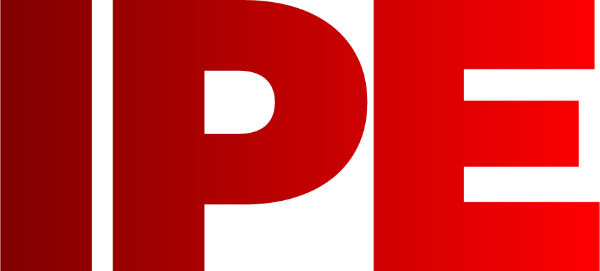
![]() |
Edward Lowton
Editor |
![]() ![]() |
1/6 (1 to 10 of 60)
Recall of safety shoes sold on TikTok exposes substandard PPE crisis | 09/07/2025 |
---|---|
The BSIF has issued a stark warning following the recall of safety shoes sold via TikTok which failed to meet basic protective standards. The case further highlights the growing risk of substandard PPE being sold online THE BRITISH Safety Industry Federation (BSIF) has warned that a recent recall of safety shoes sold via TikTok highlights the alarmingly wide availability of substandard personal protective equipment (PPE) in the UK market. The recalled product, listed on TikTok Shop under multiple descriptors including: "Men’s Anti-smash and Anti-puncture Shoes"; "Breathable Non-slip Work Shoes"; "Comfortable Safety Shoes for Men"; "Fashionable Shoes for Daily Wear, Boy", was advertised as offering protection despite failing to meet essential safety requirements. TikTok Removal Follows OPSS Enforcement Action The recall was issued by the Office for Product Safety and Standards (OPSS) following the intervention of Lewis Collantine, a product safety consultant specialising in trading standards who brought the issue to light. According to the OPSS the product, "presents a serious risk of injuries because although advertised as 'anti-smash' and 'anti-puncture,' there is no evidence it has undergone conformity assessment as PPE and it is not CE or UKCA marked." The OPSS also states: "The product does not meet the requirements of the Regulation (EU) 2016/425 on Personal Protective Equipment or the Personal Protective Equipment (Enforcement) Regulations 2018." While the shoes have now been removed from TikTok following enforcement action by the OPSS, at the time of writing, similar - if not identical - footwear remained for sale on platforms such as Temu. Calls for Tighter Regulation of Online Sellers "No surprises here. The BSIF has been aware of a burgeoning volume of substandard footwear available on platforms such as TikTok for some time, but we are pleased to see Trading Standards take action and we must applaud the work of Lewis Collantine, who has been instrumental in bringing this example to light," said , BSIF CEO Alan Murray. "This is exactly why the new Product Safety and Metrology Bill needs to ensure there are real ramifications for online suppliers who fail to provide properly certified products. Employers and users deserve confidence that PPE described as protective genuinely meets standards and offers the protection it claims." The BSIF warns that many of these products are purchased by unsuspecting individuals who have been given budgets to buy their own PPE but may not fully understand the rules, regulations, and certification requirements surrounding safety products. Alan Murray continued: “We suspect that many of these products are being bought directly by workers - including limb (b) workers who are not direct employees but for whom employers still have a legal duty to provide PPE under recent updates to the PPE Regulations. These individuals are often given a budget to buy their own PPE but may not fully understand the regulations or certification requirements surrounding safety products. The reality is that substandard PPE advertised as protective simply does not protect workers, and it can put lives at risk.” The BSIF reiterates the importance of buying PPE only from BSIF Registered Safety Suppliers, who are committed to supplying certified and compliant products that keep workers safe. For more information: www.registeredsafetysupplierscheme.co.uk Tel: 01442 248744 |
|
|
|
Shocking 90% of PPE from non-registered providers fails tests | 17/06/2025 |
With failures spanning a range of critical categories, the BSIF's findings highlight the urgent need for buyers to verify their PPE sources and prioritise certified, trustworthy suppliers to safeguard workers effectively THE BRITISH Safety Industry Federation (BSIF) has issued an urgent warning to those responsible for procuring personal protective equipment (PPE) and safety products following the results of its latest independent tests. Between December 2023 and December 2024, the BSIF tested 161 products from non-member suppliers, assessing their advertised performance, labelling accuracy, and compliance with relevant standards. Alarmingly, only 10% (16 products) met full compliance requirements, while an overwhelming 90% (138 products) failed to meet the necessary criteria with seven test results still pending. Key problem areas Failures were identified across all product categories, with some showing particularly alarming issues:
BSIF member test results The non-member test results are vastly different from the results of tests conducted on products supplied by BSIF Registered Safety Suppliers. Of the 399 tests completed on products from Registered Safety Suppliers between December 2023 and December 2024, 86% - 322 products - passed. Even for the 14% - 51 products - initially falling short, all issues were promptly addressed and rectified, while 24 results are still pending. Check for the BSIF Shield For buyers and end users seeking assurance, choosing a Registered Safety Supplier helps to ensure not only genuine products fit for purpose but also authentic information and guidance. "By verifying the credentials of their PPE and safety equipment suppliers, buyers can help eliminate the market for substandard goods and prioritise safety above all," said BSIF Registered Safety Supplier Scheme manager Roy Wilders. Resources for buyers
For more information: Tel: 01442 248744 |
|
|
|
Shocking 90% of PPE from non-registered providers fails tests | 28/03/2025 |
An eye-opening 90% of personal protective equipment (PPE) from non-registered suppliers failed safety compliance tests in a recent investigation by the BSIF. With failures spanning a range of critical categories, the findings highlight the urgent need for buyers to verify their PPE sources and prioritise certified, trustworthy suppliers to safeguard workers effectively THE BRITISH Safety Industry Federation (BSIF) has issued an urgent warning to those responsible for procuring personal protective equipment (PPE) and safety products following the results of its latest independent tests. Between December 2023 and December 2024, the BSIF tested 161 products from non-member suppliers, assessing their advertised performance, labelling accuracy, and compliance with relevant standards. Alarmingly, only 10% (16 products) met full compliance requirements, while an overwhelming 90% (138 products) failed to meet the necessary criteria with seven test results still pending. Particularly troubling was the finding that in some categories, including head protection, eye and face protection and fall protection, every non-member product tested (100%) failed the assessments. Even more concerning is the fact that many of these substandard products are still available for purchase. Key problem areas Failures were identified across all product categories, with some showing particularly alarming issues:
BSIF member test results The non-member test results are vastly different from the results of tests conducted on products supplied by BSIF Registered Safety Suppliers, who are committed to selling only certified PPE and trading honestly and ethically. Of the 399 tests completed on products from Registered Safety Suppliers between December 2023 and December 2024, 86% - 322 products - passed. Even for the 14% - 51 products - initially falling short, all issues were promptly addressed and rectified, while 24 results are still pending. Check for the BSIF Shield For buyers and end users seeking assurance, the BSIF Shield is a respected mark of credibility. Choosing a Registered Safety Supplier helps to ensure not only genuine products fit for purpose but also authentic information and guidance. "People are continually surprised by the sheer volume of PPE and safety products that fail to meet basic safety standards. What's even more shocking is that, despite vendors being informed of these deficiencies, such products often remain on the market, continuing to expose unsuspecting buyers and users to significant risks," said BSIF CEO Alan Murray. "Our latest test results have once again brought to light a deluge of problem PPE, from substandard safety helmets to safety shoes that fall a long way short of the required standards for keeping wearers safe. "Buyers and specifiers must urgently review their procurement processes and consider what assurances they have that the PPE and safety equipment they are being supplied with is fit for purpose." BSIF Registered Safety Supplier Scheme manager Roy Wilders said the findings were "deeply concerning". "When protective - and sometimes life-saving - equipment fails to meet standards, it's not just a statistic; it's a potential tragedy waiting to happen," he warned. "The dedicated RSSS team works tirelessly year-round, assessing members of the scheme to ensure compliance with stringent requirements and actively monitoring the market to identify and address substandard products. However, buyers also have a critical role to play. By verifying the credentials of their PPE and safety equipment suppliers, they can help eliminate the market for substandard goods and prioritise safety above all. "Checking for the BSIF Registered Safety Supplier shield is the easiest way to ensure you only deal with compliant, competent and trustworthy suppliers. Remember, anyone can sell safety, but you shouldn't buy safety from just anyone; always check for the BSIF shield," Wilders affirmed. Resources for buyers
For more information: Tel: 01442 248744 |
|
|
|
BSIF urges businesses to review PPE stock for the year ahead | 27/02/2025 |
As 2025 gets underway, the BSIF urges UK workplaces to review and replace outdated or damaged PPE after a recent survey revealed widespread use of substandard equipment THE BRITISH Safety Industry Federation (BSIF) is urging buyers and wearers of PPE to review their PPE stock and replace old and damaged items after a member survey showed outdated and poorly maintained personal protective equipment (PPE) is in use across UK workplaces. Substandard PPE still too common in UK workplaces The survey of BSIF members, made up of manufacturers and distributors of PPE who frequently visit workplaces across the UK, highlighted the prevalence of substandard products in use in Britain’s workplaces. The findings emphasise the urgent need for employers and workers to prioritise PPE evaluation and renewal as they prepare for the year ahead. The survey highlights a worrying trend in the state of PPE and safety equipment across industries. Examples include:
Other insights from the survey:
Ensuring PPE is fit for purpose Commenting on the findings of the survey, BSIF CEO Alan Murray, said: "It’s not enough for PPE to simply meet basic standards - it must be maintained and fit for purpose at all times to ensure worker safety. As one of the survey respondents highlighted the misconception that 'any PPE is good enough' is a dangerous mindset that leads to preventable injuries.” As 2025 gets underway, the BSIF is calling on organisations to make a New Year’s resolution to thoroughly review and refresh their PPE stock. Employers and safety professionals are urged to ensure their equipment is compliant, well-maintained, and fit for purpose. Only source PPE from responsible suppliers such as BSIF Registered Safety Supplier who are committed to selling only certified PPE and safety products that perform to claims made. The BSIF will release its latest findings around non-compliant PPE and safety equipment at the beginning of February 2025. The federation will also be turning up the focus on the essential role of PPE in 2025 with its 'PPE Saves Lives' campaign to launch in the spring. For more information: Tel: 01442 248744 |
|
|
|
BSIF urges businesses to review PPE stock for the year ahead | 02/01/2025 |
The British Safety Industry Federation is calling on UK workplaces to review and replace outdated PPE after a recent survey revealed widespread use of damaged and non-compliant equipment THE BRITISH Safety Industry Federation (BSIF) is urging buyers and wearers of PPE to review their PPE stock and replace old and damaged items after a member survey showed outdated and poorly maintained personal protective equipment (PPE) is in use across UK workplaces. The survey of BSIF members, made up of manufacturers and distributors of PPE who frequently visit workplaces across the UK, highlighted the prevalence of substandard products in use in Britain’s workplaces. The findings emphasise the urgent need for employers and workers to prioritise PPE evaluation and renewal as they prepare for the year ahead. The survey highlights a worrying trend in the state of PPE and safety equipment across industries. Examples include:
Other insights from the survey:
Commenting on the findings of the survey, BSIF CEO Alan Murray, said: "It’s not enough for PPE to simply meet basic standards—it must be maintained and fit for purpose at all times to ensure worker safety. As one of the survey respondents highlighted the misconception that 'any PPE is good enough' is a dangerous mindset that leads to preventable injuries." As 2025 gets underway, the BSIF is calling on organisations to make a New Year’s resolution to thoroughly review and refresh their PPE stock. Employers and safety professionals are urged to ensure their equipment is compliant, well-maintained, and fit for purpose. Only source PPE from responsible suppliers such as BSIF Registered Safety Supplier who are committed to selling only certified PPE and safety products that perform to claims made. The BSIF will release its latest findings around non-compliant PPE and safety equipment at the beginning of February 2025. The federation will also be turning up the focus on the essential role of PPE in 2025 with their ‘PPE Saves Lives’ campaign to launch in the spring. For more information: Tel: 01442 248744 |
|
|
|
The benefits of BSIF membership for professionals | 18/12/2024 |
For the first time, the British Safety Industry Federation is inviting health and safety professionals, duty holders, and compliance managers to join as members in their own right as part of a free membership pilot FOR THE first time BSIF are now asking health and safety professionals/duty holders/category managers/buyers, employers and or employees to become members of BSIF in their own right. To facilitate this, BSIF have launched a free membership pilot. The Pilot seeks to deliver a structure by which BSIF can engage, embrace and support duty holders and safety professionals / compliance managers in all things in PPE/Safety products. There is no cost for Pilot membership, during the Pilot we will forge a form of membership that works for you, the BSIF and the wider safety industry within the UK. The British Safety Industry Federation (BSIF) is the Trade Association for the safety industry and acts as a leading voice for the sector. Set up in 1994 the Federation has some 400 members representing the complete supply chain including manufacturers, importers and distributors of personal protective equipment (PPE) and safety products, through to test houses, certification bodies and specialist safety service providers. The following give a brief overview of the Pilot membership benefits. PPE Helpline The BSIF Members PPE Helpline has been set up to reduce the complexities of PPE & Safety Products and to become the ’Go To’ for information not always easily obtainable in the market place. The BSIF PPE Helpline is administered by PPE & Safety experts ready to assist with any questions relating to a variety of areas including product queries, standards information and help in understanding compliance of different products. The pandemic shone a light on the need for people to be able to access free non commercially biased information. BSIF’s new helpline will cover areas such as:
ACCESS TO BSIF MAILINGS BSIF communicate information that keeps you ahead of the curve. Our mailers arrive into your inbox and cover:
BSIF INDUSTRY CAMPAIGNS BSIF have produced campaigns to raise awareness of H&S issues. They highlight what can happen when personal safety is not taken into account. BSIF want to engage with Pilot members to develop new campaigns and posters to help people avoid hazards that can affect their life now and in the future. BSIF SPECIAL INTEREST GROUPS (SIG’s) BSIF have a structure of PPE/ Safety product SIGs focusing on all relevant issues within the sector. Working directly with Pilot members we will be introducing a new user group to collaborate and support the existing. The user group will receive pertinent information from the SIG’s and feedback valuable opinion and industry experience. BSIF QUALIFICATIONS BSIF Pilot membership gives access to industry courses & qualifications at discounted rates. For example a new publicly recognised qualification for specifiers/buyers of PPE/Safety products. This qualification will help provide the tools needed to procure compliant & safe product. It includes:
BSIF EVENTS BSIF will run Pilot member events designed to inform, educate and network. Giving the opportunity to meet with BSIF Economic Operator members from within the supply chain and other HSEQ members and Duty Holder (Pilot) members. BSi COMMITTEES BSIF are a nominating body for BSI. We can refer our members directly into BSI PH/Horizonal committees. These committees plug into CEN/ CENELEC/ISO working groups. If you want to get more involved in technical standards in PPE you can do so through a BSIF – Bsi referral. If the BSIF Pilot Scheme sounds of interest to you please contact us by email to [email protected] For more information: Tel: 01442 248744 |
|
|
|
Tailored protection: The push for PPE that fits every worker | 28/10/2024 |
Persistent challenges in PPE sizing, representation, and accessibility highlight the ongoing work required to ensure that everyone is adequately protected in the workplace THE ARGUMENT that there’s a requirement for PPE that meets the needs of a diverse workforce is not a hard one to make; people are safer when they have the right PPE that’s correct for their body type, in the specific environment in which they are working. Shifting focus: From functionality to diversity Where historically, innovation in the PPE world has been predominantly focused on functionality, in the last 5-10 years there has been a general shift where brands have acknowledged the need to stock a wider range of products, addressing the needs of more people. Today, there are more products available that take into consideration a person's size, body shape, gender, or religious beliefs. There are even products that address the needs of pregnant women as they move through maternity, brands have realised that pregnant people do need to work and yes, they still need protecting (perhaps more so!). But we’re not there yet. In 2023’s HSM PPE Insights Survey results, many replies cited that sizing was an issue, with "a lack of options for women" across the whole PPE spectrum being a continual issue, with comments such as "Sizing for women - pink it and shrink it doesn’t work". The impact on recruitment and retention With movements such as Bold as Brass and the work of organisations such as the National Association of Women in Construction (and many more) resonating so well recently, the frustrations are clearly there and have been building for the people who wear PPE day-to-day for their whole careers. And it’s not just damaging for those who have suffered over the years, a lack of appropriate safety equipment can only affect recruitment in a negative way, whether that be through people not seeing that they are already represented in these industries or whether they quickly realise that they are not provided for once in the role. Addressing the barriers to effective PPE So, with the ongoing progression of manufacturing brands and with more products coming to market all the time, we must now address why these survey responses persist and address the additional barriers. Firstly, just because these new products exist, it doesn’t mean that they immediately meet the needs of the wearer. As products become less generic, it becomes more difficult for manufacturers to meet their requirements, manufacturers that create poor products with a "diverse message" will soon be found out; those who have been frustrated for decades will not stand for it. Extended research and development time and an understanding that products may not be perfect the first time, coupled with an attitude of continual improvement from wearer feedback is essential. Communication and feedback: keys to progress Feeding information up and down the chain is the key to ensuring the progression of PPE for those currently marginalised. Only by receiving constructive feedback from wearers can the manufacturer know that improvements need to be made, only by having a culture of listening and action, can a manufacturer make these changes a reality. Manufacturers must work tirelessly to make sure their distributors know that these products exist, but also effectively convey their benefits to users as well, alongside engaging with end users where possible. The role of distributors in promoting inclusive PPE Distributors must ensure they are aware of these products and actively make them available to their customers, championing them over the generic and encouraging purchasers that the personal approach to PPE is the best one. Again, this argument isn’t a hard one to make. Someone who is given a product that meets their needs knows that their employer cares, and knows they are valued and respected. This makes it a sustainable approach too. As businesses continue to scrutinise their impact on the environment, they need to not only look at the way in which the products are made but also ensure that wearers are actually getting products that fit them and meet their needs. The proverb ‘respect begets respect’ comes in here; people who are given products that show they are safer, respected, cared for and valued are more likely to respect the products they are given. They are more inclined to care for that product in line with a user information sheet and less likely to request a replacement before it's necessary. This way products will last longer and be replaced less frequently. Overcoming availability and cost barriers Availability is another barrier. Unless manufacturers invest in products that meet the needs of a smaller cohort, they cannot expect that cohort to grow, the onus is on them to push progression and for the rest of the chain to follow suit. Manufacturers and distributors must do everything they can to strive for price equity. Ordering more products in smaller quantities will inevitably cost them more but they must not use niche as an excuse for profiteering. Employers must see the value in tailoring their PPE to their employees or the whole system falls down. Great things are happening, which must be celebrated, but not without a huge dose of humility from all members of the supply chain that they all haven’t yet done enough. So, whilst many barriers still exist to getting the right products worn by the right people for the right environment, many great advances are happening throughout the supply chain. The vital key to ongoing progression is an attitude of feedback that leads to action at all touchpoints within the chain. If we all stay committed, our industries will have happier workers, a more diverse future and we can consign these remaining barriers to the bin. For more information: Tel: 01442 248744 |
|
|
|
Channel 4 expose on substandard PPE "the tip of the iceberg" | 06/09/2024 |
Following a recent Channel 4 documentary which highlighted the dangers posed by PPE with fake safety certificates, the BSIF has once again underlined the importance of sourcing sourcing PPE from verified and competent suppliers A NEW Channel 4 documentary, The Truth about Temu, that revealed that safety products for sale on the Temu app had fake safety certificates and were unfit for purpose is part of a much larger problem of substandard Personal Protective Equipment (PPE) flooding the UK market, according to the British Safety Industry Federation (BSIF). In the Dispatches documentary, reporter Ellie Flynn reveals that some equipment advertised on the platform - which surpassed 46 million downloads in April 2024, making it more popular than Amazon's marketplace app - doesn't perform as advertised and falsely claims to have safety certifications from reputable organisations. Fake certifications One notable instance involved two pairs of pliers, being sold as having electrical insulation properties, that were advertised as being certified by VDE, an established electrical product tester and certifier. However, VDE's Hendrick Schäfer confirmed that these tools had not been certified by the institute. Flynn discovered that the product listings featured altered photos of genuine safety certificates, with the name of the Temu merchant superimposed over the original certificate holder’s name. Schäfer explained that if the certification is not correct: "The insulation of these handheld tools is maybe not properly done and the result could be an electric shock and in the worst case, electric shock could lead to death." The risk of substandard PPE The British Safety Industry Federation (BSIF) has long warned about the widespread availability of substandard PPE and safety equipment offered for sale in the UK and the serious threat this poses to users. The BSIF's own investigations, spanning from December 2022 to December 2023, found that a staggering 79% of PPE items sourced from non-member companies from a range of vendors including online marketplace and high street retailers failed to meet basic safety standards. Examples of these failures are alarming. A flame-retardant parka purchased from an online retailer failed flame spread testing, burning through its outer layer and igniting the inner layer. Additionally, safety glasses from a high street retailer failed impact resistance tests and lacked essential safety documentation. Despite the retailer's assurances that this would be addressed, these glasses remained on sale for over two months after the failure was identified. In response to the certification issues raised by Flynn, Temu told Dispatches: "We do not allow forgeries and will take action against any sellers involved if such cases are found." Using verified suppliers These issues underline the critical importance of sourcing PPE from verified and competent suppliers. The BSIF advocates for the use of their Registered Safety Supplier Scheme, which ensures that products are fit for purpose and meet regulatory standards. This scheme has a compliance rate of 91% during BSIF testing, with any shortcomings swiftly rectified. "Unfortunately, the findings of the Channel 4 investigation are just the tip of the iceberg in terms of the availability of substandard safety products in the UK," said BSIF CEO Alan Murray. "A growing body of evidence shows there is an alarming volume of substandard PPE and safety products for sale and to the untrained eye it can be difficult to tell one from another. We encourage anyone buying safety products to look for the BSIF Shield for reassurance that your supplier is committed to only providing products that are fit for purpose." Find a Registered Safety Supplier at: www.registeredsafetysupplierscheme.co.uk For more information: Tel: 01442 248744 |
|
|
|
Shocking 79% of PPE from non-registered providers fails BSIF tests | 09/05/2024 |
The BSIF has cautioned those responsible for PPE and safety product procurement after recent tests on non-member products revealed a significant number of substandard and dangerous items THE BRITISH Safety Industry Federation (BSIF) has issued a warning to those overseeing personal protective equipment (PPE) and safety product procurement after their latest tests on non-member products highlight the widespread availability of substandard and even dangerous items. Between December 2022 and December 2023, the BSIF examined 123 non-member products, assessing advertised performance, marking adequacy and compliance with standards. Shockingly, only 21% - 26 products - proved fully compliant, leaving a staggering 79% - 97 products - falling short of testing criteria. Worryingly, many of these substandard products are still available and in use, posing serious risks to unsuspecting users. Examples of non-member product failures Some examples of products from non-BSIF-registered members that failed testing include a Flame Retardant Parka, bought from an online retailer. During flame spread testing, the outer layer burnt through, exposing the inner layer, which then caught fire, resulting in the entire coat being consumed by flames. The garment also lacked correct documentation and markings in line with PPE Regulation requirements. A pair of safety boots from the same retailer failed toe cap compressions tests. They were also over ten years old and supplied with outdated certification, didn’t have the correct documentation and were not correctly marked. Elsewhere, a pair of safety spectacles, acquired from a high street retailer failed an impact resistance test, with lenses cracking/breaking when struck by a projectile. The spectacles also lacked markings and the required documentation. Despite promises to remove the product from sale, it was still available over two months later. Meanwhile, a Respiratory Protective Mask (FFP3) purchased from a PPE distributor performed at only half the required level during filter penetration tests against contaminants and had missing documentation. When contacted, the distributor didn't act to remove the product from sale or initiate a recall. BSIF member test results The non-member test result findings sharply contrast the results of tests conducted on products supplied by BSIF Registered Safety Suppliers, who are committed to only selling certified PPE and trading honestly and ethically. Of the 348 tests completed on products from Registered Safety Suppliers between December 2022 and December 2023, 91% - 315 products - passed immediately. Even for the 9% - 33 products - initially falling short, all issues were promptly addressed and rectified. Check for the BSIF Shield For buyers and end users seeking assurance, the BSIF Shield is a respected mark of credibility. Companies displaying this shield have pledged a binding declaration that their offered PPE and safety equipment meets the correct standards, fully complies with regulations, and bears the necessary UKCA and/or CE markings. Choosing a Registered Safety Supplier ensures not only genuine products fit for purpose but also authentic information and guidance. "Our latest test results show that you don't have to look very far to find examples of inadequate and substandard PPE and safety equipment for sale in the UK. Shockingly, many unsuspecting users are relying on these compromised products for their safety," said BSIF CEO Alan Murray. "Checking for the BSIF Registered Safety Supplier shield is the easiest way to ensure you only deal with compliant, competent and trustworthy suppliers. Remember, anyone can sell safety, but you shouldn't buy safety from just anyone; always check for the shield." For more information: www.registeredsafetysupplierscheme.co.uk Tel: 01442 248744 |
|
|
|
BSIF launches PPE checklist to take the risk out of buying PPE | 20/02/2024 |
As part of addressing the rising number of substandard safety products on the market, the BSIF has published a checklist to help specifiers and users ensure that PPE complies with the law and is safe to use WITH AN increasing volume of substandard products on the market, the British Safety Industry Federation (BSIF) has issued a handy checklist to help specifiers and users check whether personal protective equipment (PPE) is fit for purpose. BSIF analysis carried out last year showed that much of the PPE on the market fails to match up to the advertised protection. 85% of non-member products not fully compliant It completed tests on 127 non-member products, which included checking their compliance with relevant standards and testing whether they perform as claimed. Only 18 (15%) of these products were fully compliant. This means 108 products (85%) failed to meet the regulatory criteria, many of which are still for sale to unsuspecting users. The findings around non-member products contrast with the results of tests on products supplied by BSIF Registered Safety Suppliers, whose products are tested annually as part of the scheme’s audit process. Of 387 tests completed on Registered Safety Suppliers’ products, 332 (86%) passed immediately, and of the 55 (14%) that initially did not meet the test criteria, all issues were subsequently resolved. The new BSIF PPE checklist has been created to help specifiers and users ensure that PPE complies with the law and conforms to PPE Regulation 2016/425. It presents a series of questions to ask when purchasing PPE, which are divided into sections for ease of use: Product Markings, Required Documentation, Product Condition, and Storage. Examples of questions included in the checklist are:
If any questions present cause for concern, users are advised to seek support and guidance from their company’s health & safety advisor and the manufacturer of the PPE. The BSIF can also provide general guidance. 'Don't buy safety from just anyone' "This checklist is a reminder that while anyone can sell safety, you shouldn’t buy safety from just anyone," said BSIF CEO Alan Murray. "Failing to check your PPE is fit for purpose could leave you or your employees, for whom you have a duty of care, vulnerable and unprotected, and also expose your organisation to the risk of prosecution. The easiest way to check your PPE is compliant is by only buying from a Registered Safety Supplier." The checklist can be downloaded for free at: tinyurl.com/yrwjsrxt The BSIF also offers an 'Is it Genuine - Certification Checklist' that provides further advice on how to check if the supporting documentation for your PPE is genuine and what to do if you are concerned. It can be downloaded at tinyurl.com/yckvf7zz For more information: Tel: 01442 248744 |
|
|