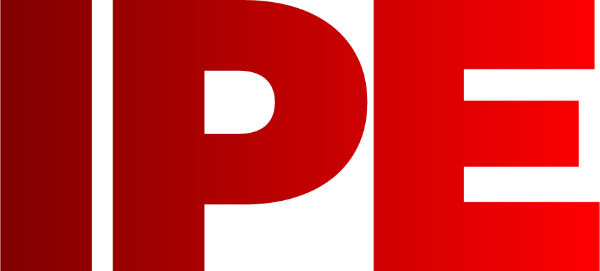
![]() |
Edward Lowton
Editor |
![]() ![]() |
Home> | Plant, Process & Control | >Filtration equipment | >Missing media: Problem solved |
ARTICLE
Missing media: Problem solved
04 March 2013
A recent project for Industrial Purification Systems (IPS) was to evaluate the media filters in a large scale steel works which were inexplicably void of filter media and to instigate a planned schedule of refurbishment works
A recent project for Industrial Purification Systems (IPS) was
to evaluate the media filters in a large scale steel works
which were inexplicably void of filter media and to instigate
a planned schedule of refurbishment works
The project was to refurbish the five existing sand filters. These were located outside and comprised five off steel fabricated vessels each about 3m in diameter. They had 600mm inspection manholes at the uppermost and lowermost levels to enable works to be carried out.
The system was last refurbished eight years ago when the control valves, filter bed nozzles (560/vessel) and sand were replaced. IPS identified that three of the five vessels were void of filter media and two had very little media remaining (about 500mm). A total overhaul of the sand filters was required. The project also included the conversion of the operation of the filters to filter glass.
It was decided that the conversion process would remove all filters from service for work to be undertaken and that work should be completed in 2.5 weeks.
Scope of works During the works it was anticipated that industrial cleaners would be in attendance to remove existing media and clean out the filter vessels prior to inspection Replacement of any damaged plastic nozzles and their close inspection Redesign of the filter bed to incorporate filter glass Approximately one day to remove existing spades in one of the vessels (named vessel 4) One day to fill each vessel with water (for cushioning) and load the filter glass (3 layers) and seal hatches.
Carry out fabrication repairs to vessel 4 where the air discharge pipe had failed and dropped from its location damaging the backwash inlet valve It was believed the existing media was missing due to a number of reasons, one being that the backwash water flow was too high. To address this, the following action was taken: Installation of a line sized valve to control the backwash flow from the backwash pump. The valve was installed in a location to serve all the pumps associated with the backwash flow and was of the type suitable for this application (not butterfly) The valve was installed in a location adjacent to the existing platform next to the backwash discharge pit The line was installed in a straight run of pipe with approximately 1 metre of pipe either side with the valve used being suitable for setting and locking off at a mid-set point.
It was agreed that, due to the filter system having been removed from service and continuous works being viable, work needed to repair vessel 4 would be considered part of the refurbishment program.
Differential pressure switch This function had failed on the existing system and the equipment was replaced by a custom controller manufactured by IPS. Feed lines and isolation valves were also replaced as part of the project.
Refurbishment works On inspection of the empty vessels a number of undamaged nozzles were removed and destroyed to test for aging and brittleness. The nozzles integral strength was discovered to be acceptable however it was found that they were contaminated with a scale-like material and nozzle slots predominately blocked. Later analysis identified the material as Calcium Fluoride. Identification of other nozzles in a similar condition resulted in a decision to remove all 2800 nozzles for manual cleaning.
This meant additional working hours so the project could be delivered on time. In total, 830 new nozzles were procured by IPS to replace damaged/broken nozzles.
The air release pipework in vessel 4 was repaired by firstly removing the backwash in valve, jacking the pipework back into place and fixing, including the manufacture of additional support brackets.
Commissioning The five vessels were individually commissioned with the upper lids off so the backwash and air scour process could be observed. The backwash control valves were set at five complete turns from fully open to achieve the required flow rate.
When the air scour was checked it was found to be too vigorous so blower volume was adjusted on the flow valves located on the blower outlets so a more controlled scour was achieved.
The project was to refurbish the five existing sand filters. These were located outside and comprised five off steel fabricated vessels each about 3m in diameter. They had 600mm inspection manholes at the uppermost and lowermost levels to enable works to be carried out.
The system was last refurbished eight years ago when the control valves, filter bed nozzles (560/vessel) and sand were replaced. IPS identified that three of the five vessels were void of filter media and two had very little media remaining (about 500mm). A total overhaul of the sand filters was required. The project also included the conversion of the operation of the filters to filter glass.
It was decided that the conversion process would remove all filters from service for work to be undertaken and that work should be completed in 2.5 weeks.
Scope of works During the works it was anticipated that industrial cleaners would be in attendance to remove existing media and clean out the filter vessels prior to inspection Replacement of any damaged plastic nozzles and their close inspection Redesign of the filter bed to incorporate filter glass Approximately one day to remove existing spades in one of the vessels (named vessel 4) One day to fill each vessel with water (for cushioning) and load the filter glass (3 layers) and seal hatches.
Carry out fabrication repairs to vessel 4 where the air discharge pipe had failed and dropped from its location damaging the backwash inlet valve It was believed the existing media was missing due to a number of reasons, one being that the backwash water flow was too high. To address this, the following action was taken: Installation of a line sized valve to control the backwash flow from the backwash pump. The valve was installed in a location to serve all the pumps associated with the backwash flow and was of the type suitable for this application (not butterfly) The valve was installed in a location adjacent to the existing platform next to the backwash discharge pit The line was installed in a straight run of pipe with approximately 1 metre of pipe either side with the valve used being suitable for setting and locking off at a mid-set point.
It was agreed that, due to the filter system having been removed from service and continuous works being viable, work needed to repair vessel 4 would be considered part of the refurbishment program.
Differential pressure switch This function had failed on the existing system and the equipment was replaced by a custom controller manufactured by IPS. Feed lines and isolation valves were also replaced as part of the project.
Refurbishment works On inspection of the empty vessels a number of undamaged nozzles were removed and destroyed to test for aging and brittleness. The nozzles integral strength was discovered to be acceptable however it was found that they were contaminated with a scale-like material and nozzle slots predominately blocked. Later analysis identified the material as Calcium Fluoride. Identification of other nozzles in a similar condition resulted in a decision to remove all 2800 nozzles for manual cleaning.
This meant additional working hours so the project could be delivered on time. In total, 830 new nozzles were procured by IPS to replace damaged/broken nozzles.
The air release pipework in vessel 4 was repaired by firstly removing the backwash in valve, jacking the pipework back into place and fixing, including the manufacture of additional support brackets.
Commissioning The five vessels were individually commissioned with the upper lids off so the backwash and air scour process could be observed. The backwash control valves were set at five complete turns from fully open to achieve the required flow rate.
When the air scour was checked it was found to be too vigorous so blower volume was adjusted on the flow valves located on the blower outlets so a more controlled scour was achieved.
MORE FROM THIS COMPANY
OTHER ARTICLES IN THIS SECTION