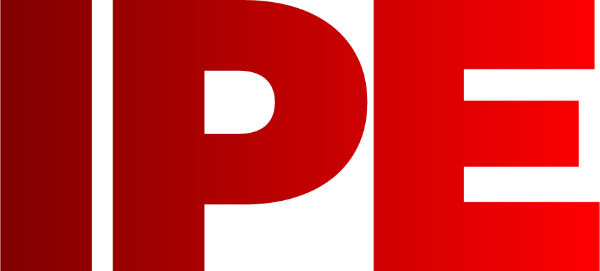
![]() |
Edward Lowton
Editor |
![]() ![]() |
Is lack of visibility damaging your energy performance?
08 October 2019
Industrial businesses with poor visibility of their energy consumption are missing out on the potential for large energy cost and operational savings, says Ian Hopkins, Director of Centrica Business Solutions.
Research by Centrica Business Solutions shows that less than a quarter of businesses continuously monitor their energy use. Most say they measure energy use annually, or even less frequently.
If you don't know precisely how, when and where energy is being used, it is difficult to pinpoint where energy is being wasted. How can you understand the full extent of your energy costs, or where the biggest opportunities for savings lie?
Beyond the meter analytics
The most energy efficient businesses understand the importance of collecting and analysing their energy data. Top performers use advanced software analytics to take their energy insights beyond the meter.
This advanced analytics approach involves attaching wireless sensors to energy-using devices, which are connected to an online analytics platform using Internet of Things (IoT) technology. The collected data can provide real-time, granular visibility of power use and easy-to-digest insights on process and asset performance.
In this way businesses with energy-intensive equipment can understand exactly how their processes and equipment are consuming energy and unlock greater value from these assets.
Boosting operational performance
Anomalies picked up by the energy analytics software can be symptomatic of deep-lying faults in plant equipment or weaknesses in operational performance that are otherwise difficult to detect.
With energy intelligence, plant managers can inform maintenance requirements to reduce downtime and increase productivity. It's sometimes possible to identify potential equipment failures before they happen.
Centrica Business Solutions worked with a global cement manufacturer to measure energy use and pinpoint consumption across different equipment, buildings and plant. With real-time monitoring of energy-intensive machinery, the company identified a fault with a conveyor motor that was causing a bottle neck in the manufacturing process. By fixing this, the company achieved £200,000 in operational and energy savings annually. They also achieved further cost savings by eliminating unnecessary out-of-hours energy use across the site.
Informing energy savings
Advanced energy monitoring can also be used to inform energy efficiency improvements and get more out of existing resources. This is particularly important as companies look towards more sophisticated demand reduction measures, such as investing in onsite generation and storage technology. Accurate energy data is required to build a clear picture of energy priorities and create a convincing case for capital investment.
Combined heat and power (CHP), solar photovoltaic systems and battery storage can often provide a rapid return on investment for manufacturing sites, but decisions about equipment size and specification need to be based on accurate consumption figures.
£43k cost saving
FUJIFILM Speciality Ink Systems has used Centrica Business Solutions' Energy Insights technology to achieve a £43,000 annual cost saving at its Kent facility, which provided a return on investment within just 3 weeks.
Centrica Business Solutions installed 22 self-powered sensors to monitor energy-intensive processes and equipment across the facility, which delivered 24/7 energy information to an online analytics platform.
This monitoring highlighted two major issues. A fault with air compressor units meant that they were running during weekend hours, wasting £17,000 per year when the site wasn’t operational.
A second issue on the ink production line meant that specific chillers continued to run after production stopped. By optimising these chillers, FUJIFILM made an additional saving of £26,000 per year.
Benefits of advanced monitoring
Anything that isn’t measured can’t be improved, which is why energy monitoring should be the first step in any effective energy saving plan.
Advanced energy monitoring provides a number of important benefits for manufacturers. It allows them to unlock more value from energy-intensive assets and processes, can reduce their carbon footprint and informs energy investment.
- No related articles listed