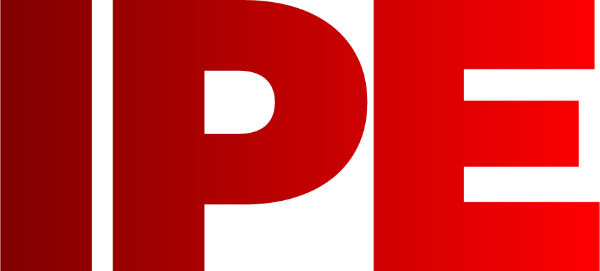
![]() |
Edward Lowton
Editor |
![]() ![]() |
Home> | Energy Management | >Motors and drives | >Electric actuators making deep inroads into MOH applications |
Electric actuators making deep inroads into MOH applications
29 November 2024
Electric linear actuators are transforming mobile off-highway machines with smarter control, better energy efficiency, and reduced maintenance. Offering seamless integration with vehicle systems, they deliver precise, autonomous operation while lowering installation costs and downtime

ELECTRIC LINEAR actuators are steadily gaining ground in mobile off-highway machine design. Where early generation electric actuators could replace single hydraulic or pneumatic cylinders in simple, end-to-end motion applications using up to 100 watts of power, modern actuators can perform complex motion profiles drawing power up to 400 watts.
Designing with smart actuators
Smart actuator applications could be as simple as low-level power switching or as sophisticated as implementing a control deck across a CAN bus network. Having a microprocessor in the actuator enables access to functionality and position data that might otherwise have required external components. Synchronising movement of multiple actuators is done with simple cabling and programming movements and movement profiles independently.
Collecting position data without adding external sensors and other equipment also reduces the number of components and simplifies installation.
Self-driving agriculture equipment is a good example of a smart actuator application. Some grain harvesters, grape harvesters and farm tractors, for example, already operate autonomously. This makes it critical for actuators to control stroke and force on their own. By replacing an operator who might otherwise control operation from visual clues, a system running autonomously must rely on electronic feedback.
To deliver this, most smart actuators have built-in fieldbus capability. Some have CANopen masters that enable direct connect to vehicle controls, eliminating the need for operators or data acquisition equipment. The vehicle's built-in logic manipulates speed, force and position from the master control unit and provides precise control of the actuator and position knowledge for every point of the stroke.
Electric actuators consume energy only when in operation, eliminating the need for a constant power supply. This power-on-demand fuel consumption reduces the operating cost of MOH equipment significantly, in sharp contrast to the parasitic power loss from keeping hydraulic or pneumatic system running constantly.
Lower Installation and Maintenance Costs:
Electric actuators are also much easier to install, requiring only connection to a power supply and signal cables. They are more compact and have fewer components and moving parts than hydraulic systems, which are prone to leaks and require regular maintenance. This reduces downtime and maintenance costs, which is a critical business consideration for heavy machinery operation.
In addition to reducing maintenance requirements, because there is no hydraulic fluid to change or leaks to clean up, electric actuators much safer for food-related applications such as the agricultural harvesters.
And although smart actuators themselves require little maintenance, self-monitoring can reduce overall maintenance costs by sensing wear or helping synchronise replacement schedules with planned machine downtime. They can also share monitoring data in the cloud so that technicians anywhere in the world can dial-in to troubleshoot a particular actuator. And if an actuator does need replacing, it would take only about 20 minutes or so, compared to hours or even days of troubleshooting, disassembly, reassembly, system bleeding and testing, which a fluid driven actuator might require.
For more information:
Tel: +44 1271 334 500
- Thomson Industries introduces electro-hydraulic linear actuators
- Steady automation for car curing
- High load capacity in a small footprint
- Simplifying round rail linear guide system selection
- Compact electromechanical actuators with embedded CAN Bus support
- Simplifying motor integration for linear motion systems
- Thomson to showcase smart electric actuators for intralogistics at LogiMAT 2025
- Cost-effective options to replace hydraulic cylinders