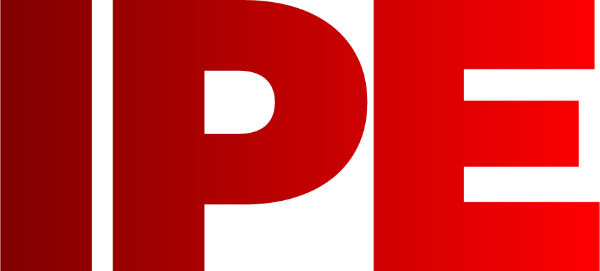
![]() |
Edward Lowton
Editor |
![]() ![]() |
Home> | Energy Management | >Compressors & ancillary equipment | >Saving energy, running time and space |
Home> | Plant, Process & Control | >Compressors and ancillary equipment | >Saving energy, running time and space |
Saving energy, running time and space
20 December 2015
When Calderdale Engineering Services (CES) moved to new premises in Boothtown, it chose to replace its 15-year old fixed-speed compressor with an Atlas Copco VSD installation, supplied by Pennine Pneumatic Services. The new unit has reduced energy costs by 50%, running time by 80% and occupies a smaller workshop footprint.
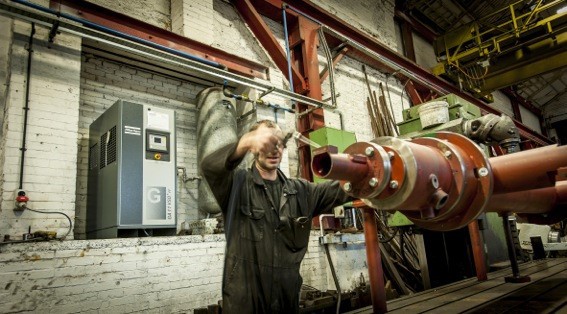
CES offers traditional manual turning, milling, boring and machining capability as well as fabrication and engineering services, from one-off welded assemblies to batch component manufacturing.
The move to new premises prompted a review of the operational efficiency of the compressor installation.
As a long-term customer of Atlas Copco Compressors’ premier distributor, Pennine Pneumatic Services (PPS), CES called on the distributor's expertise to recommend a unit to meet its specific needs. A new Atlas Copco GA11VSD+ rotary screw compressor was installed.
In contrast to the old, continuous running, fixed-speed compressor, the GA compressor’s variable speed drive matches compressed air supply to demand thereby reducing run time and corresponding energy costs by as much as 50%. When combined with the compressor’s in-house designed iPM permanent magnet motor, this is reported to result in an average 37% reduction in lifecycle costs.
- Energy savings calculator
- Controller listed
- Re-design for energy recovery units
- Calculates energy savings
- Air compressors: New generation unveiled
- Joint approach to air issues
- Connected compressors and Industry 4.0
- Competitive compressors
- Further energy savings
- Industrial gas generation: Why the time is right to switch to on-site sourcing