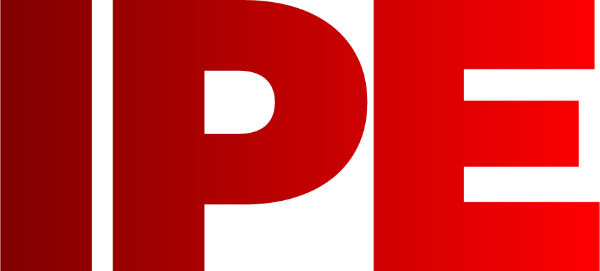
![]() |
Edward Lowton
Editor |
![]() ![]() |
1/2 (1 to 10 of 20)
New guide to reducing unplanned downtime in motor-driven systems | 27/02/2024 |
---|---|
THE ASSOCIATION of Electrical and Mechanical Trades (AEMT) has produced a new guide designed to help motor-driven equipment users minimise unplanned downtime. Unplanned downtime can have significant direct and indirect costs on a business - lost production, wasted materials and ingredients, the high cost of reactive maintenance, reputational damage and even human safety risks. In some industries, the cost can be huge, but even when the cost is not so high, unplanned downtime is unwelcome. This comprehensive new six-page guide, which can be downloaded from https://bit.ly/AEMTmdg, outlines a range of steps that users of motor-driven systems can take to minimise the likelihood of unscheduled interruptions to the operation of their systems. The AEMT’s new guide covers five key areas. The first is installation, which highlights key factors to consider when setting up and implementing a new motor-driven system, all of which can ensure it starts with a sound foundation. Ongoing routine maintenance is also featured, with suggestions around key steps to take in the short, medium, and long term. The availability of spares and how they are stored, to enable a system to be promptly and reliably recommissioned when needed, is also addressed. While how motor repairs are carried out and their impact on the ongoing reliability of a motor-driven system, is also outlined. The final area covered in the guide is condition monitoring. This section explores the areas which can be monitored and busts a few myths surrounding the topic. Commenting on the publication of the new guide, Thomas Marks, the AEMT’s secretary and general manager, said: “Our members are experts in getting to the route of issues within electromechanical systems and repairing them quickly to the highest standards. However, a lot of the failures they see could have been avoided. This new guide has been produced to give users of motor-driven systems an outline of best practices they can implement to reduce the risks of financial and reputational damage being caused by unplanned downtime.” The guide is part of a series produced by the AEMT, which also includes a guide to motor efficiency legislation and one which looks at ways to reduce a motor-driven system’s total cost of ownership. All three guides are available to download from the Association’s website. For further information on the services provided by the AEMT and its members, please call +44(0)1904 674899 or email [email protected] |
|
|
|
AI-powered tool to simplify navigating electromechanical repair and maintenance standards | 05/02/2024 |
THE ASSOCIATION of Electrical and Mechanical Trades (AEMT) is working with the British Standards Institute (BSI) and UKRI’s Driving the Electric Revolution Challenge, delivered by Innovate UK, to develop an AI-powered tool to help electromechanical repair specialists ensure they repair hazardous area motors to the correct standard. The tool, which is being developed with some funding and support from Innovate UK, will enable engineers repairing rotating electrical equipment to clarify technical requirements through an easy-to-operate chatbot-style interface. The tool under development by the AEMT and BSI aims to vastly simplify interpreting and complying with the complex BS EN and IEC 60079 series of standards while reducing the potential for error. Users of the system will be able to ask questions about the repair they are working on and be provided with the technical guidance and information required to ensure compliance and safety. |
|
|
|
Ensure you get a good quality motor repair | 21/11/2023 |
With growing financial and supply chain pressures, repairing a motor can be an increasingly viable alternative to replacement. But for a repaired motor to perform as well as, or in some cases better than, when it was new it is essential that you get a quality repair from your motor repair partner, says Karl Metcalfe THERE ARE several ways that a poor-quality motor repair can impact a business. Firstly, there could be issues with the energy efficiency of a badly repaired motor which can lead to unnecessary increases in costs. However, if repaired well, a motor should be at least as efficient as when it was new. This was demonstrated by a study carried out by the Association of Electrical and Mechanical Trades (AEMT) and the US-based Electrical Apparatus Service Association (EASA), which used independent testing facilities to confirm higher efficiency IE3 units are unaffected by a repair that uses good practice procedures. The impact of poor-quality repairs A motor that has not been well repaired can also be prone to failure earlier than expected. Winding faults can lead to premature insulation breakdown, while poorly fitted bearings can fail sooner than expected. If these unexpected faults occur, the cost of unintended downtime could be massive for some businesses. There are ways to identify a good quality repair, and this can start before the repairer even sets eyes on the motor. The repairer should take the time to understand what the client needs. They should talk to the customer to find out about the motor, where and how it is being used, and what the customer wants from the repair. When inspecting a repaired motor, generally, if the motor looks like it has been well treated on the outside, it is likely that it will have been well treated on the inside. For example, when the motor is returned, are the mounting faces free of paint? If they have been well masked when the motor was painted, the motor will be much easier to mount accurately. Equally, if the terminal box looks nice and clean and there are new nuts and washers on the terminals, that would be a sign that care has been taken. Other small but notable signs include the fitting of new grease nipple caps. They cost a few pence but can make a big difference. Also, look for mesh wrap or some form of protection on the shaft. While silica gel packs inside the terminal box and anti-corrosion coatings can make a difference, especially if the motor may not go straight into service and is in storage for any time. The International Repair Standard One way to ensure a quality repair is to ask your provider if they follow the international repair standard (IEC 60034-23). The standard establishes the benchmarks for repairing rotating equipment, maintaining efficiency levels, high standards of quality control and improving efficiency in associated pieces of equipment. The standard covers many other aspects of the repair process. It sets out requirements for the maximum temperatures used in an oven to burn off old windings to prevent damage to the steel laminations. It covers which insulation grades should be used, the approach to rebuilding bearing seats, the selection of replacement bearings and grease, and a range of other factors. IEC60034-23 also sets out what tests should be carried out on a motor before and after it is repaired and how the test equipment should be maintained and calibrated. In line with the repair standard, a good motor repairer should have a repair specification they can give customers, showing what will be done. And when the motor comes back from repair, there should be an accurate record of what has been done, including certificates covering aspects such as balancing, vibration measurement, tolerances, and surge test results. So, to ensure you get levels of reliability and efficiency from your next motor repair, ask your repair provider if they work to the international repair, overhaul and reclamation of rotating equipment standard, IEC 60034-23. Karl Metcalfe is technical support at the Association of Electrical and Mechanical Trades For more information: Tel: 01904 674899 |
|
|
|
AEMT moves to support equality, diversity and inclusion across its sector | 14/08/2023 |
WITH SUPPORT from its members, the Association of Electrical and Mechanical Trades (AEMT) has launched a committee which aims to drive, support and promote equality, diversity and inclusion within the electromechanical sector. In the UK, the engineering sector has a long-standing history of being less diverse than the general population. Research from EngineeringUK shows that 16.5% of those working in engineering are female compared to 51% of the working-age population, while 9% are from minority ethnic backgrounds compared to 12% of the population, and 9% declare they have a disability or impairment as compared with the average of 14%. At a time when the engineering sector faces a widespread skills shortage, a focus on equality, diversity and inclusion (EDI) offers a broader talent pool to help meet the sector’s recruitment needs. Research also demonstrates that increased workforce diversity improves innovation, creativity, productivity, resilience and market insight. A study carried out by McKinsey has shown that companies in the top quartile for racial/ethnic diversity were 30% more likely to have financial returns above their national industry median, while those in the top quartile for gender diversity were 15% more likely to have increased financial returns. The business case for EDI in engineering is undoubtedly there, but many organisations in the sector are unsure of how they can improve their position or, indeed, what support and resources are available to them. The AEMT’s new group aims to help its member companies to develop their approach to EDI within their organisations and reap the available rewards. This work will include identifying and sharing best practices, signposting members to resources and initiatives to support them on their journey, and raising awareness of the benefits a focus on EDI can deliver. The group will also work to encourage individuals from diverse backgrounds and experiences, and those with wide-ranging needs, to explore careers in the electromechanical repair sector by promoting the opportunities available in the industry and highlighting the way EDI is supported. The new AEMT committee was formed by a group of Association members with experience promoting and supporting EDI within their businesses. Members of the committee include representatives from Houghton International, ABB, ADC Electrical, Bedford Pumps, EMiR Software, Fenflow, Hidrostal, Mid Kent Electrical and Primary Engineer. Commenting on the new group, Kirstie Davies, Marketing Manager at EMiR Software, said: “The electromechanical sector is facing a skills shortage as young and diverse individuals are not choosing to enter the sector. I believe we will benefit significantly from promoting and actively engaging in diversity and inclusion, as companies that celebrate diversity and inclusion are seen as more progressive and attractive to customers, employees and investors. Lucy Ogden, Marketing Manager at Hidrostal (GB) Ltd, added: “We strive to make our engineering workforce diverse, equitable and inclusive. At 25%, our proportion of female staff is well above the UK average, plus we have diverse role models, particularly within our leadership team, who show our staff that there are no limits to their progression within our organisation. Employing a diverse workforce benefits our business in many ways. It extends our skill set and provides us with a wider range of perspectives, plus it increases our productivity by enabling us to blend our experiences and learn from each other. Ultimately, our employees are happier.” Eleanor McIntosh, Marketing Manager at Houghton International, explained how her company works to embed an EDI focus across the business: “With support from a well-established HR team Houghton International embeds effective policies and procedures, health and wellbeing support, a strong internal culture and set of core values throughout recruitment, training and apprenticeships, staff retention, development, performance management, and business operations. Within our workforce there is the representation of ages from 16 to 60+, giving us the benefit of decades of experience alongside innovative young minds and fresh perspectives. In a traditionally male-dominated industry, the number of women within the business has increased steadily. With many women within the business routed into significant career development and progression.” One of the group’s first actions was to sign the Association up as a supporting partner of EngineeringUK’s Tomorrow’s Engineers Code, a community of over 250 organisations working toward common goals to increase the diversity and the number of young people entering engineering careers. This move sees the Association commit to actively participating in the Code’s community, contributing where applicable and sharing knowledge/good practice. |
|
|
|
AEMT announces new president | 28/07/2023 |
AT ITS recent AGM, the Association for Electrical and Mechanical Trades (AEMT) announced the appointment of James Stevens as its new honorary president, taking over the position from outgoing president, Central Group director Shaun Sutton. The organisation's AGM was held exclusively online, enabling a wider portion of the Association's Council and Membership to attend the annual event. Stevens, a director at coil winding manufacturer and supplier Preformed Windings, took the president's position after spending the previous two years as vice president. "I'd like to acknowledge the fantastic work that Sean Sutton has been doing over the last two years. He's seamlessly integrated the council with the staff of the AEMT, working closely with the general manager and the rest of the team to implement significant improvements in the Association, including clarifying the vision and mission and introducing a coaching styled approach to all interactions with the team. He has left me in that unfortunate position of filling some really big shoes. But I look forward to the challenge and our continued work together," said Stevens. "When I joined Preformed Windings, the AEMT provided invaluable information and networking opportunities. Since then, I've enjoyed collaborating with the Association and particularly enjoyed activities such as the peer group, which sees everyone benefiting from the wealth of knowledge within our membership. "So, as I embark on my term as president, my vision is to build upon the fantastic work that's been done over the past few years by Shaun and the wider team, building those clear value propositions for our members, and I'd specifically like to focus on the engagement of all of our membership groups including the international members, building opportunities for knowledge sharing at all levels and increasing our membership base. "I'm truly honoured to be named the president of the AEMT," he added. In addition to appointing a new president, Mark Brady, director at electromechanical repair specialist Haley247, took over the role of vice president and Andy Patten from ADC Electrical became junior vice president and interim treasurer. Commenting on his time in office, outgoing president Shaun Sutton said: "I have thoroughly enjoyed my time as president and the opportunity to contribute to shaping the ongoing direction of our Association. A key area of focus for me during my time in office has been the people within our membership. And by that, I mean all the people working within our member organisation. "I believe in collaboration and the power of sharing knowledge and experience, and I hope as I leave my position, the Association has grown in those vital areas, and our membership has benefited as a result," he affirmed. |
|
|
|
Can a repaired motor be more efficient? | 12/05/2023 |
When it comes to upgrading motors, it's not always possible to swap out an older motor for a more modern alternative. Reflecting this, there are a variety of considerations when looking at how a motor's efficiency can be improved as part of a repair or refurbishment, says Thomas Marks AGAINST A backdrop of increasing energy costs, significant savings can be made by upgrading old motors to more efficient modern alternatives. However, simply swapping a motor for a modern equivalent is not always practical or even possible. With this in mind, when looking at how a motor's efficiency can be improved as part of a repair or refurbishment, there are several things you should consider. A study carried out jointly by the Association of Electrical & Mechanical Trades (AEMT) and the American Association, the Electrical Apparatus Service Association (EASA), has shown that motor efficiency can widely be maintained when a repair is carried out to a defined set of standards.The findings of the 2019 study, established that efficiency was maintained on repairs to current machines up to IE3 efficiency. Improving motor efficiency There are, however, some circumstances under which the efficiency of a motor can actually be improved by refurbishment and rewinding. This generally applies to older, less efficient motors and the decision to repair rather than replace typically involves a broader range of factors than simply to improve efficiency. Generally, the most effective way to improve a motor's efficiency is to add more copper to its coils. It is often possible to add more copper to a set of coils, or, more specifically, increase the copper cross-sectional area. This is achieved through the very tight tolerances modern coils can be manufactured to and the ability of state-of-the-art CAD systems to optimise coil design. This has several benefits, such as reducing the coil's resistance, increasing the potential output, and reducing the operating temperature of the machine, which can increase an asset's life. Taking care with copper It is, however, important to understand that adding more copper will affect other characteristics in a motor which may require the wider system to be adapted. Adding more copper into a machine will affect not only efficiency but also other parameters. For example, an increased inrush-current - which might be in conflict with existing protective measures - should be expected. The ability to increase the amount of copper in a motor has been supported by advancements in insulation materials' which means that less insulation is required, and therefore space in the motors' slots becomes available. The thickness of insulation needed for various voltage systems has significantly decreased over the years, and modern insulation systems can offer 15% reductions in thickness. As this is on the outside of the coil, the effect on the copper cross-sectional area can be greater still. Furthermore, these thinner insulations assist with heat dissipa tion and can again offer both an increased asset life and improved efficiency of the coils. Comparing pre- and post-repair efficiency It is worth noting, however, that care is needed when comparing pre- and post-repair efficiency levels in a motor. Efficiency should not be compared simply by looking at a motor's datasheets. Before a 2007 update of the IEC / EN 60034-2-1 standard, which defines methods of determining a rotating machine's efficiency, efficiency figures were more generous due to how certain effects could be calculated out. Efficiency levels could previously be calculated with smaller additional losses than today - a standard 0.5% of absorbed power, regardless of the motor output. Since the 2007 update, the methods have become much stricter. Now stray load losses have to be determined by a factor that reflects the motor's output, ranging from 0.5% (≤1MW) to 2.5% (≥10MW). So, to avoid potentially misleading comparisons calculated from individual losses, efficiency should be measured directly at nominal load. Thomas Marks is general manager and secretary at the AEMT For more information: Tel: 01904 674 899 |
|
|
|
Commissioning motors for reliable and efficient service | 22/02/2023 |
There are a number of key steps that should be taken when commissioning motors which have been in storage or removed for repair, says Karl Metcalfe CAREFUL INSTALLATION of motors will help ensure their efficient and reliable operation, minimising the potential for costly downtime or sub-standard operation. It is therefore essential that particular care is taken when installing and starting motors that have been in storage or that have been subject to an off-site repair. Stored motors A motor which has been in storage should first be cleaned to bring it back to the condition it was in when placed in storage. If there are any signs of damage, such as broken cooling fins, they should be investigated to assess whether any internal damage could have occurred and, where necessary, the damage repaired. In an ideal scenario, motors should be stored in a vibration-free environment; however, this is not always practical. If the motor under inspection may have been subject to vibration, there is a potential for the bearings to have been damaged. Even minimal ambient vibration will cause motor bearings to wear over time and can result in fretting or false brinelling, which can lead to motor failure. Therefore, unless there is complete certainty that the stored motor was not subjected to any vibration, the bearings should be inspected for signs of wear and replaced if necessary. Maintaining your bearings Bearing lubrication should also be considered when taking a motor from storage. Where the motor uses sealed bearings, if it has been in storage for an extended period of around two years or more, it is highly likely that the grease inside the bearing will have separated and will not work optimally. If the date when the bearing was fitted is unknown, or the motor has been in storage for a long time, then it would be advisable to replace the bearing. Motors which utilise re-greaseable bearings should be regreased. And if there are any signs of water in the grease purged from the motor, there will likely be rust damage, and the bearings should be replaced. All stored motors will be subject to some degree of temperature fluctuation, and this will cause the seals to expand and contract, allowing moisture to enter the motor. Where the motor is oil-lubricated, it is, therefore, good practice to change the oil before starting it after a long period of inactivity. To minimise the likelihood that the motor’s windings are contaminated by oil, it is advisable to drain the oil before it is moved from its storage location and then refill it after it has been installed. If good practice was followed when the motor was put into storage, an insulation resistance (IR) test, which measures the total resistance between any two points separated by electrical insulation, should have been carried out. This test determines how effective the insulation is in resisting the flow of electrical current. Before putting a motor back into service, repeat this test to ensure that any decreases in insulation effectiveness that may have occurred during storage can be addressed. Repaired motors If an AEMT member has repaired the motor, it is likely to have been done following the international repair, overhaul and reclamation of rotating equipment standard, IEC 60034-23:2019, and it is a good idea to check if this has been followed. The standard establishes the benchmarks for repairing rotating equipment, maintaining efficiency levels, high standards of quality control and, where possible, improving efficiency in associated pieces of equipment. As such, bearing checks, lubrication procedures and insulation resistance testing will all have been carried out to the highest standard. However, the following checks should also be carried out on repaired motors, as well as stored motors. Before putting a motor into service, manual rotation of the shaft should be carried out if size allows. If the shaft doesn't spin freely by hand or doesn't quite sound as it should, the bearings should be checked for damage that may have occurred during transport. It is essential that the wiring of a motor is carried out or checked by a suitably qualified electrician, and the equipment must be earthed in accordance with current regulations. It is also essential that the motor is securely mounted and accurately aligned in all three planes - allowing for shaft end float and thermal expansion. Start your motors Before the motor is fully put into service, it should be briefly started. If any vibrations or unusual noises are experienced, the motor should immediately be de-powered to examine the causes. Vibration or noise caused by magnetic or electrical issues will typically improve as soon as the power is switched off. If there is no change when the power is disconnected, misalignment or balance issues are more likely to be the cause. Assuming no issues have been identified, all safety measures have been put in place, and the parameters relating to the motor’s specification (such as supply voltage and cable sizes) have been met, the motor can be put into service. After around an hour of running at normal load, the vibration levels should be checked. If they are excessive, the alignment or belt tensioning should be re-checked. It is worth noting, however, that there may be a degree of bearing noise for the first few hours of operation as the grease settles, but this should soon disappear. Once the motor and load are running as expected, the full load voltage and current for all phases should be recorded, along with the input power under load. If the motor has the capability, the bearing and winding temperatures should also be recorded once they have stabilised. This information will help with future maintenance and assessment of the motor. Where the application is critical, and a predictive maintenance programme is planned, the full vibration signature of the motor and its load should be recorded as a baseline. If the correct procedures are carried out when installing and commissioning a stored or repaired motor, it is far more likely to have an efficient and reliable operational life. Of course, a sound maintenance programme is also required, but if the starting position is strong, the ongoing maintenance requirements should also be reduced. Karl Metcalfe is technical support at the Association of Electrical and Mechanical Trades (AEMT) For more information: Tel: 01904 674899 |
|
|
|
Ensuring a good quality motor repair | 06/10/2022 |
With growing financial and supply chain pressures, repairing a motor can be an increasingly viable alternative to replacement. But for a repaired motor to perform as well as, or in some cases better than, when it was new it is essential that you get a quality repair from your motor repair partner. Karl Metcalfe, technical support at the Association of Electrical and Mechanical Trades, explains what to look for when commissioning a repair. THERE ARE several ways that a poor-quality motor repair can impact a business. Firstly, there could be issues with the energy efficiency of a badly repaired motor which can lead to unnecessary increases in costs. However, if repaired well, a motor should be at least as efficient as when it was new. This was demonstrated by a study carried out by the Association of Electrical and Mechanical Trades (AEMT) and the US-based Electrical Apparatus Service Association (EASA), which used independent testing facilities to confirm higher efficiency IE3 units are unaffected by a repair that uses good practice procedures. How to identify a good quality repair A motor that has not been well repaired can also be prone to failure earlier than expected. Winding faults can lead to premature insulation breakdown, while poorly fitted bearings can fail sooner than expected. If these unexpected faults occur, the cost of unintended downtime could be massive for some businesses. There are ways to identify a good quality repair, and this can start before the repairer even sets eyes on the motor. The repairer should take the time to understand what the client needs. They should talk to the customer to find out about the motor, where and how it is being used, and what the customer wants from the repair. When inspecting a repaired motor, generally, if the motor looks like it has been well treated on the outside, it is likely that it will have been well treated on the inside. For example, when the motor is returned, are the mounting faces free of paint? If they have been well masked when the motor was painted, the motor will be much easier to mount accurately. Equally, if the terminal box looks nice and clean and there are new nuts and washers on the terminals, that would be a sign that care has been taken. Other small but notable signs include the fitting of new grease nipple caps. They cost a few pence but can make a big difference. Also, look for mesh wrap or some form of protection on the shaft. While silica gel packs inside the terminal box and anti-corrosion coatings can make a difference, especially if the motor may not go straight into service and is in storage for any time. International repair standard One way to ensure a quality repair is to ask your provider if they follow the international repair standard (IEC 60034-23). The standard establishes the benchmarks for repairing rotating equipment, maintaining efficiency levels, high standards of quality control and improving efficiency in associated pieces of equipment. The standard covers many other aspects of the repair process. It sets out requirements for the maximum temperatures used in an oven to burn off old windings to prevent damage to the steel laminations. It covers which insulation grades should be used, the approach to rebuilding bearing seats, the selection of replacement bearings and grease, and a range of other factors. IEC60034-23 also sets out what tests should be carried out on a motor before and after it is repaired and how the test equipment should be maintained and calibrated. In line with the repair standard, a good motor repairer should have a repair specification they can give customers, showing what will be done. And when the motor comes back from repair, there should be an accurate record of what has been done, including certificates covering aspects such as balancing, vibration measurement, tolerances, and surge test results. So, to ensure you get levels of reliability and efficiency from your next motor repair, ask your repair provider if they work to the international repair, overhaul and reclamation of rotating equipment standard, IEC 60034-23. For more information: Tel: 01904 674899 |
|
|
|
AEMT awarded funding to develop Ex training platform | 12/08/2022 |
The Association of Electrical and Mechanical Trades (AEMT) has been awarded funding by Innovate UK to support a knowledge transfer project (KTP) with the University of York. THE PROJECT will see the development of an online platform for the delivery of the association's internationally renowned hazardous area equipment repair courses. The 24-month-long project aims to take the courses, which are currently delivered in face-to-face sessions, online through a virtual learning and assessment environment where delegates can 'handle' virtual machinery and equipment to understand key principles of the design elements. The hazardous area, or Ex, courses are delivered across the globe, and in 2019 the association delivered training in 20 countries to delegates from 40 countries. However, during the COVID pandemic, this delivery was significantly affected, and it became apparent that an online option was needed. But it was clear that transferring the courses to a digital environment would not be a straightforward task. The in-person training requires a large amount of interaction with Ex equipment to understand how it operates and must be repaired, plus the assessment of the delegates' competencies is very much a practical activity. To identify an approach that would cover the needs for interaction and assessment, the association approached the University of York, which it had worked with before. The University proposed using interactive, interrogatable models, known as virtual twins, to deliver the hands-on environment. This cutting-edge approach will allow course delegates to examine and explore the equipment previously taken to each course, from anywhere in the world with an internet connection. "We typically visit 20 countries a year to deliver our Ex training, with delegates travelling across borders to attend the courses," said Thomas Marks, the AEMT's general manager and its lead on the project. "A fundamental value of the AEMT is to support and drive sustainability – it's what our members do, repairing and remanufacturing electromechanical equipment to extend its life. So, aside from broadening the reach of our training and improving our resilience, the chance to reduce the significant amount of travel required by delegates and our lecturers will have a hugely positive impact on our carbon footprint." Hamed Ahmadi, a lecturer at the University of York and the project's lead academic, added: "As well as benefiting the training the AEMT carries out, this project will support our delivery at the University. The lectures we deliver for our engineering courses require significant practical activity. During the pandemic this presented challenges when lectures had to move online. Developing the work carried out with the association will give us greater flexibility and improved resilience." The project will run for two years, with a beta release scheduled for the first quarter of 2023. This will enable the project team to gather user feedback to factor into the platform's development ahead of its full launch, which is scheduled for the second quarter of 2024. Once the Ex training courses are fully operational, the association plans to bring other training relating to the repair of electromechanical equipment to the platform. |
|
|
|
Fletcher Moorland rewards hard working staff | 27/04/2022 |
AEMT MEMBER, Fletcher Moorland, has moved to support staff through the cost-of-living crisis with a ex-gratia payment. A longstanding member of the Association of Electrical and Mechanical Trades (AEMT), the Staffordshire-based firm has received widespread recognition, including in the national media, after it announced plans to give every staff member an ex-gratia payment of £1,000. The move, which received a standing ovation when announced at an all-company meeting, aims to help the firm’s 86 staff tackle rising costs, including fuel and energy prices. This payment is on top of the yearly pay rises the company extends to all staff. With its focus on the maintenance and repair of electrical, mechanical, and electronic equipment across manufacturing, building services, utilities and many other industries, the company has seen growth over the past two years despite COVID, and particularly so in the renewable energy and electric transport sectors. "We have a dedicated and loyal team here at Fletcher Moorland who have all worked extremely hard over the last few years, sometimes in challenging circumstances. As the whole country is facing a cost-of-living increase, we wanted to do something to support our employees and, thankfully, we were in a position to do so. We recognise how important our people are to the business, and the decision to help them was a no-brainer," said Matt Fletcher, the company's managing director. With engineering-based businesses facing a skills shortage like many other sectors, the AEMT is actively working with organisations such as Primary Engineer, designed to encourage young people to take up careers in the industry. However, retaining staff is equally important, particularly in today’s climate. And so, the Association is delighted to see one of its members demonstrating how recognising and rewarding the value of existing staff can mean so much, especially when times are tough. |
|
|