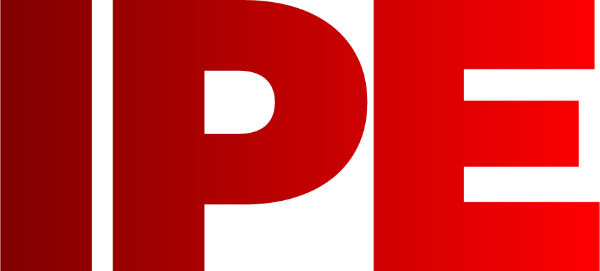
![]() |
Edward Lowton
Editor |
![]() ![]() |
Home> | Production Engineering | >Materials | >Metal rocks 3D printing industry |
Metal rocks 3D printing industry
18 November 2021
ADDITIVE MANUFACTURING equipment maker BCN3D and filament supplier Forward AM are challenging traditional metal injection moulding and CNC milling techniques by printing in stainless steel.
The Metal Pack is an upgrade for users of Barcelona-based BCN3D's Epsilon Series 3D printers which allows them to print with Ultrafuse metal milaments from Forward AM, a brand of BASF 3D Printing Solutions. The pack includes a new hot-end for metal, unique accessories, and filaments of Ultrafuse 316L and 17-4 PH grades. The development allows its customer base to easily upgrade their hardware to catch up with the latest developments and affordably produce solid metal pieces for spare parts, functional prototyping and tooling for the pharmaceutical, food, automotive, aerospace, and manufacturing sectors.
The parts produced by this process have practically identical behaviour to those produced by MIM (metal injection moulding) or CNC and offer an office-friendly solution with far more design freedom. After the printing process, debinding and sintering processes can be carried out externally through the Forward AM's authorised network of service suppliers.
Eric Pallarés, CTO of BCN3D, said: “The whole AM industry is chasing metal 3D printing. But the truth is that, nowadays, affordable available solutions, if any, are very scarce. With the release of the Metal Pack at BCN3D, we are excited to leverage BASF's decades of experience in MIM technology applied to metal extrusion and post-processing. In combination with our existing 3D printing ecosystem, it becomes an end-to-end and accessible solution for functional prototyping. Our customers will be able to take the best advantage of 3D printing by obtaining industry-grade metal parts, within days.”
Firat Hizal, head of metal systems business group at BASF 3D Printing Solutions, said: “The Ultrafuse metal filaments portfolio has been developed based on BASF´s decades of know-how coming from the MIM industry. Filaments are designed for ultimate ease of handling and can be used on any open-source fused filament fabrication (FFF) printer. We are very happy that both Ultrafuse 316L and 17-4 PH are validated by BCN3D and BCN3D decided to enable its user base by introducing this bundle.”
The printing process is divided into three steps: printing a part with the BCN3D Epsilon 3D printers, followed by industry-standard debinding and sintering, which is done externally through the current Forward AM authorised network of suppliers. The result is a final part which is nearly 100% solid stainless steel.
The filaments Ultrafuse 316L and 17-4 PH contain high levels of stainless steel in a polymer binder substrate which allows for easy printing. The substrate is removed from the printed part in a catalytic debinding process. The next step is a sintering process in which the parts reach temperatures just below the melting point of the metal, causing the metal particles to coalesce. The material then reaches its final properties through post-sintering. For example, achieving required performances in aspects such as hardness and strength.
The Metal Pack will include one Ultrafuse 316L (3kg) spool and one Ultrafuse 17-4PH (3kg), the Magigoo 316L which is also compatible with the 17-4PH, two new Hotend M’s and the new BCN3D Brass Wipers for Metal. BCN3D will also publish an add-on for new slicing software BCN3D Stratos dedicated to printing with metal that will include printing profiles curated for the BCN3D Epsilon Series.
The first units of the Metal Pack will be shipped in January 2022.
https://www.bcn3d.com
Ultrafuse is a registered trade mark ®.