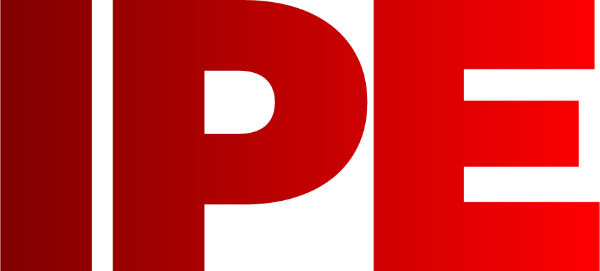
![]() |
Edward Lowton
Editor |
![]() ![]() |
Improving laser sintering (by getting rid of the laser)
07 February 2022
3D Printing has always been a bit of a metaphor, it’s not a process comparable to your desktop inkjet printer. At least not until a British invention hit the market, writes James Snodgrass.

As a country we’ve had more than our fair share of innovations: from the steam engine to the jet engine; and from the telegraph to television (okay, slightly sketchy claim, that one, given the Baird system’s short life and cul-de-sac technology). We’ve also been at the forefront of new materials: polyethylene, the world’s most commonly used plastic, was invented by ICI in the 1930s and, in this century, we have seen the isolation of graphene at the University of Manchester. So it’s great to see a brand-new 3D printing technology that was invented on these shores and, this year, makes the move to production reality.
3D printing as we know it today
The technique is called Selective Absorption Fusion (SAF) and it’s the brainchild of Professor Neil Hopkinson. But before he explains to IP&E how it works, here’s a little reminder of some of the existing 3D printing methods, which basically fall into three categories: resin-based, extrusion-based and powder-based.
The first commercially available form of 3D printing was (and is) stereolithography (SLA), a resin-based method. Solid objects are produced by computer-controlled focussing of laser light within a bath of photoreactive liquid. Where the beam hits the liquid, it completes a chemical reaction, which turns the liquid into solid at that precise point. The three-dimensional form is then built, layer by layer, bottom to top, upside down, with a print platform rising through the vat of liquid.
Then there’s the type of 3D printing that caught the public imagination at the beginning of the last decade, thanks to inexpensive hobbyist machines sold through crowdfunding campaigns, which is commonly known as fused deposition modelling or FDM (an acronym trademarked by Stratasys) and sometimes called fused filament fabrication (FFF). This is an extrusion-based process.
Polymer, often the bioplastic, polylactic acid (PLA), is purchased in the form of a filament wrapped around a spool, like cotton thread around a bobbin. The filament is fed into a heated chamber, making a molten plastic. Tiny strands of the molten plastic are extruded onto a flat surface by moving the extruder head through the x- and y-axes. Once one layer is finished, the print bed moves down (or the extruder head moves up) and the next layer is extruded onto the preceding layer, and so on, until the object is complete. While this technique is fine for hobbyists and prototyping, it is slow. And it creates obvious bands where one layer has fused to the one before, which can require finishing by mechanical or chemical means, to improve appearance.
Sintering and powder-based processes
SAF is powder-based and uses a very familiar technology which could make 3D printing less expensive, quicker and of higher quality than comparable techniques. It’s a technology most of us will have in our home: inkjet printing. Hopkinson was a PhD student at Loughborough University when he filed the patent that underpins SAF, back in 2003.
“At that time, there was a process called laser sintering, which is still around today and a very good technology,” said Hopkinson, “but you are effectively turning powders into parts by melting those powders selectively. It’s a bit like colouring in a drawing, using a Biro. And that struck me as a not very efficient process. So what I asked myself was, how can I make a laser sintering machine quicker, cheaper, so the parts that come from it are cheaper – and therefore suitable for high volume production?
“And the answer was really to remove the laser from the laser sintering machine and replace it with printheads and an infrared lamp, such that the printheads print the shape that would have been drawn by the laser, but they do so far more quickly. And in one pass.”
The printheads aren’t using ink, as in your inkjet printer, but an infrared-absorbing fluid. The printhead passes over a bed of plastic powder and deposits fluid onto the powder just like a conventional inkjet depositing ink on paper. An infrared light follows the printhead. The areas that have been printed with the fluid become irradiated with infrared, getting hot and melting the particles of plastic powder underneath. The areas that haven’t don’t get hot and don’t melt.
This basic idea hasn’t taken 19 years to get from patent to reality. The concept described in Hopkinson’s patent has been licensed to different companies over the years but he wanted to make the process more consistent, to achieve his vision of a system suitable for high volume production. “My background is as a manufacturing engineer,” said Hopkinson, “I was thinking about injection moulding and 3D printing at the same time, trying to pull these things together to get the benefits of both.
“I was talking at the time [1999] about using technologies like laser sintering to make 10,000-plus parts. And, at the time, I think most people in the industry thought I was some sort of barely credible academic with no idea.”
Finding the right print head was critical. Traditional inkjet printheads print up-and-down across the width while the paper feed controls the length from left to right (or top to bottom, depending on orientation). With SAF, the printhead is the entire width of the print bed, therefore travelling in only one axis. This is important for two reasons: so it doesn’t get in the way of the feed of the next powder layer; and to ensure a more consistent temperature, layer after layer, because – regardless of the print area or complexity of each layer compared to the last – “every particle on the surface has the same thermal experience as each other”.
SAF technology is born
Hopkinson’s search led him to Cambridge-based inkjet technology firm Xaar. Hopkinson brought his technology to Xaar and, in 2018, Xaar 3D Ltd. was born: a joint venture between Xaar and US-Israeli 3D printing giant, Stratasys. In April 2021 Stratasys announced its H350 3D printer, the first system using Xaar 3D’s SAF technology. In October 2021, Stratasys bought the 55% of Xaar 3D that it didn’t already own, bringing the technology – and Professor Hopkinson’s expertise – into the Stratasys fold. Early builds of the H350 were placed with technology partners for testing, with the product going on general sale this year.
It helps to visualise the process that the print bed of the H350 is approximately the size of an A4 piece of paper, in landscape format. The print head is on the front of a carriage, the infrared light is on the rear of the same carriage. A second carriage follows the print carriage and deposits the next layer of plastic powder behind it. “Both carriages move left to right,” explained Hopkinson, “then they print, fuse, deposit and pre-heat.”
As with laser sintering, SAF uses engineering thermoplastics including polyamide (nylon), and launches with the sustainable polyamide 11, made from castor seed rather than a petrochemical feedstock. And it can be used to make parts for metal-replacement/lightweighting applications, among many other potential uses.
“It’s very gratifying that, 20 years later, with the technology I’ve invented, that making 10s of 1000s of parts is pretty routine,” said Hopkinson, “and I expect us to go into much higher volumes. So that’s been a very gratifying journey, even if I say so myself.”
FDM and SAF are trademarks of Stratasys
For more information:
www.stratasys.com
Tel: +49 7229 7772 0
- No related articles listed