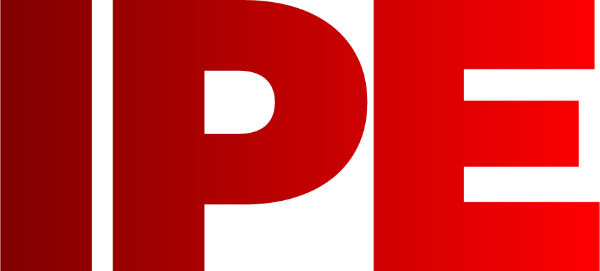
![]() |
Edward Lowton
Editor |
![]() ![]() |
Home> | Handling and Storing | >Lifting equipment | >Bespoke electric winch ensures safe and smooth loading of HGVs |
Bespoke electric winch ensures safe and smooth loading of HGVs
29 March 2024
THE RECENT supply by Hoist and Winch of a bespoke electric-powered winch to a UK building products company is allowing the safe and smooth lifting and lowering of a large telescopic export chute that loads heavy-goods vehicles (HGVs) with a media byproduct from the customer’s production process.

Importantly, raising and descending takes place in a level and precise position thanks to adjustable turn-buckle jacking screws.
Conceived by Hoist and Winch, one of the UK's leading lifting equipment companies, a 400 V three-phase Haacon wire rope winch providing a swl (safe working load) of 1,500 kg sits at the heart of this innovative solution. The advanced winch offers a special triple rope lead-off design that raises and lowers the export chute via one vertically and two horizontally orientated diverter pulleys. A purpose-made frame and bolted connections facilitate mounting of the winch to the steel floor, ensuring level rope pay-off from the winch drum to the three diverter pulleys serving the system.
The final wire rope connection to the export chute is via adjustable turn-buckle jacking screws and swivelling eye bolts, a design that not only provides accurate chute levelling adjustment, but also extends the service life of the wire rope by eliminating any twisting action.
Winch control arrives courtesy of a switchgear enclosure and a two-button, single-speed, hard-wired pendant control station located remotely in an environmentally protected operating cubicle. Environmental protection is vital due to operating temperatures of over 40°C in summer months, as well as excessive dust in the atmosphere and surrounding work areas.
The new winch system, which replaces an original obsolete solution that had reached the end of its service life, offers a number of further beneficial features to the customer, many relating to safety. For instance, the winch has a pressure roller to ensure secure retention of the wire rope on the drum. This capability is particularly important in the event of a slack wire rope, which might occur due to accidental over-lowering of the chute on to the HGV bed, for example.
Further safety-oriented features include an inverter controlled winch motor to provide very smooth and slow speed control, and grooves in the winch drum to ensure even and secure wire rope winding.
Notably, the scope of supply provided by Hoist and Winch was extremely comprehensive, as Andy Allen, director of Hoist and Winch, explains: "We provided all pre-installation survey work to ensure correct alignment of the winch, diverter pulleys and associated equipment. In addition, we performed installation commissioning and load testing, all field wiring and the issue of a LOLER (Lifting Operations and Lifting Equipment Regulations) Thorough Examination Report for the complete system, including diverter pulley support steelwork. We take our responsibilities very seriously in all customer projects, ensuring the delivery of robustly engineered, high-performance solutions that are safe, reliable and fit-for-purpose."
Delivered on-time and on-budget, the installation took place over a two-day plant shutdown. Hoist & Winch also provided thorough operator training on topics such as winch operation and control functions, as well as daily maintenance checks.
Visit www.hoistandwinch.co.uk for further information and to view recent case studies.
- Electric hoist leaves large distillery in high spirits
- Hoist & Winch promotes consultancy know-how
- Construction project presses home the advantage of using Hoist and Winch
- Hoist and Winch performance reaches new heights in roof replacement project
- Hoist and Winch designs bespoke electric winch system for wet room
- Electric winch catapults trebuchet into the spotlight at Warwick Castle
- Hoist and Winch Raise Corporate Profile
- Hoist and Winch helps bridge the lifting expertise gap
- Hoist and Winch is pillar of support in overhead crane project
- Raising the bar for large-capacity hoist installations