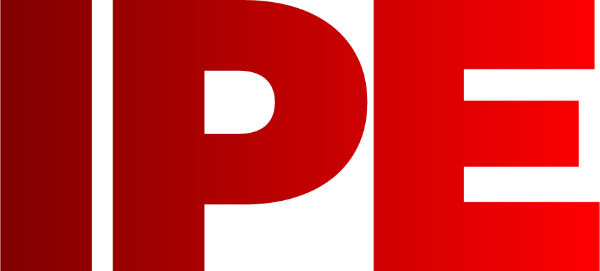
![]() |
Edward Lowton
Editor |
![]() ![]() |
ARTICLE
Management challenge to step into operator’s shoes
27 October 2015
There is a serious problem in the fork lift truck industry that is killing people. The good news however, is that we now know about it and we also know how to fix it. Dave Sparrow, MD of AITT (Association of Industrial Truck Trainers) explains.
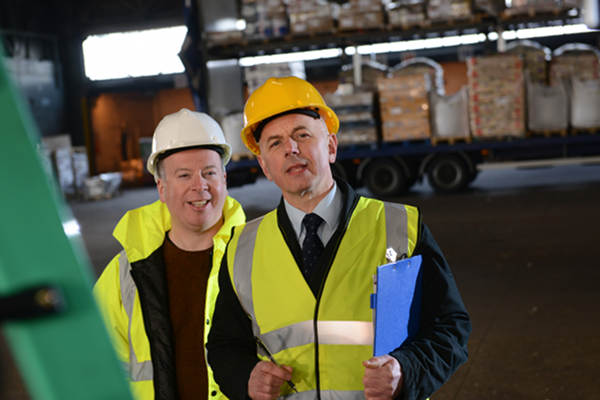
Safety and training experts in the fork lift industry have invested a great deal of time and effort into investigating the root cause of the 800 horrific, life-changing injuries and six tragic deaths that occur every year in the UK because of lift truck accidents. They found that many, if not most, of these accidents are due to operator error that is specifically associated with inadequate training and inadequate supervision.
Historically, there has been a gaping hole in the provision of training for managers and supervisors, especially those who enter the lift truck world with little or no experience of how they function. Indeed, until recently, UK training courses have been focussed on the operator and no training standard existed for managers and supervisors whose role requires them to oversee forklift operations.
Enter AITT’s Standards Committee, which is comprised of a panel of experts who have many years of experience in the industry. Concerned by the lack of training provision for those in these key roles, we designed a comprehensive training standard that manager and supervisor courses must meet in order to be recognised under the AITT accreditation.
Courses meeting this standard will enable those responsible for a company’s forklift operations - who may be lift truck novices themselves - to understand how a lift truck should be operated safely, taking into account different truck types, operating condition, rated capacity and how weight, distance and height have an effect on the truck’s stability.
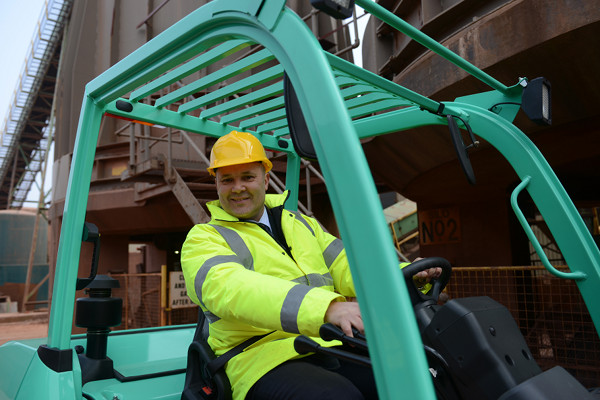
Mentor Training, the UK's largest provider of training in the FLT sector, and one of our accredited training providers, has developed their own course to meet the AITT standard for manager and supervisor training. Feedback from those attending suggests that this type of training fills a previously overlooked skills gap. Stuart Taylor, Managing Director, explains, "More than half of the managers taking our course have never driven a lift truck before and have never received formal training relevant to forklift operations. But following our accredited training course, they leave equipped with the skills and knowledge that empowers them to make good decisions that will reduce accidents. They also learn how to translate working safely into increased productivity and profitability, which is crucial for implementing lasting change.”
Learning to spot bad practice and eradicate it
A good lift truck manager’s course will ensure that candidates are able to identify common bad practices and take the necessary steps to correct them. This is crucial because a silent but widespread obstacle to site safety is the shared acceptance of bad habits – where potentially dangerous practices become the accepted norm. Often it is because it has become a well-established short cut that is disregarded because nothing bad has happened… yet.
Without this training, managers and supervisors who are new to the fork truck industry could inadvertently sanction bad practice and allow it to continue because they are genuinely unaware that is dangerous.
Stepping into the operator’s shoes
By being properly versed in all of these aspects of lift truck operation, managers can begin to understand the kind of time constraints and often overlooked complications that drivers and pedestrians in the warehouse face as part of their daily operations. Armed with all the facts and a degree of empathy, managers are able to work out more accurate estimates of the time it takes to do jobs safely and to ensure that the truck and operator are fit for the job.
In a world where important decisions in the warehouse are influenced by throughput and profit, training should ensure that safety and productivity can go hand in hand. The focus of any business should be safety first, always and without compromise. And importantly, that includes during busy periods, tight deadlines and staff shortages. But businesses looking at training budgets should remember - a safe workforce is a productive workforce. One does not have to come at the expense of another.
The materials handling industry is a round-the-clock, 365 days a year, vibrant network that keeps the rest of the country eating, drinking, building, manufacturing and consuming. An indispensable part of that framework are those who operate lift trucks, and whilst we want our lives to be as easy and cheap as possible – I for one do not want to be responsible for contributing to the possibility of the loss of someone’s life or limb.
MORE FROM THIS COMPANY
- New testing standards for counterbalance and reach truck training
- Verifying forklift operator qualifications
- AITT to address safety conference
- New standards designed to boost warehouse safety
- Growth in fork lift truck training
- Warning: a fork truck operator's certificate is no free pass
- AITT offers guidance for safe training during COVID-19
RELATED ARTICLES
- No related articles listed
OTHER ARTICLES IN THIS SECTION