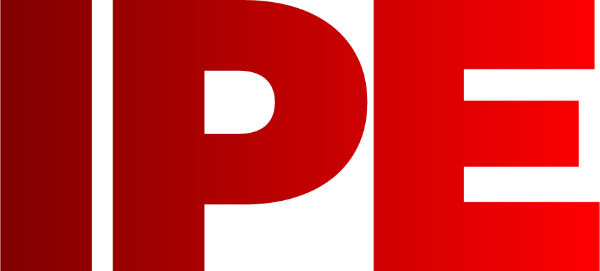
![]() |
Edward Lowton
Editor |
![]() ![]() |
Home> | Industry update | >Company news | >Practical steps to overcome labour shortages in the manufacturing industry |
Practical steps to overcome labour shortages in the manufacturing industry
11 December 2023
The shortfall of skilled workers, coupled with on-going supply chain disruptions has resulted in procurement, safety and supply chain leaders adapting a reactive, rather than a proactive, strategic approach to contractor sourcing and risk management. However, there are a range of reasons why it’s important for manufacturers to adopt a robust approach to contractor management, explain Rebecca Sperti and Graeme Smith

THE MANUFACTURING sector has weathered its fair share of challenges since 2020, and the range of pressure points remains substantial. In addition to the ongoing disruption to global supply chains, UK manufacturers are also having to deal with a shortage of skilled workers, causing a barrier to growth, despite the improvements seen in production and orders.
While not a new problem, the challenge for the industry has been intensified by Brexit, COVID-19, evolving age demographics and growing concerns about workplace safety. 77% of employers reported difficulty in filling roles, with British manufacturers facing the largest shortfall of skilled workers since 1989.
What’s contributing to the labour shortage in manufacturing
In a recent Talent Shortage Survey, the key causes of the labour shortage in manufacturing were categorised as:
36% related to the skills shortage and a lack of qualified candidates - we know that manufacturers and educational institutes need to work together to develop new ways to inspire skill-based learning and courses relevant to the manufacturing industry to equip the future talent stream. There is a need to focus on training and development to retain talent and ensure the supply chain possesses the skills it needs to carry out work effectively.
25% related to Brexit - while the UK is not unique in experiencing shortages of materials and workers, commentators have noted that new immigration rules post-Brexit may have exacerbated the labour shortage situation. The Bank of England reports that slowing population growth is partly responsible for a decreased labour supply, which has been driven by lower net migration from the EU.
20% attributed to manufacturing being an unattractive sector to work in.
19% down to an ageing workforce - it’s estimated that almost 2.7m manufacturing workers will retire by 2030.
What are the impacts of the labour shortage on the manufacturing industry
The manufacturing industry relies heavily on contractors, who are typically spread across multiple sites and locations. A lack of skilled, experienced contractors has created a ‘quick fix’ approach to getting the job completed. However, a ‘corner cutting’ move and lack of long-term partnerships with contractors is leading to increased challenges and risks for the sector, such as:
- Limited visibility of sub-contractors and tiered contractors
- Costly and time intensive internal pre-qualification processes
- Regulatory non-compliance leading to reputational damage
- Increased risk of safety accidents and incidents on site
It's clear that as the recruitment challenge is only set to increase, manufacturers will have to adapt their strategies to find the right people with the necessary skills to fill roles and limit their business risks. An essential part of that means making sure they can access credible, safe, and compliant contractors and have one true view across every tier in their supply chain that spans multi-site and locations
The impact on the compliance and management of supply chain partnerships
The threat of skills shortages is not a new one. For years, a range of industries have struggled to recruit the right talent, and it has only become worse since Brexit, and further compounded by the pandemic.
This challenge has led to:
Business Inefficiencies, e.g. project management and scheduling delays and increased costs due to hiring last-minute contractors.
Regulatory non-compliance, e.g. increased exposure to fines and reputational damage.
Quality and competency issues, e.g. an increased risk of incidents and accidents on site, particularly when working with contractors with the wrong skill set.
It’s time to take action. The need for integrated, proactive management of risk across the supply chain has never been greater.
By its nature, manufacturing is a high-risk industry, both in the output of work and the way it operates. So, for a sector heavily reliant on contractors to keep it moving and operating, ‘plugging the gaps’ does not equal finding the right experience and skills that are safe and compliant to do the job.
Being able to manage contractors across multiple, dispersed sites and locations takes on a whole new dimension when manufacturers have limited visibility not only of their tier one contractors, but the sub-contractors that are subsequently employed.
In today’s outsourced environment, that means there is a greater need to safeguard against risk and gain real time visibility across the whole supply chain. Thinking that it’s enough to only have insight into your main contractors is a significant risk. As highlighted by a recent McKinsey study - 51% of supply chain disruptions occur in Tier-2 suppliers and below, yet only 2% of companies have visibility into their supply base beyond the second tier.
Key questions to consider
- If you were audited today, could you demonstrate that your business and your supply chain is compliant with the latest regulations?
- Do you have one consolidated view of your contractor risk profile data?
- Do your processes and systems produce cost and resource savings?
Key points to consider when reviewing your supply chain partnerships
So now we understand the challenges, let's start looking at some practical steps manufacturers can take to overcome them.
Managing a compliant supply chain and eliminating risks
So, what does managing a compliant supply chain look like? To make sure that your organisation only partners with credible and compliant onsite contractors and offsite suppliers, the foundation for effective supply chain management starts with pre-qualification.
Consistently monitoring contractor risk is a continual process to prevent costly disruptions or weaknesses in the supply chain and ultimately, your business. That means routinely monitoring and auditing topics such as health and safety, financial standing, insurances and ESG.
When using a contractor or supplier for work, can you assure yourself that you have the right controls in place and visibility that compliance standards are being met?
There are several points to consider:
Strategic sourcing - One of the major problems, particularly for clients with multiple locations, is controlling who you bring on to carry out works on your behalf and the lack of central visibility. A lot of enterprise organisations have grown through acquisition so can have siloed 'local' processes. Finding the right onsite contractors and offsite suppliers can be a time-consuming process if you don’t have an approved supplier list. It can take time and resources to shortlist potential contractors/suppliers and you never truly know the quality until you qualify them further through an extended process. As you can see through the impact over the last few years with Covid, Brexit, and the shortage of haulier and HGV drivers, it’s always sensible to have a pool of contractors/suppliers that you can access for business resilience. You can build these up yourself, or you can work with a third party to access accredited suppliers.
Contractor/supplier onboarding - What we tend to see is multiple processes miss-used or bypassed due to them being time consuming or having multiple stakeholders involved, such as Procurement, Safety and Ops who may need to sign off their section before it gets handed over to another department. Like any business, the day to day can get in the way. To minimise this risk businesses should ideally assess safety statistics, regulatory compliance, past performance, and reputation as well as any necessary insurance and training requirements, so you have peace of mind that they’re a good fit for the job. This should prevent scope creep and ensure the contractors are only completing works they are trained and insured to undertake.
Competencies - It’s vital to have an understanding and visibility of the competency of your supply chain to ensure they have the appropriate qualifications, experience, training and knowledge to undertake the task.These competencies would also need to be monitored on-site and reviewed on a regular basis to ensure that any changes in competency are captured, for example, a change in employee numbers and/or a change in scope of works.
Control of work - Control of work can be defined in a number of different ways, depending on the work being undertaken. It’s crucial that any contractors undertaking works on your behalf have regular site inductions, toolbox talks and in the case of high risk works, follow a permit to work system. These methods of communication with your supply chain must be undertaken by a competent person to ensure all processes are being adhered to within the appropriate time frames to minimise risk.
Work completion - Throughout the management of the project and prior to completion of works, it’s important that Project Managers and/or Site Managers undertake regular site monitoring/site inspection activity to ensure the works are being carried out to the sufficient standard and in line with the site documentation specified at the beginning of the project i.e risk assessments and method statements to avoid risk and ensure works are completed in the agreed timescale.
Performance - Part of the performance process would include monitoring during projects via audits and reviews to capture near misses, logging accidents/incidents and reporting under RIDDOR.
Another form of performance monitoring is at the end of the project, where you would review and assess the effectiveness of processes that were implemented during the project to see if there are any areas of improvement to be made.
Having the right audit and review assessments in place will help to clearly demonstrate that you’re following the right legal steps with a robust audit trail of risk management.
Rebecca Sperti is SVP of sales at Alcumus and Graeme Smith is senior business development manager at Alcumus
If you'd like to listen to Rebecca and Graeme discussing how to navigate the impact of labour shortages on supply chain management in more detail, together with what Alcumus SafeContractor can do to help, why not check out their webinar on the subject, available here: https://tinyurl.com/ep4xekur
For more information:
www.safecontractor.com/supply-chain-management
Tel: 0330 828 3032