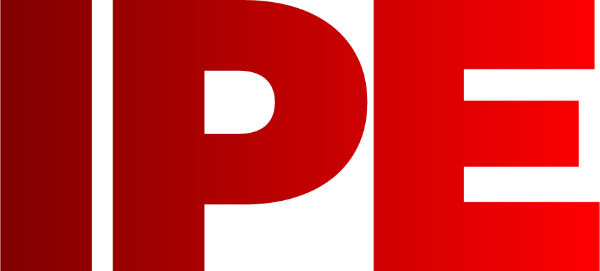
![]() |
Edward Lowton
Editor |
![]() ![]() |
1/76 (1 to 10 of 758)
Starrag presents new 5-axis Heckert machine | 14/08/2025 |
---|---|
STARRAG HAS launched the Heckert X80, a versatile 5-axis machining centre that delivers exceptional precision and productivity within a compact footprint. Building on the acclaimed Heckert HEC series, the Heckert X80 features a workpiece-side swivel unit, allowing for high-dynamic 5-axis machining from a single clamping position. The Heckert X80's lightning-fast 65 m/min traverse rate and industry-leading changeover times enhance productivity. Pallet changes are completed in just 21 seconds, whilst the tool changer provides chip-to-chip times of only 8 seconds. Standard 800 by 1000 mm pallets incorporate Starrag's precision-engineered concave surfaces with 6 µm curvature depth, ensuring stable positioning of large parts. The Heckert X80 offers X, Y, and Z axis travel of 1450 by 1300 by 1300 mm while requiring 18% less installation space than its HEC Series predecessor. It accommodates workpieces with a core contour diameter of 1200 mm and a maximum height of 1000 mm, supporting loading masses of up to 1200 kg. Within robust dimensions of 8.5 m by 4 m, the X80 delivers exceptional space utilisation without compromising performance. The Heckert X80 provides a range of spindle options that cater to specific application requirements, from 12,500 rpm hollow shaft spindles to 15,000 rpm motor spindles, as well as various gear spindles that offer increased torque for heavy machining. Starrag's innovative tool change system offers both lightweight and heavy-duty versions. The lightweight option accommodates tools weighing up to 22 kg, while the heavy-duty version supports tools weighing as much as 50 kg. The maximum tool dimensions are 800 mm in length and 340 mm in diameter. Tool magazine options include timing belt magazines with 45 or 60 positions for HSK-100 tools, chain magazines accommodating up to 120 HSK-100 tools, and tower magazines supporting up to 440 HSK-100 tools. Turning technology is integral to the machine concept and available as an option. Using specially developed assemblies and software modules, both classic and complex turning operations can be performed with machining centre productivity levels. Unlike turning centres, the machine benefits from versatile setup options, including vertical workpiece clamping and mid-operation clamping via the pallet changer. For optimal operator experience, the Heckert X80 boasts Starrag's ergonomic 24-inch touchscreen HMI paired with a powerful Siemens SINUMERIK ONE control system. The touch-sensitive display responds to gloves and features a scratch-resistant, easy-to-clean surface. Operators can access PDF construction plans and sequence sketches while maintaining visibility in the workspace through an integrated camera. New hardware and rapid sensor technology enhance automation capabilities via extended 13-channel clamping hydraulics and optimised standard interfaces for pallet storage systems and robot cells. Efficient chip management employs a thermo-symmetric design and steep-angled fixed plates, enhanced by an internal coolant supply operating at pressures of up to 80 bar. This setup ensures effective cooling and chip evacuation, with an additional flushing capability of up to 280 litres per minute for applications that generate a high volume of chips. The Heckert X80 integrates with Starrag's comprehensive automation solutions, including Fastems FPT round pallet store systems, linear storage systems, and robotic cells, catering to production requirements from small to large batch sizes. The new Heckert X80 utilises the proven four-axis Heckert H-series machine envelope. Instead of the NC rotary table from the H-series, X-series models feature a robust rotary/tilt table developed and manufactured in-house at Starrag's Chemnitz plant. The tilting unit incorporates two equally sized bearings and a thermally stable design, enabling five-sided, highly dynamic machining of complex components. Ensuring pallet compatibility across the new Heckert X80, smaller X70, and larger X90 models was essential for developers. Pallets are interchangeable with Heckert H series machines and older Heckert HEC 630/800 X5 machines. The Heckert X80 is now available as part of Starrag's expanded X-series line of five-axis machining centres. Manufacturers can view the new Heckert X70 at EMO Hannover in September. The Heckert X-series includes the smaller Heckert X50 and the larger Heckert X80 and X90 variants, offering enhanced work envelopes and capacity. |
|
|
|
AITT is excited to exhibit at IMHX 2025 | 13/08/2025 |
AITT - THE UK's fastest growing accrediting body for workplace transport training - is excited to announce its exhibition at IMHX 2025 from the 9-11 September. "As the only member-run accrediting body in this industry, we pride ourselves on fostering good working relationships with every member, from individual trainers to large national companies," said AITT MD Liam Knight. "IMHX is a great opportunity for us to catch up with members in attendance and answer any questions in person. For visitors who are not yet AITT members, this will be a chance for us to share our knowledge on how to maintain training standards for operators, instructors, and tutors. We will be at stand F37, so come and say hello." As an added incentive, AITT will be offering current members the chance to enter a free prize draw to win a year's membership by simply scanning details at the stand. Plus, anyone who signs up on the day as a new member will get the rest of 2025 free. "IMHX is a fantastic industry event. We’re looking forward to meeting attendees and sharing our insights into how AITT accreditation can ensure the highest training standards on all types of workplace transport and material handling equipment," Knight continued. Visit stand F37 at IMHX 9-11 September 2025 for the chance to win a year’s free membership |
|
|
|
Combining sustainability with lifting power: Sarens introduces new SGC-170 | 08/08/2025 |
THE NEW model represents one of the most powerful land-based cranes in the world, second only to the SGC-250, holding the record as the largest land-based crane globally for six years. Designed entirely at Sarens' facilities, the new SGC-170 crane has fewer connections and larger components to enable faster mobilisation and assembly. Its reinforced structure allows it to be transported in less than a week and adapted to all types of situations. The new SGC-170 crane is also committed to the environment, with a fully electric system that produces zero emissions, cutting energy consumption by up to 40%, and returns the unused energy to the grid. Sarens, world leader in heavy lifting, engineered transport and crane rental services, has introduced the new member of its range of giant cranes, the SGC-170, a model with the highest load and lifting capacities, second only to the SGC-250, considered the largest land-based crane on the planet for six years. The new Sarens model is able to reach a load capacity of 170,000 T/m and exceed a lifting capacity of 3,200 tons. Its main boom with jib can lift 1,300 tons at over 200 metres, a demonstration of its total precision and power. The new crane has been developed entirely by Sarens’ R&D team at its Wolvertem (Belgium) facility and represents another leap forward in performance and efficiency. The new SGC-170 thus rounds out Sarens’ range of electric cranes, which already included the SGC-90 (also known as “Little Celeste”), offering unprecedented lifting capacity that places it among the most powerful land-based cranes in the world and makes it the benchmark for large-scale projects. As an electric crane, the new Sarens SGC-170 eliminates the need for hydraulic pumps, filters and diesel engines, slashing maintenance requirements and boosting overall efficiency. The model incorporates an energy-recovery system that activates when lowering loads or moving the main boom—which can extend up to 155 metres. The regenerated electricity can be reused for other crane movements, while any surplus can be fed back into the grid. Thanks to this system, the SGC-170 can cut energy consumption by up to 40%. The latest addition to Sarens’ giant-crane family also remains fully committed to efficient assembly. The SGC-170 uses fewer internal connections and larger, more manageable components, easing transport and installation. Its reinforced structure allows it to be commissioned in only 4 to 6 weeks from its arrival on site, requiring only one week to be relocated on site. It is therefore ideal for large offshore wind projects, petrochemical installations, major infrastructure works and nuclear sites, where tight spaces, heavy lifts and the need to optimise operating costs are critical. "Ten years ago, plugging a crane like this into the grid would’ve been unthinkable. Now, we’ve built a machine that’s not only more efficient and sustainable, but one that’s ready for the most demanding jobs, anywhere in the world," said Matthias Sarens, head of design at Sarens. Sarens's new venture completes the company's family of giant cranes, with members of recognized international prestige such as the SGC-250 - known as “Big Carl”, and key in the development of the Hinkley Point C nuclear power plant in the UK -, the SGC-140 “Big Benny XL”, the recently unveiled SGC-120/1 or the SGC-90 - known as “Little Celeste” -, a ring crane powered only by electricity, which is capable of returning the energy produced and not used to the grid. |
|
|
|
Proven HBK Force Measurement Technology goes digital with IO-Link | 05/08/2025 |
GLOBAL LEADER in precision measurement solutions, Hottinger Brüel & Kjær (HBK) is proud to introduce digital connectivity to its trusted U2B and C2 force transducers, now available with an IO-Link interface. This enhancement makes it easier than ever to integrate tensile and compressive force measurements directly into control systems. For years, the U2B (tensile and compressive) and C2 (compressive) series have been essential tools in production, monitoring, and testing environments worldwide. With a nominal force range from 500 N to 200 kN, these sensors are known for their reliability and precision. Now, in addition to analogue outputs (4 - 20 mA and 0 - 10 V), users can opt for a digital output via IO-Link - which ensures smarter data handling and improved system integration. The IO-Link Integration provides engineers with many benefits:
HBK also offers IO-Link-enabled sensors for torque and weight, expanding the possibilities for smart, connected measurement solutions. More information is available on the company’s website www.hbkworld.com/en/products/transducers/force/c2 |
|
|
|
Esh-Stantec and Hauff-Technik collaborate to improve sealing solutions in UK water sector | 04/08/2025 |
A GROUND-BREAKING collaboration between Esh-Stantec and German-based sealing technology specialist Hauff-Technik is being trialled across the North East with innovation, efficiency, and sustainability at its core. The two organisations have been working together for the last year to explore more efficient sealing methods and are introducing press and link seals on live projects in a step away from more traditional sealing methods. |
|
|
|
Technidrive expands Drum Drive range | 23/07/2025 |
TECHNIDRIVE HAS extended its Drum Drive range to meet growing demand for electrified, energy-efficient conveyors across heavy industries. The latest additions offer greater torque capacities, flexible mounting and reduced maintenance - helping operators meet both operational and sustainability goals. |
|
|
|
Liebherr ship-to-shore cranes assembled efficiently at Valencia port | 18/07/2025 |
CARGO PORTS handle thousands of ships every year. Efficiently offloading and loading vessels is essential for their smooth operation and maintaining global supply chains. Many ports however face capacity constraints, with newer lifting equipment required to accommodate bigger ships and loads. When it comes to container crane installations at ports, work must be carefully managed to minimise disruption and avoid interfering with operations. The Port of Valencia took delivery of two Liebherr ship-to-shore container cranes in large, preassembled components, for integration on site. Building these giants in one of the Mediterranean’s busiest seaports would require expert forward planning and efficient execution. Building off-quay to minimise disruption Both STS cranes were shipped from the Port of Fenit, Ireland, to the Port of Valencia, in Spain. Their components were offloaded onto SPMTs using the delivery vessel’s crane. The largest of these were the main beam and the derrick boom, which measured 69.6 and 76.3m meters, respectively. Almost 90 axle lines of SPMTs were used on the project to move the components safely across the site. Once the components were taken to the assembly area, Mammoet used crawler cranes, telescopic cranes, cherry pickers and forklifts to begin assembly of the first crane. The working cranes had different capacities across the different stages of the project. The telescopic cranes had lifting capacities of between 80t to 250t; the two crawlers each had a capacity of 600t. The telescopic crane worked with the crawlers to top and tail the main frame sections – performing a tandem lift to place them in the vertical upright position and onto bogies. During the project, Mammoet, along with engineers from Liebherr, managed different teams of sub-contractors to make all the mechanical and electrical connections between the different components. Once both cranes were assembled, they were driven to their final position on the quayside. For this stage, SPMTs was used but fitted with two interfacing transport beams to help spread the load and connect the crane’s landside frame to its seaside frame for stability. The STS cranes have a transport bracket on each of their four legs. The SPMTs were driven underneath the cranes, and the transport beams were connected to these brackets. Once everything was securely fastened, the STS cranes were lifted using the on-board stroke of the SPMT. They were then driven 600 meters to the quayside and lowered into their longitudinal rails. A full-service solution for project efficiency "As soon as the components were delivered, they were immediately taken away from the quayside to allow operations to continue. The installation process was equally as quick, minimising disruption," said Javier de Pablo Arenzana, sales manager at Mammoet. "We have worked with Liebherr for many years and across a number of different projects. Liebherr value our expertise and experience and are proud to be one of Liebherr’s key partners for this kind of work." |
|
|
|
Blueshift's AeroZero Flame and Thermal Barrier (AZ-FTB) Passes All Ten Cycles of the UL 2596 Torch and Grit Test | 29/07/2025 |
BLUESHIFT'S AEROZERO Flame and Thermal Barrier (AZ-FTB) material, has become one of the first thin profile TPS to pass and complete all 10 cycles of the UL 2596 Torch and Grit Test (TaG). Therefore, proving its market-leading performance in helping to mitigate the risk of thermal runaway in electrically powered aerospace applications. UL 2596, Test Method for Thermal and Mechanical Performance of Battery Enclosure Materials, Torch and Grit Test (TaG), is designed to provide a standardised approach for assessing the impact of explosions on electric battery enclosures. The TaG exam involves the exposure of an alternating pattern of flame (~15 seconds) and alumina ejecta (~5 seconds) onto a material sample. The twenty second alternating cycles are repeated up to 10 times, after which the material is said to have passed. The test is designed to prove the performance and durability of battery materials against the extreme temperatures and mechanical abrasion can rapidly cause failure within a battery system during a thermal runaway event. Blueshift’s AeroZero Flame and Thermal Barrier (AZ-FTB) successfully passed all 10 cycles of the TaG test, proving resilient against high-intensity flame and grit cycles at temperatures reaching 1200 °C and power levels of 3 kW. Despite its light weight and thin profile, no breaches or material failures were observed in all samples tested, highlighting the material’s exceptional resistance to extreme thermal runaway events. Lawino Kagumba, VP applications and research of Blueshift, reports that this reinforces Blueshift as a disrupter in the advanced material sector for electric aircraft and aerospace industries: "This marks a significant accomplishment for Blueshift as one of the first companies to produce a thin profile and light weight material capable of withstanding all 10 cycles of the challenging UL Torch and Grit test. This is a testament to our material’s unique capabilities and its potential to transform how design engineers approach battery module design." The tests were performed at UL Solutions’ Northbrook, Illinois facility following a demand for safer, more resilient battery systems. |
|
|
|
Starrag presents new 5-axis Heckert machine | 24/07/2025 |
STARRAG HAS launched the Heckert X70, a versatile new 5-axis machining centre designed to deliver exceptional precision and productivity within a compact footprint. Building on the exceptional features of the acclaimed Heckert HEC X5 series, the Heckert X70 incorporates a swivel unit on the workpiece side, facilitating high-dynamic 5-axis machining from a single clamping position. Receiving its world premiere at the EMO show in September on Stand C35 in Hall 12, the Heckert X70 offers impressive technical specifications with X, Y and Z axis travel of 1200 by 1100 by 1200mm. The compact machine requires 18% less installation space than its predecessor, the Heckert HEC 630 X5. It accommodates workpieces with a core contour diameter of 960 mm and a maximum height of 800 mm, supporting a loading mass of up to 1000 kg, demonstrating no change to the working area. Within its robust and spacious dimensions of 8,150 mm by 3,700 mm, the Heckert X70 offers exceptional space utilisation without compromising performance. Furthermore, turning as a technology is an integral part of the machine concept and can be configured as an option. Using specially developed assemblies and software modules, both classic and complex turning operations can be performed with the unrivalled productivity of a machining centre. Unlike a turning centre, the machine benefits from various setup options. Not only can the workpieces be clamped vertically for added convenience, but they can, in fact, be clamped during the machining operation thanks to the pallet changer. The Heckert X70's lightning-fast traverse rate of 65 m/min and industry-leading component changeover times enhance productivity. Pallet changes are completed in just 17.5 seconds, and a tool changer provides a chip-to-chip time of only 7.4 seconds. The machine's standard pallet dimension of 630 by 800 mm incorporates Starrag's precision-engineered concave surfaces with a curvature depth of 6 µm, ensuring stable workpiece positioning of large parts. It features Starrag's innovative tool change system, available in both lightweight and heavy-duty versions. The lightweight option accommodates tools weighing up to 22kg, while the heavy-duty version supports tools as heavy as 50 kg. The machine can handle tools with a maximum length of 800 mm and a diameter of 340mm. Customers can choose from a range of tool magazine options, including a timing belt magazine with 45 or 60 positions for HSK-100 tools, an chain magazine with a capacity of up to 120 HSK-100 tools, and a tower magazine capable of supporting up to 440 HSK-100 tools. The Heckert X70 also offers a broad range of spindles to meet specific application requirements, with options varying from a 12,500rpm hollow shaft spindle up to a 15,000 rpm motor spindle and different gear spindles with more torque for heavy machining. For optimal operator experience, the Heckert X70 features Starrag's ergonomic 24-inch touchscreen HMI. The control system supports the powerful Siemens SINUMERIK ONE, ensuring intuitive operation even when wearing gloves. The touch-sensitive display remains responsive to gloves and has a scratch-resistant, easy-to-clean surface. Operators can effortlessly access PDF construction plans and sequence sketches while maintaining a clear view of the workspace through an integrated camera. With new hardware and fast sensor technology, the new machine is also easier to automate than its predecessor. This is partly due to the extended 13-channel clamping hydraulics and optimised standard interfaces to pallet storage systems and robot cells. Efficient chip management is accomplished through a thermo-symmetric design and steep-angled fixed plates, complemented by an internal coolant supply operating at up to 80 bar pressures. This system ensures effective cooling and chip evacuation, with an additional flushing capability of up to 280 litres per minute for applications involving high chip volumes. The Heckert X70 can be integrated with Starrag's comprehensive automation solutions, including Fastems FPT round pallet store systems, different linear storage systems, or robotic cells, catering to various production requirements from small to large batch sizes. The Fastems FPT system provides an economical entry into production automation, enabling workpiece changes for small and medium batch sizes. In contrast, linear storage systems offer maximum flexibility for production processes with integrated master control for effective task planning and distribution. The new Heckert X70 is based on the comparable four-axis Heckert H-series machine envelope. Instead of the NC rotary table installed in the Heckert H-series, the new Heckert X-series models feature a robust rotary/tilt table - an in-house development that is also manufactured at the Starrag plant in Chemnitz. Not only does the tilting unit have two equally sized bearings, but also a thermally stable design. This means that the machines can complete five-sided, highly dynamic machining of complex components. Ensuring the compatibility of the pallets on the new Heckert X70, as well as the Heckert X80 and Heckert X90 models, was particularly important to the developers. The pallets are interchangeable with those from the H series. Furthermore, the pallets from the older Heckert HEC 630 / 800 X5 machines can also be used on the new Heckert X models. The Heckert X70 is now available as part of Starrag's expanded Heckert X-series line of 5-axis machining centres. Manufacturers are invited to see the new machine at EMO Hannover in September. The Heckert X-series also includes the smaller Heckert X50 and the larger Heckert X80 and Heckert X90 variants for manufacturers seeking larger work envelopes and enhanced capacity. |
|
|
|
Charging ahead safely: Confronting the growing risks of electric vehicle lithium-ion batteries | 29/07/2025 |
THE ARE several key risks associated with lithium-ion batteries used in electric vehicles. Mike Brodie, MD of Chemstore UK, shares the latest best practice for their safe storage and management. The rapid shift toward electric vehicles (EVs) across consumer markets, motorsports, and commercial fleets, is transforming the global automotive landscape. At the core of this transition lies lithium-ion (Li-ion) battery technology, offering impressive energy density and performance. But with this innovation comes a serious and growing challenge: safety. Though Li-ion batteries are powerful, they are also inherently volatile. Under certain conditions, including mechanical damage, overcharging, exposure to heat, or improper storage, these batteries can enter a state known as thermal runaway, which can lead to fires, explosions, and toxic gas release. As well as presenting a technical problem for engineers, this risk spans vehicle design, manufacturing, transport, storage, service, and disposal. Whether you’re a manufacturer, motorsport team, logistics operator, or facility manager, it’s essential to understand the risks and be prepared. EV battery risk is a wide-scale issue The risks tied to EV batteries extend far beyond the road or racetrack. Every phase of the electric vehicle lifecycle introduces potential hazards:
Why the risks are increasing High energy density = high potential for harm Li-ion batteries store massive amounts of energy in compact spaces. In the wrong conditions, they can behave unpredictably, and a single failure can trigger a cascade of destruction in minutes. Motorsports: The innovation frontier Motorsport teams push the boundaries of performance. But extreme temperatures, vibrations, and charging/discharging cycles also amplify the likelihood of failure, turning the racetrack into a high-stakes testing ground for EV battery safety. Mass adoption means mass exposure As EVs scale globally, so too do the associated risks. One overlooked safety flaw can affect thousands of vehicles, turning isolated issues into large-scale safety liabilities. Public trust in EVs is hard-won, and easily lost. Real-world incidents prove the point In the United Kingdom, lithium-ion battery fires are escalating at a concerning rate. According to data from QBE Insurance, UK fire services responded to 1,330 lithium-ion battery fires in 2024, marking a 93% increase from 690 incidents in 2022. This surge spans various applications, including electric vehicles (EVs), e-bikes, and e-scooters. The safety expectations are clear, and getting stricter Insurers, regulators, battery manufacturers and safety-conscious organisations now expect robust, proactive protocols. These include:
Getting ahead of the problem Overstating the safety risks of EVs could undermine climate progress but that doesn’t mean we should downplay the risks. We must:
Conclusion: Innovation without safety is irresponsible The shift to electric vehicles is essential, exciting and irreversible. But with new technology comes new responsibility. EV battery safety is foundational, not optional. Those who lead on safety will lead the industry. Chemstore is proud to support world-leading vehicle manufacturers, and infrastructure providers with best-in-class, award-winning lithium-ion battery safety solutions. The leaders are already acting. Are you? Get in touch to find out how Chemstore can help you mitigate risk, reduce liability, and futureproof your operations. For more information, visit www.chemstore.co.uk |
|
|
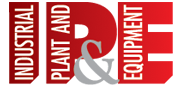