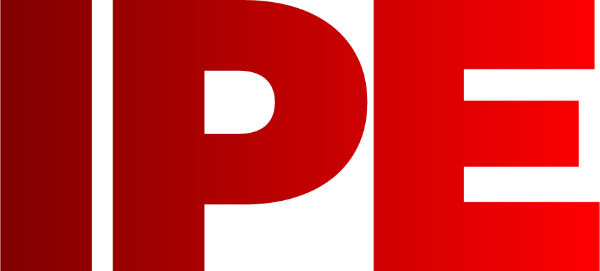
![]() |
Edward Lowton
Editor |
![]() ![]() |
Home> | Handling and Storing | >Warehouse IT | >Revolutionising the MRO Supply Chain |
Revolutionising the MRO Supply Chain
24 September 2024
ERIKS' MRO supply chain report spotlighted that inadequate management of spare parts and inventory is a widespread issue. In a recent webinar, Paul Lynch and Tim Munt looked at several strategies for improving MRO supply chain management

IN THE ever-evolving landscape of manufacturing, the maintenance, repair, and operations (MRO) supply chain plays a pivotal role in ensuring productivity and minimising downtime. This importance was at the heart of a recent webinar hosted by ERIKS. Led by Paul Lynch, business development director, and Tim Munt, chief sales and service officer for ERIKS Industrial Services, the webinar provided an in-depth analysis of the findings from ERIKS’ recently published MRO supply chain report and offered valuable insights and strategies for improvement.
Key insights from the webinar
The webinar commenced with Lynch highlighting a startling statistic from the MRO supply chain report: 51% of manufacturers admitted to suffering downtime due to spare parts availability. This significant figure underscores the critical impact that spare parts availability has on manufacturing operations. Lynch elaborated on the common issues leading to this downtime, such as wrong parts in the engineering stores, expired or broken parts, and simply the absence of necessary parts. These issues cause significant disruptions, leading to lost productivity and increased operational costs.
Lynch noted that many businesses still treat the engineering stores function as a secondary concern, often relegating it to a back-office role with minimal investment and oversight. This can lead to inefficiencies that ripple throughout the entire manufacturing process. The MRO supply chain report, based on a survey with key senior decision makers from within major manufacturers across the UK and Ireland, revealed that inadequate management of spare parts and inventory is a widespread issue that requires urgent attention.
Challenges in inventory management
One of the major challenges discussed during the webinar was the decline in regular inventory checks. In the report, it was highlighted that in 2016 a whopping 12% of respondents never checked their inventory. This figure had alarmingly increased to 30% by 2023. In a 24/7 manufacturing environment, where the engineering stores are often managed only during office hours, this lack of regular checks creates significant opportunities for stock discrepancies. Parts can leave the storeroom without being recorded, leading to situations where the system inaccurately reflects stock levels. When an engineer needs a part that the system shows as available but is not physically present, the result is unplanned downtime and frustration.
The financial implications are substantial, with 20% of respondents reporting that they wrote off more than £25,000 worth of inventory in the last financial year, with an average write-off value of £75,000 per respondent. More than 50% of respondents could not even quantify the value of their inventory write-offs, pointing to a significant gap in financial control and oversight. These write-offs not only represent a direct financial loss but also reflect inefficiencies in the supply chain that could be addressed with better inventory management practices.
From a sustainability perspective, the waste generated by discarding unused parts is equally troubling. For instance, a bearing that is manufactured, transported, and stored for years only to be discarded represents a significant waste of resources. Lynch urged organisations to consider both the financial and environmental costs of poor inventory management and to adopt more sustainable practices.
Issues with 'Squirrel Stores'
Another critical issue highlighted in the webinar was the prevalence of ‘squirrel stores,’ or unofficial stashes of spare parts maintained by individual employees. A surprising 55% of survey respondents admitted to having their own secret stores. While these hidden reserves might provide a temporary solution to avoid downtime, they are a stark warning of a lack of control, confidence and accountability, leading to duplicated orders and increased costs. This phenomenon underscores the need for better inventory management and control mechanisms within manufacturing organisations.
Munt pointed out that these squirrel stores are often seen as a safeguard by employees who have experienced stock-outs in the past. However, this practice leads to inefficiencies and hidden costs. For instance, if an engineer leaves the company, the parts in their personal stash may be forgotten, leading to unnecessary reorders. This lack of visibility and control over inventory can severely impact the financial health of an organisation.
Strategies for improvement
The presenters discussed several strategies for improving MRO supply chain management. They stressed the importance of regular inventory checks to maintain accurate records and ensure the availability of critical parts.
One of the key strategies put forward by Lynch and Munt was outsourcing the engineering stores function. They explained that small teams and limited budgets often lead to inadequate management of engineering stores. By outsourcing this function to a specialised provider, manufacturing organisations can benefit from technical expertise and supply chain knowledge, leading to improved efficiency and cost savings. Outsourcing also addresses the issue of staff turnover, which can be a significant problem for small teams. When a key member of the stores team leaves, it creates a talent gap that can be difficult to fill. Outsourcing ensures continuity and expertise, mitigating the risks associated with staff changes.
The MRO supply chain report supports this approach, noting that businesses with outsourced stores functions often see improved operational efficiencies and cost controls. These providers bring specialised skills and experience that can transform the way inventory is managed, from more accurate stock counts to better procurement practices.
Questions from the audience
The Q&A session at the end of the webinar provided further insights into the concerns of the attendees and the practical steps that can be taken to improve MRO supply chain management. One question addressed the importance of regularly reviewing stores. Lynch responded by emphasising the need for a small number of powerful KPIs that are monitored monthly and digitally to ensure effective management and avoid unexpected consequences.
Another attendee asked about the methodology used to collect the survey data. Munt explained that the survey was sent to a broad industrial manufacturing base, predominantly targeting senior engineering and procurement professionals to obtain a strategic view. The meaningful data set of 200 plus responses provided a comprehensive overview of the current state of MRO supply chains.
The issue of efficiency in procurement was also discussed. Lynch and Munt advised streamlining procurement processes to avoid unnecessary delays and ensure that critical parts are available when needed. They highlighted the importance of balancing on-site and off-site stock to minimise downtime, using the example of the paper industry where lead times and criticality are carefully managed to ensure efficiency.
Questions about write-off procedures and obsolescence management were also addressed. Lynch explained that write-offs typically occur due to either a lack of control or obsolescence, or both. He recommended implementing policies that involve the finance department to ensure that slow-moving inventory is accounted for and managed properly. Obsolescence management involves understanding the shelf life of parts and anticipating changes that may render some parts obsolete.
Lynch elaborated on two types of obsolescence: age-driven and change-driven. Age-driven obsolescence occurs when items reach the end of their shelf life, such as rubber components that become brittle over time. Change-driven obsolescence happens when new equipment replaces old, rendering previously essential spare parts in the stores, obsolete. Lynch emphasised the importance of managing both types of obsolescence to avoid unnecessary write-offs and ensure the availability of critical parts.
The challenges faced by outsourced stores teams in ensuring engineers have the right products were also explored. Communication between the stores team and engineers is crucial to avoid misunderstandings and ensure that critical parts are available when needed. Lynch and Munt emphasised the importance of collaboration and long-term projects to build a comprehensive understanding of the inventory needs.
Achieving efficiency in MRO supply chains
The webinar provided a comprehensive overview of the current challenges and opportunities within the MRO supply chain. The findings of ERIKS’ MRO supply chain report underscore the importance of effective inventory management and control in minimising downtime and improving productivity. By adopting strategies such as regular and digital inventory checks, outsourcing the engineering stores function, and implementing better control mechanisms, manufacturing organisations can enhance their efficiency and sustainability.
The MRO supply chain report and the insights shared during the webinar offer valuable guidance for manufacturing organisations looking to improve their operations. For those interested in delving deeper into the findings and recommendations, the full MRO supply chain report is available for download. For further inquiries or consultancy on improving MRO supply chain management, readers are encouraged to contact ERIKS directly. With the right strategies and expertise, manufacturing organisations can overcome the challenges of the MRO supply chain and unlock new levels of productivity and sustainability.
If you'd like to listen to Paul and Tim discussing the MRO supply chain in further detail, together with what ERIKS can do to help, why not check out our webinar on the subject, available here: tinyurl.com/267ktasx
For more information:
Tel: 0121 508 6000
- ERIKS streamlines customer feedback process
- Going beyond the repairable asset
- Remote status monitoring system
- Automation Services Division launched in UK
- ERIKS provides customer sealing solution for Longwall mining systems
- Top tips to keep your belts in business
- New Eriks report highlights MRO supply chain challenges
- New drive design guide
- Counting down to Maintec 2011
- Metal detectable seal solutions