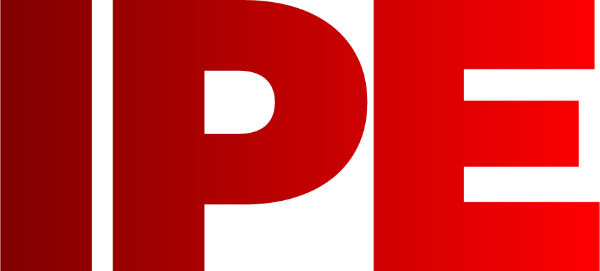
![]() |
Edward Lowton
Editor |
![]() ![]() |
Home> | Health, Safety & Welfare | >Safety Management | >Dual approach to combat HAVS |
ARTICLE
Dual approach to combat HAVS
25 January 2013
Hand-Arm Vibration affects thousands of UK workers each year, causing short-term and long-term medical afflictions. Here,David Wilson, HSEQ manager at HSS Hire, discusses how adequate training combined with a proactive
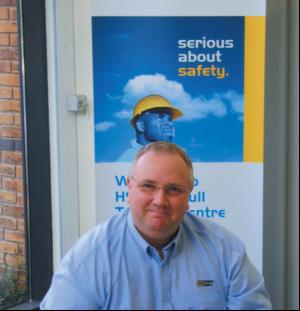
Hand-Arm Vibration affects thousands of UK workers each
year, causing short-term and long-term medical afflictions.
Here,David Wilson, HSEQ manager at HSS Hire, discusses how adequate training combined with a proactive maintenance programme can help to reduce or even prevent such problems in the workplace
Hand-arm vibration occurs when the vibration effects from work processes such as operating hand-held power tools spreads into workers' hands and arms.
The constant exposure to such repetitive vibration has an adverse effect on the body, especially the limbs, and frequent exposure to hand-arm vibration can have detrimental effects on workers health, causing a range of conditions, collectively known as Hand-Arm Vibration Syndrome (HAVS).
HAVS can lead to a number of conditions including carpal tunnel syndrome, or it may manifest itself in loss of strength in the hands, inability to grip, numbness in the fingers, particularly in the tips, and overall reduced grip. HAVS sufferers can also be forced to endure painful joints and permanent damage to bones in the hands and arms. There are up to 5 million workers using hand-held or hand-guided power tools in the UK, with an estimated fifth of them exceeding the HSE's guidelines for HAV exposure and a third of those living with advanced 'white finger' symptoms.
Some industries, particularly those using heavy duty equipment, endure a much greater risk of HAV over exposure than others, with construction, maintenance, manufacturing, engineering, rail, mining, and estate management being among those most affected.
However, it is possible to minimise and reduce the occurrence of HAVS and illnesses relating to vibration through a dual approach of adequate training and the strict maintenance of tools and equipment.
Firstly, operators should ensure that they only carry out work that they're adequately experienced to do, only using equipment that they are trained to use. It is a legal requirement of the employer to ensure employees are up-to-date with the training in order to minimise any potential risks to health including HAVS. That includes knowing how to use the equipment properly so that the task in hand is completed as efficiently and as effectively as possible to reduce the time a worker is exposed to HAV risks. It also means being trained in the theory behind the subject to reduce the overall exposure - knowing how to assess the risk of HAV; how to identify alternative equipment or work processes; how to hold the equipment properly and for the recommended safe amount of time - perhaps using a rotation based work system - as well as how to calculate and adhere to the legal Exposure Action Values (EAV) and Exposure Limit Values (ELV) for each item.
On-the-job training and experience will be invaluable, but it should be supplemented with formal training and industryrecognised accreditation.While educating workers on the correct application of equipment that causes vibration is up to the trainers, their advice soon becomes somewhat redundant if the auxiliary items are left to deteriorate - by auxiliary items I mean the items used in conjunction with the tool itself, drill bits, blades and chisels for example.
Most of the current published data on HAV levels is gained when using tools at optimum condition. Users may be adhering to the published EAVs and ELVs for an item of equipment but what happens when the tools get blunt? Well, quite simply, a tool appendage loses its shop-bought condition after the very first use. Blunt and eroded tools are prone to increasing significantly the amount of vibration absorbed by the user as they produce more friction and impair efficiency as the task takes longer to complete.
So as well as risk assessments and training, it is vital in tackling HAV issues that users start with good tools that are sharp and that they maintain them so they stay that way.
This way, you know that the theoretical EAVs and ELVs that you are working to will be as accurate as possible to the actual working conditions.
If a formal, professional tool maintenance programme isn't possible within your company, invest in a well-respected maintenance channel partner who will resharpen tools to the correct angles. One of the benefits of hiring equipment is that all auxiliary items, as well as the powered item itself, are checked and maintained after each use, so the new user receives 'shop fresh' equipment each time.
When it comes to HAV, it's an issue that's never going to go away but it is an issue that can be managed and controlled and the risk reduced. To do this, the importance of combining both the correct training and the proper maintenance of tools and equipment cannot be stressed enough - this dual approach will not only help ensure the protection of your workforce but should also help achieve optimal productivity.
Here,David Wilson, HSEQ manager at HSS Hire, discusses how adequate training combined with a proactive maintenance programme can help to reduce or even prevent such problems in the workplace
Hand-arm vibration occurs when the vibration effects from work processes such as operating hand-held power tools spreads into workers' hands and arms.
The constant exposure to such repetitive vibration has an adverse effect on the body, especially the limbs, and frequent exposure to hand-arm vibration can have detrimental effects on workers health, causing a range of conditions, collectively known as Hand-Arm Vibration Syndrome (HAVS).
HAVS can lead to a number of conditions including carpal tunnel syndrome, or it may manifest itself in loss of strength in the hands, inability to grip, numbness in the fingers, particularly in the tips, and overall reduced grip. HAVS sufferers can also be forced to endure painful joints and permanent damage to bones in the hands and arms. There are up to 5 million workers using hand-held or hand-guided power tools in the UK, with an estimated fifth of them exceeding the HSE's guidelines for HAV exposure and a third of those living with advanced 'white finger' symptoms.
Some industries, particularly those using heavy duty equipment, endure a much greater risk of HAV over exposure than others, with construction, maintenance, manufacturing, engineering, rail, mining, and estate management being among those most affected.
However, it is possible to minimise and reduce the occurrence of HAVS and illnesses relating to vibration through a dual approach of adequate training and the strict maintenance of tools and equipment.
Firstly, operators should ensure that they only carry out work that they're adequately experienced to do, only using equipment that they are trained to use. It is a legal requirement of the employer to ensure employees are up-to-date with the training in order to minimise any potential risks to health including HAVS. That includes knowing how to use the equipment properly so that the task in hand is completed as efficiently and as effectively as possible to reduce the time a worker is exposed to HAV risks. It also means being trained in the theory behind the subject to reduce the overall exposure - knowing how to assess the risk of HAV; how to identify alternative equipment or work processes; how to hold the equipment properly and for the recommended safe amount of time - perhaps using a rotation based work system - as well as how to calculate and adhere to the legal Exposure Action Values (EAV) and Exposure Limit Values (ELV) for each item.
On-the-job training and experience will be invaluable, but it should be supplemented with formal training and industryrecognised accreditation.While educating workers on the correct application of equipment that causes vibration is up to the trainers, their advice soon becomes somewhat redundant if the auxiliary items are left to deteriorate - by auxiliary items I mean the items used in conjunction with the tool itself, drill bits, blades and chisels for example.
Most of the current published data on HAV levels is gained when using tools at optimum condition. Users may be adhering to the published EAVs and ELVs for an item of equipment but what happens when the tools get blunt? Well, quite simply, a tool appendage loses its shop-bought condition after the very first use. Blunt and eroded tools are prone to increasing significantly the amount of vibration absorbed by the user as they produce more friction and impair efficiency as the task takes longer to complete.
So as well as risk assessments and training, it is vital in tackling HAV issues that users start with good tools that are sharp and that they maintain them so they stay that way.
This way, you know that the theoretical EAVs and ELVs that you are working to will be as accurate as possible to the actual working conditions.
If a formal, professional tool maintenance programme isn't possible within your company, invest in a well-respected maintenance channel partner who will resharpen tools to the correct angles. One of the benefits of hiring equipment is that all auxiliary items, as well as the powered item itself, are checked and maintained after each use, so the new user receives 'shop fresh' equipment each time.
When it comes to HAV, it's an issue that's never going to go away but it is an issue that can be managed and controlled and the risk reduced. To do this, the importance of combining both the correct training and the proper maintenance of tools and equipment cannot be stressed enough - this dual approach will not only help ensure the protection of your workforce but should also help achieve optimal productivity.
MORE FROM THIS COMPANY
OTHER ARTICLES IN THIS SECTION