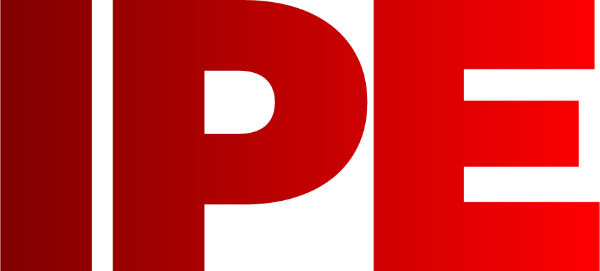
![]() |
Edward Lowton
Editor |
![]() ![]() |
Raising standards in manufacturing & maintenance
12 June 2020
Lifting equipment plays an essential role in manufacturing plants of all sizes. Denis Hogan, Performance and Special Projects Manager at the Lifting Equipment Engineers Association explains why ‘duty holders’, who bear responsibility for the safe design, maintenance and operation of this plant, will find reassurance in the LEEA badge
Manufacturing is a dangerous business. Almost by definition, production involves the transformation of materials through powerful physical processes, using machinery that moves and rotates with speed and force – pitilessly indifferent to anything vulnerable that may be in the vicinity.
Risks in the actual production processes are generally well appreciated. But less attention is sometimes paid to the risks of lifting and moving materials, often at height, with a bewildering variety of cranes, hoists, platforms, cradles and their associated chains, ropes, slings and other tackle. LEEA (The Lifting Equipment Engineers Association) exists to help makers and users of these devices reduce or eliminate these risks.
LEEA works at several levels. We contribute to the development and dissemination of legislation, regulation and ‘best practice’ guidance. Through our auditing schemes, which may lead to membership of the Association, we give assurance that our members’ equipment and procedures are both compliant and safe – which is not always the same thing. And at an individual level we promote training, assess experience and qualify by examination to indicate that people are competent to specify, maintain, inspect and take responsibility for the safe operation of lifting equipment of all kinds.
Our audit schemes are tailored to the circumstances of different types of industry. Craneage in a steelworks, for example, is clearly very different from materials handling in a light fabrication plant. But all carry risks, and the underlying approach is consistent.
That is true globally. The UK and EU operate under the Work Equipment Directive; other countries may have similar rules, weaker regulations, or little law at all. Similarly, product Standards include ISO, EN, and national standards such as BS, ASME and others. Countries without their own standards may often adopt a mix of these, and a variety of rules on the certification of products and on maintenance and inspection regimes. And of course a lot of lifting equipment used in, for example, the UK is manufactured in countries with different domestic regulations.
Assured equipment
What does a LEEA audit look at? Let’s take lifting equipment manufacturers first. Manufacturing begins with raw materials and bought-in parts. We look for evidence that companies are identifying the correct materials for the proposed product and process, that they are buying from reputable sources, that Purchase Orders make clear the requirements including applicable Standards, and that materials are delivered with appropriate certification or declarations of conformity. Are materials properly checked when they are delivered? And is there a stock segregation system to ensure that the wrong material isn’t inadvertently selected – one wire rope, after all, looks very much like another.
Then we need to see that the workforce is properly instructed in the relevant processes, that Quality Control and testing is properly carried out, and that individuals have the relevant competencies to ensure the integrity of the finished goods. Where manufacturers are also installers we would need to look at these processes as well. Competent record-keeping is of course a must.
That should ensure that a company buying lifting equipment from an audited LEEA member is receiving equipment that is safe for the intended purpose. But we also guide and audit end users.
Supporting end users
An important consideration here is whether the buyer properly understands what they are buying, against the intended use. This is becoming more complicated. With the rise of e-commerce, there are more vendors and intermediaries that aren’t necessarily in a position to give reliable advice on the suitability or provenance of the goods they are offering, particularly with lower value items like slings. Also, while older equipment may, when properly maintained, have an almost indefinite life, a lot of new gear has a surprisingly short design life – often as little as ten years. And some slings and accessories are strictly ‘one time only’ – procedures are needed to control this.
Companies need procedures to ensure that those using lifting equipment have been trained and understand how it should be used, and what tasks it is or not safe to use it for. Staff should be trained to spot and report any defects every time they use equipment. Firms also need procedures for routine servicing and for periodic ‘thorough examination’ and inspection. In the UK and many other countries this has to be done by a ‘competent person’, and using someone (in-house or contracted in) with LEEA qualification is an obvious way of satisfying this requirement not just in the UK – many other countries recognise LEEA members as ‘competent’ in this context. Again, the creation and retention of comprehensive records is a key requirement.
Many manufacturing companies may be surprised to discover how much lifting equipment they actually own. Production equipment is fairly obvious, but use of material handling equipment is growing in yards and warehouses, partly in a bid to reduce musculo-skeletal and repetitive strain injuries. Often there is also rarely used equipment to do with building maintenance. And as industrial change sees buildings repurposed, many facilities contain ‘redundant’ lifting gear – redundant, that is, until someone unexpectedly tries to use it. All this needs to be taken into account.
If all this sounds complex, fear not – LEEA is here to help. We are always happy to give guidance, and to encourage firms, whether vendors, installers, or users, into the fold. We are in a sense a one-stop shop. For peace of mind we suggest that firms source and install their lifting gear with LEEA members, use LEEA to train their people, and contract with LEEA members for ‘thorough examinations’. If you are a significant user of lifting equipment, you might wish to consider the LEEA audit, with a view to becoming a member. That would also give your firm a way of making input to the constantly developing technical and regulatory environment around lifting equipment.
- The Lifting Equipment Engineers Association has announced a new leadership team
- LEEA appoints Matt Barber as director of membership
- The world of the Lifting Inspector
- LEEA South East Asia Regional Council holds first meeting
- LEEA launches Chatbot
- Oliver Auston named new LEEA chair
- LEEA appoints Ian Cooke as director of academy
- Visit LiftEx to innovate lifting safety and efficiency
- LiftEx revamped for 2015
- An event-full time for LEEA