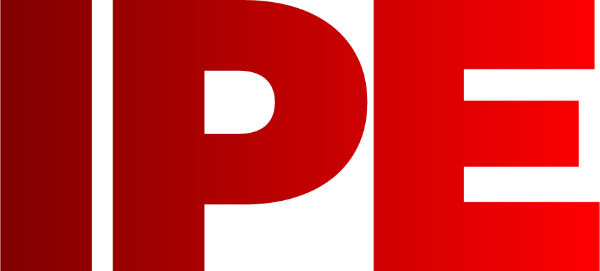
![]() |
Edward Lowton
Editor |
![]() ![]() |
Home> | Plant, Process & Control | >Process equipment | >Supercharging the battery slurry process |
Supercharging the battery slurry process
27 September 2021
INTRODUCED BY ystral, Batt-TDS powder dispersing systems are designed for the development and industrial production of electrode slurries for lithium-ion batteries.

The Batt-TDS™ inducts powders dust-free under vacuum into a stream of liquid, thereby creating conditions for optimal dispersion of diverse components in a continuous sequence. Independent control of key parameters, including flow and shear rates, offers a wide process window in a single piece of equipment.
Dispersion of diverse materials is tailored according to their specific physical properties and topologies with the capability to produce high-solids slurries at high viscosities.
Scalable and cost-efficient
The Batt-TDS is said to achieve high product quality in a fraction of the time required by conventional processes. Easily scalable across various battery chemistries, the Batt-TDS solution is suitable for production at current industrial levels and is ready for tomorrow’s gigafactories. The platform combines a low cost of ownership with high productivity.
ystral has been a leading company for dispersion and dissolution processes for numerous individual components such as PVDF, CMC, carbon black and graphite across multiple industries for more than 20 years. Its solutions can be incorporated to enhance existing processes such as reducing binder or conductive paste preparation time, improving quality, lowering energy costs and minimising equipment footprints.
With the surge in demand for lithium-ion batteries, ystral set out to develop something special for the industry. The ystral development team did not conclude by merely mastering each process in an application development activity, but instead leveraged its extensive experience to build all required functions into a single platform for slurry production.
At R&D scale, the Batt-TDS navi can complete the entire slurry mixing process in just a few minutes, making it suitable for formulation and process screening and enabling faster R&D cycles for more robust product development.
Dispersion itself requires only milliseconds as components pass through its inline process chamber. An intuitive touchscreen HMI automatically captures mixing parameters for seamless scale-up.