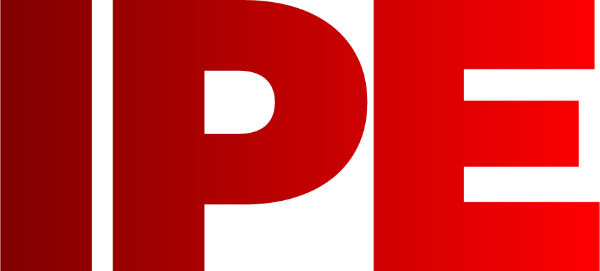
![]() |
Edward Lowton
Editor |
![]() ![]() |
Home> | Plant, Process & Control | >Pneumatic equipment | >Plug-and-play energy recovery |
ARTICLE
Plug-and-play energy recovery
25 January 2013
This time last year, IP&E looked at why energy recovery appeared to be a forgotten technology.A year on, we talk to Anthony Cornes from Atlas Copco Compressors about the latest developments IP&E:What's been happening
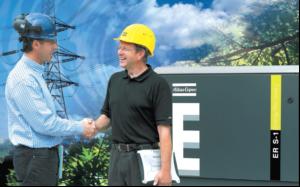
This time last year, IP&E looked at why energy recovery
appeared to be a forgotten technology.A year on, we talk to
Anthony Cornes from Atlas Copco Compressors about the
latest developments
IP&E:What's been happening since we last looked at energy recovery? Cornes: The biggest news is the launch of retrofit kits.When the Carbon Zero breakthrough in compressed air energy efficiency was announced last year, whereby 100% of electrical energy employed in compression can be recovered*, the focus was on larger oil-free compressors up to 750kW with built-in energy recovery systems. Now, the introduction of a range of retrofit energy recovery units for smaller, oillubricated rotary screw compressors means that a broad spectrum of manufacturing and process industries can now also save up to 94% of compression heat costs.
IP&E:What's new about these units? Cornes: Until recently, heat recovery methods applied mainly to larger, watercooled compressors and were achieved via a heat exchanger in the oil circuit that provided hot water at comparatively low temperatures in the region of 50° - 60°C. But now, things have changed with the development of new oil/water heat exchangers that make it possible to retrofit stand-alone units to 11-90kW air-cooled machines, enabling between 72 to 94% of energy recovery to be achieved in the form of hot outlet water at temperatures of up to 90°C.
IP&E: So how has that been achieved? Cornes: By introducing the latest range of stand-alone, plug-and-play energy recovery units. The principal innovation is a completely new stainless steel oil/water heat exchanger that has been designed for simple installation, fast commissioning, reduced downtime and increased safety. All of the mechanical parts are pre-mounted within the unit's canopy, allowing easy access to the thermionic valve and the motor for servicing. The all-in-one-box configuration eliminates the possibility of incorrect connection of flexible hoses and parts.
What's more, no structural beam adaptation of the compressor is necessary to accommodate water inlet and outlet connections.
IP&E:How is recovered heat used? Cornes: Over 45% of industrial applications use hot water in their process operations.
The highest degree of thermal efficiency is generally obtained when the compressor hot water outlet can be connected to a continuous heating demand, such as a heating boiler's return circuit. The temperature level of the recovered energy determines the most appropriate applications.
As a general guide, these can be expressed in percentage terms related to temperature bands: The 51% 'hot' end of water temperatures from 60 - 90°C are ideal for boiler return heating and for heating buildings; the 29% band, 40 - 60°, is suited to hot water tap supply, while the remaining 14%, water at 30 - 40°, can be used for preheating tap water, process water, supply air and maintaining background heating. There may well be other very specific roles within any particular process application.
IP&E: In a multiple installation, does it need a retrofitted energy recovery unit for each compressor? Cornes: Not necessarily, it all depends on the number of installed compressors and their capacities. At present, the largest energy recovery unit is rated at 90kW therefore it could be linked to a single 90kW compressor or 'daisy chained' to a maximum of three 30kW machines or more units of lower capacity. The only limitation is that the total ratings of the linked compressors do not exceed those of the total energy recovery units.
IP&E:What are the cost/benefit ratios? Cornes: If we look at the whole life cost components for an average compressor installation without any form of energy recovery, they can be divided as follows: Capital costs 21%, service and maintenance 7%, operating costs 72%. In comparison, an installation with an energy recovery system in place presents a much healthier picture for an organisation's bottom line: Capital costs 23%, service and maintenance 6%, and operating costs reduced to 31% - so, at least , a significant 40% saving. In terms of return on investment, payback is generally achieved within one year of installation.
Whereas the amount of energy costs is linked to total operating time per year, the degree of use and energy prices, capital investment costs such as these retrofit systems give a direct payback in the form of reduced operational and maintenance costs.
It is also possible to achieve indirect process savings by reducing the maintenance costs of associated equipment and, in specific applications, the overall process efficiency can be boosted by up to 20%.
*In specific design conditions.
IP&E:What's been happening since we last looked at energy recovery? Cornes: The biggest news is the launch of retrofit kits.When the Carbon Zero breakthrough in compressed air energy efficiency was announced last year, whereby 100% of electrical energy employed in compression can be recovered*, the focus was on larger oil-free compressors up to 750kW with built-in energy recovery systems. Now, the introduction of a range of retrofit energy recovery units for smaller, oillubricated rotary screw compressors means that a broad spectrum of manufacturing and process industries can now also save up to 94% of compression heat costs.
IP&E:What's new about these units? Cornes: Until recently, heat recovery methods applied mainly to larger, watercooled compressors and were achieved via a heat exchanger in the oil circuit that provided hot water at comparatively low temperatures in the region of 50° - 60°C. But now, things have changed with the development of new oil/water heat exchangers that make it possible to retrofit stand-alone units to 11-90kW air-cooled machines, enabling between 72 to 94% of energy recovery to be achieved in the form of hot outlet water at temperatures of up to 90°C.
IP&E: So how has that been achieved? Cornes: By introducing the latest range of stand-alone, plug-and-play energy recovery units. The principal innovation is a completely new stainless steel oil/water heat exchanger that has been designed for simple installation, fast commissioning, reduced downtime and increased safety. All of the mechanical parts are pre-mounted within the unit's canopy, allowing easy access to the thermionic valve and the motor for servicing. The all-in-one-box configuration eliminates the possibility of incorrect connection of flexible hoses and parts.
What's more, no structural beam adaptation of the compressor is necessary to accommodate water inlet and outlet connections.
IP&E:How is recovered heat used? Cornes: Over 45% of industrial applications use hot water in their process operations.
The highest degree of thermal efficiency is generally obtained when the compressor hot water outlet can be connected to a continuous heating demand, such as a heating boiler's return circuit. The temperature level of the recovered energy determines the most appropriate applications.
As a general guide, these can be expressed in percentage terms related to temperature bands: The 51% 'hot' end of water temperatures from 60 - 90°C are ideal for boiler return heating and for heating buildings; the 29% band, 40 - 60°, is suited to hot water tap supply, while the remaining 14%, water at 30 - 40°, can be used for preheating tap water, process water, supply air and maintaining background heating. There may well be other very specific roles within any particular process application.
IP&E: In a multiple installation, does it need a retrofitted energy recovery unit for each compressor? Cornes: Not necessarily, it all depends on the number of installed compressors and their capacities. At present, the largest energy recovery unit is rated at 90kW therefore it could be linked to a single 90kW compressor or 'daisy chained' to a maximum of three 30kW machines or more units of lower capacity. The only limitation is that the total ratings of the linked compressors do not exceed those of the total energy recovery units.
IP&E:What are the cost/benefit ratios? Cornes: If we look at the whole life cost components for an average compressor installation without any form of energy recovery, they can be divided as follows: Capital costs 21%, service and maintenance 7%, operating costs 72%. In comparison, an installation with an energy recovery system in place presents a much healthier picture for an organisation's bottom line: Capital costs 23%, service and maintenance 6%, and operating costs reduced to 31% - so, at least , a significant 40% saving. In terms of return on investment, payback is generally achieved within one year of installation.
Whereas the amount of energy costs is linked to total operating time per year, the degree of use and energy prices, capital investment costs such as these retrofit systems give a direct payback in the form of reduced operational and maintenance costs.
It is also possible to achieve indirect process savings by reducing the maintenance costs of associated equipment and, in specific applications, the overall process efficiency can be boosted by up to 20%.
*In specific design conditions.
MORE FROM THIS COMPANY
- Atlas addition
- Further energy savings
- Authorised distributor
- Debunking 10 total cost of ownership myths
- On-the-spot oil contamination testing
- Screw compressors
- Energy efficient compressors
- Atlas copco celebrates 140 years
- Pneumatic nitrogen solution from Atlas Copco delivers 3D printing efficiencies
- Atlas Copco Compressors completes 50th anniversary celebrations in Ireland with a gala reception
OTHER ARTICLES IN THIS SECTION