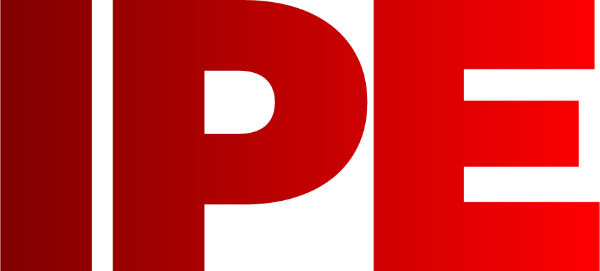
![]() |
Edward Lowton
Editor |
![]() ![]() |
Home> | Handling and Storing | >Safer manual handling | >Rules, tips and best practices for warehouse safety |
Rules, tips and best practices for warehouse safety
09 January 2025
With warehouse accidents on the rise, it's imperative to take proactive measures to protect both your employees and your business

RUNNING A warehouse comes with its own set of challenges, and safety should always be at the top of the list. With the recent rise in warehouse accidents, it’s more important than ever to take proactive steps to protect your team and your bottom line. Ensuring a safe working environment not only helps prevent injuries but also keeps your operations running smoothly and efficiently. Whether you're a seasoned professional or new to the industry, understanding and implementing the right safety measures can make a world of difference.
This article will explore essential rules, tips, and best practices to help you maintain a safe and productive warehouse.
- Understand the Hazards and Controls
The first step towards ensuring warehouse safety is understanding potential hazards to carry out appropriate controls. Warehouses are dynamic environments with numerous risks, including heavy machinery, high shelving, moving vehicles, and manual handling tasks. Identifying these hazards is crucial for creating a safe workspace.
Understanding potential hazards involves a comprehensive assessment of the warehouse environment. It includes evaluating the layout, the type of equipment used, the nature of the goods stored, and the daily operations. Common warehouse hazards include trips, falls, forklift accidents, improper stacking, and hazardous materials handling. Each of these risks requires specific attention and tailored safety measures.
After identifying the hazards, the next step is implementing controls. It can range from physical controls, such as installing guardrails, using proper signage, and ensuring adequate lighting, to procedural controls, such as implementing safety protocols and providing training. For example, training employees on proper lifting techniques can prevent musculoskeletal injuries, while regular equipment maintenance can prevent mechanical failures.
Effective communication and continuous monitoring are also essential. Employees should report potential hazards and near-misses. Furthermore, warehouses should conduct regular safety audits to ensure up-to-date controls.
- Provide PPE
Part of ensuring safety is to provide employees with Personal Protective Equipment (PPE). Warehouses are inherently hazardous, with employees exposed to various risks, including falling objects, chemical exposure, and moving equipment. PPE is an effective line of defence against these hazards, helping to minimise the risk of injury and illness.
For instance, employees may need to wear hard hats to protect against head injuries from falling objects, safety goggles to shield their eyes from debris or chemicals, and high-visibility vests to increase visibility and prevent collisions with moving equipment. In addition, they should wear gloves to protect against cuts, abrasions, and chemical exposure and earplugs or earmuffs to safeguard against noise-induced hearing loss in noisy environments.
Providing appropriate PPE is also a legal requirement by some local governments. As an employer, you are legally responsible for providing a safe working environment, which includes providing employees with PPE.
By providing employees with PPE, warehouse owners mitigate risks by protecting them against potential hazards. Aside from safeguarding the well-being of their workforce, it promotes a culture of safety in the workplace.
- Make Sure Everyone Has Appropriate Training
Warehouse staff should undergo health and safety at work training and be given an appropriate introduction to health and safety at work and safety protocols to ensure their well-being and minimise workplace hazards. This training is crucial as warehouses are dynamic environments with various risks, including heavy machinery, moving vehicles, and hazardous materials.
Health and safety training provides employees with the knowledge and skills to identify potential hazards, assess risks, and implement appropriate control measures. It covers essential topics such as proper lifting techniques, emergency procedures, fire safety, and the safe handling of materials. By understanding these principles, warehouse employees can effectively contribute to maintaining a safe work environment and prevent accidents.
Moreover, providing staff with an appropriate introduction to health and safety at work sets the foundation for a strong safety culture within the organisation. It communicates to employees that their safety is a priority and empowers them to adopt safety practices. This introduction should include an overview of company safety policies, the location of emergency equipment, and procedures for reporting hazards or incidents.
By equipping employees with the necessary knowledge and awareness through training, warehouse businesses can create a safer working environment, reduce the risk of accidents, and protect the well-being of their workforce.
- Carry Out Risk Assessments
Conducting risk assessments is a critical component of ensuring safety in the warehouse. Risk assessment refers to identifying potential hazards within the warehouse environment, evaluating the likelihood and severity of harm they pose, and implementing measures to control or eliminate these risks.
Warehouse employees are prone to hazards, such as heavy machinery, elevated work areas, and manual handling tasks. Therefore, conducting risk assessments is paramount. This process allows businesses to proactively identify potential dangers and take appropriate action to mitigate them.
When conducting a risk assessment, you should focus on key areas like equipment safety, storage practices, material handling procedures, and emergency response protocols. By thoroughly examining each aspect of warehouse operations, businesses can identify potential hazards and assess the effectiveness of existing control measures.
Moreover, warehouses should regularly conduct risk assessments. It's also crucial to assess the warehouse when significant changes occur in the warehouse environment, such as the introduction of new equipment or modifications to processes. Doing so ensures that safety protocols remain up-to-date and reflective of current conditions.
Risk assessments come with many benefits for warehouses. Aside from empowering them to make informed decisions about safety practices, it helps them allocate resources effectively and prioritise areas for improvement.
- Learn About Manual Handling
Manual handling is the lifting, carrying, pushing, or pulling of objects by hand or bodily force. Learning about proper manual handling is essential for ensuring safety in warehouses. According to studies, manual handling accounts for numerous workplace injuries in warehouses. Teaching employees appropriate manual handling techniques protects them against musculoskeletal injuries, strains, and sprains.
By learning about manual handling, warehouse workers will understand ergonomic principles and safe lifting practices. They can assess loads, maintain proper posture, and use mechanical aids effectively to reduce the risk of injury. It also teaches them the importance of pacing themselves, taking breaks, and seeking assistance when handling heavy or awkward loads.
Furthermore, incorporating manual handling training into warehouse safety protocols sends a message to employees that they are concerned about their welfare. It empowers employees to take ownership of their safety and encourages them to embrace measures to prevent injuries. These can reduce absenteeism, improve productivity, and create a safer working environment.
- No related articles listed