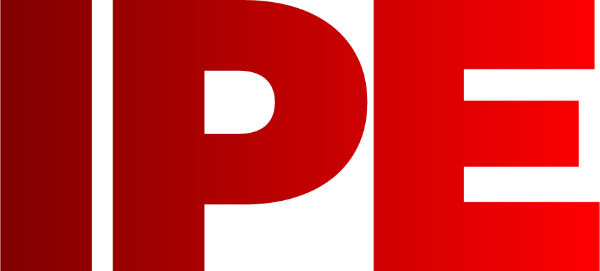
![]() |
Edward Lowton
Editor |
![]() ![]() |
Home> | Handling and Storing | >Safer manual handling | >No room for complacency |
ARTICLE
No room for complacency
25 January 2013
Our workplaces are continuing to get safer - good news for everyone, yet Stanley Handling highlights some facts and figures that suggest that, when it comes to manual handling, there is still more work to be done Data
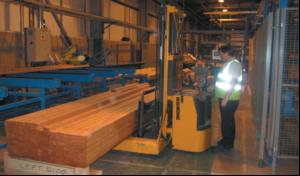
Our workplaces are continuing to get safer - good news for
everyone, yet Stanley Handling highlights some facts and
figures that suggest that, when it comes to manual
handling, there is still more work to be done
Data for the first two quarters of 2009/10 from the HSE (RIDDOR) indicate that non-fatal workplace injuries continue to decline, following a general trend evident since 2004/5, with major injuries down by an impressive 12% compared to the same period last year.
Numbers of 'slips and trips' and 'falls' related injuries have fallen as have 'struck by' incidents, although the latter showed an increase between the first two quarters. 'Handling' injuries fell by 13%. Of all industry sectors, only food, drink and tobacco manufacture saw an increase in reported injuries.
The figures do still make worrying reading for employers, data for 2008/9 revealing that of 29.3 million days lost to workrelated accident or illness, some 4.7 million were due to workplace injury. A total of 180 workers were killed at work, there were 131, 895 other injuries reported (RIDDOR) and 246,000 reportable injuries (Labour Force Survey).
Figures for self-reported work-related ill health indicate that musculoskeletal disorders accounted for the lion's share of complaints with 'stress, depression or anxiety' the next most widespread. This is reflected in data on reported work-related illhealth collected from doctors and specialists.
Interestingly though, mental health gives rise to more working days lost.
The perceptions held by both employers and employees of workplace health and safety again tend to mirror the injury data.
According to the Fit3 Employer survey, musculoskeletal disorders and slipping and tripping were the most commonly reported health and safety risks by British employers.
The Fit3 Worker survey showed that some 76% of a sample of workers involved in manual handling considered it a risk to their health and safety. Significantly, the percentage who felt that their employer was effective in reducing the risk from manual handling was similar at 74%.
Employers have a statutory duty of care to employees and the law is clear as to the responsibilities of both. Besides the safety and well-being of employees, the possibility of prosecution and the penalties available add further to the importance of compliance.
Legislation relating to the use of equipment in the workplace includes PUWER (Provision and Use of Work Equipment Regulations 1998) and LOLER (Lifting Operations and Lifting Equipment Regulations 1998) which between them apply to all equipment and its use at work including that used for lifting, lowering and carrying.
Although employees do not have specific duties under LOLER and PUWER, they do have general duties under the Health and Safety at Work Act and the Management of Health and Safety at Work Regulations 1999, requiring them to take reasonable care of themselves and to co-operate with others who may be affected by their actions.
Employers and employees are subject to the Materials Handling Operations Regulations 1992 (revised in 2004) and these apply to manual handling activities, including lifting, lowering, pushing, pulling or carrying whether or not carried out using 'equipment'.
Note that the equipment regulations apply to anywhere that the HSW Act applies. A risk assessment should contribute to protecting your workers and your business and help you to comply with the law. The HSE suggests a 'five step' approach: Identify hazards Decide who might be harmed and how Evaluate risks and decide on precaution Record and evaluate findings Review and update as necessary Once the assessment has been completed, steps can be taken to avoid hazards in handling, assess unavoidable hazardous operations, remove or reduce the risk of injury and monitor progress. In many organisations risks are well known and managed and workplace manual handling can be reduced and simplified, and any risks further reduced by following easily available guidelines. Simple steps - clearing spillages and keeping floors clear of obstacles for example - are both cheap and effective.
Use of mechanical equipment can cut 'manual' operations and improve safety as well as permitting operations involving heavier and more awkward loads and higher volumes. From hand and heavy duty powered pallet trucks to powered and counterbalanced stackers and a wide range of specialist and bespoke equipment, Stanley Handling offers solutions and advice for all handling applications.
Clear policies to manage health and safety, use of appropriate technology, thorough training and a safe working environment not only raise productivity but can lower costs and provide key building blocks for a company's success.
Data for the first two quarters of 2009/10 from the HSE (RIDDOR) indicate that non-fatal workplace injuries continue to decline, following a general trend evident since 2004/5, with major injuries down by an impressive 12% compared to the same period last year.
Numbers of 'slips and trips' and 'falls' related injuries have fallen as have 'struck by' incidents, although the latter showed an increase between the first two quarters. 'Handling' injuries fell by 13%. Of all industry sectors, only food, drink and tobacco manufacture saw an increase in reported injuries.
The figures do still make worrying reading for employers, data for 2008/9 revealing that of 29.3 million days lost to workrelated accident or illness, some 4.7 million were due to workplace injury. A total of 180 workers were killed at work, there were 131, 895 other injuries reported (RIDDOR) and 246,000 reportable injuries (Labour Force Survey).
Figures for self-reported work-related ill health indicate that musculoskeletal disorders accounted for the lion's share of complaints with 'stress, depression or anxiety' the next most widespread. This is reflected in data on reported work-related illhealth collected from doctors and specialists.
Interestingly though, mental health gives rise to more working days lost.
The perceptions held by both employers and employees of workplace health and safety again tend to mirror the injury data.
According to the Fit3 Employer survey, musculoskeletal disorders and slipping and tripping were the most commonly reported health and safety risks by British employers.
The Fit3 Worker survey showed that some 76% of a sample of workers involved in manual handling considered it a risk to their health and safety. Significantly, the percentage who felt that their employer was effective in reducing the risk from manual handling was similar at 74%.
Employers have a statutory duty of care to employees and the law is clear as to the responsibilities of both. Besides the safety and well-being of employees, the possibility of prosecution and the penalties available add further to the importance of compliance.
Legislation relating to the use of equipment in the workplace includes PUWER (Provision and Use of Work Equipment Regulations 1998) and LOLER (Lifting Operations and Lifting Equipment Regulations 1998) which between them apply to all equipment and its use at work including that used for lifting, lowering and carrying.
Although employees do not have specific duties under LOLER and PUWER, they do have general duties under the Health and Safety at Work Act and the Management of Health and Safety at Work Regulations 1999, requiring them to take reasonable care of themselves and to co-operate with others who may be affected by their actions.
Employers and employees are subject to the Materials Handling Operations Regulations 1992 (revised in 2004) and these apply to manual handling activities, including lifting, lowering, pushing, pulling or carrying whether or not carried out using 'equipment'.
Note that the equipment regulations apply to anywhere that the HSW Act applies. A risk assessment should contribute to protecting your workers and your business and help you to comply with the law. The HSE suggests a 'five step' approach: Identify hazards Decide who might be harmed and how Evaluate risks and decide on precaution Record and evaluate findings Review and update as necessary Once the assessment has been completed, steps can be taken to avoid hazards in handling, assess unavoidable hazardous operations, remove or reduce the risk of injury and monitor progress. In many organisations risks are well known and managed and workplace manual handling can be reduced and simplified, and any risks further reduced by following easily available guidelines. Simple steps - clearing spillages and keeping floors clear of obstacles for example - are both cheap and effective.
Use of mechanical equipment can cut 'manual' operations and improve safety as well as permitting operations involving heavier and more awkward loads and higher volumes. From hand and heavy duty powered pallet trucks to powered and counterbalanced stackers and a wide range of specialist and bespoke equipment, Stanley Handling offers solutions and advice for all handling applications.
Clear policies to manage health and safety, use of appropriate technology, thorough training and a safe working environment not only raise productivity but can lower costs and provide key building blocks for a company's success.
MORE FROM THIS COMPANY
OTHER ARTICLES IN THIS SECTION