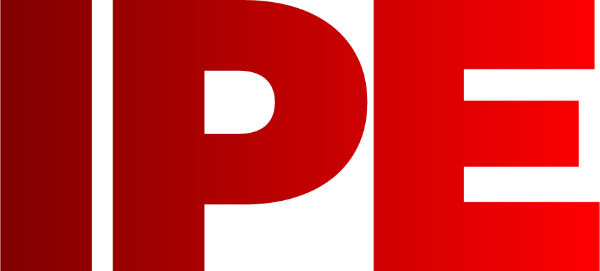
![]() |
Edward Lowton
Editor |
![]() ![]() |
Home> | Handling and Storing | >Safer manual handling | >Three layers of forklift safety |
Three layers of forklift safety
09 January 2025
With workplace injuries costing the €476bn annually, forklift safety requires a multi-faceted approach. From tailored training to advanced telematics and operator assist systems (OAS), companies must combine multiple strategies to improve safety, efficiency, and operator support, says Daniel Heap

FORKLIFT SAFETY requires a comprehensive, multi-faceted approach, including training, real-time support and monitoring, and reactive evaluation after the fact.
According to the European Agency for Safety and Health at Work (EU-OSHA), work-related illnesses and injuries cost €476bn annually. Losing control of machines, tools, or transport and handling equipment is also the leading cause of both non-fatal and fatal workplace accidents, accounting for 25.7% of the latter in the EU. Likewise, industrial sites, including those involving lift trucks, are prone to incidents. Industrial sites account for more than three in ten of all non-fatal workplace accidents.
In addition to the high-stakes challenge of safety, High-intensity operations must get the most production out of a limited labour pool - and it is very limited. According to an extensive study conducted by the United Nations, Europe will have 95 million fewer working age people (between 20 and 64) in 2050 than in 2015.
Inexperienced operators and skeleton crews exacerbate the challenges that businesses face, but forklift safety remains essential in keeping operations moving and hitting targets on-time and on-budget.
TRAINING: BUILD A STRONG FOUNDATION
Health and safety regulation requires a certain standard of lift truck operator training for compliance. This comprises a combination of proven theory training, practical training, and training relevant to the particular workplace. In many cases, health and safety guidelines also require employers to authorise workers to operate a lift truck, which may mean additional levels of training or assessment are required.
No two operations are the same, so it is critical to strategise a training process tailored to equip your operators for the specific needs and challenges associated with your unique facility, workflows, and lift trucks.
TELEMATICS: MONITOR OPERATOR PERFORMANCE IN REAL TIME
Telematics systems can track several aspects of fleets, from equipment diagnostics and utilisation to individual operator performance. All this information can be accessed in real-time via desktops, laptops and mobile devices to make informed fleet management decisions and assist with managing operator behaviour.
Tracking truck information by the specific operator provides visibility to information like travel locations and idle time. Some systems even have impact monitoring functionality that provides managers with notifications when impacts happen, with information about where the incident occurred and who was operating the truck. This data can be used to help identify high performers who deserve recognition and those who may require more training.
Certain systems can also be used to apply equipment performance limitations based on operator experience and skill level. For example, new hires might have their trucks capped at slower speeds to help reduce potential risk, while more experienced operators can have controls set to allow access to higher levels of equipment performance.
OPERATOR ASSIST SYSTEMS (OAS): EQUIP OPERATORS WITH SUPPORT
Telematics is actually part of a broader category of products and technologies designed to assist lift truck operators, known as OAS. This umbrella term encompasses a variety of other solutions, from alarms to pedestrian awareness lighting. While telematics can help facilities monitor and reactively address operator behaviour and truck impact events at their facility, another type of OAS, integrated stability control systems, offer a more proactive approach to help minimise certain tip over risks and automatically reinforce safe operating practices.
One such solution, the optional Dynamic Stability System (DSS) from Hyster, promotes lift truck stability by applying limitations to truck performance in certain conditions, accompanied by audible and visual alerts that communicate the cause of the intervention to the operator. These automatic interventions happen in real time, helping to support stable travel and provide operators with an immediate layer of feedback that can help reinforce the proper lift truck operation established during their training. Picture this:
- An operator retrieves a load stored at height. When they back up and move while lowering the load, the system automatically prevents them from driving too quickly and limits forward tilt to support stability.
- As they travel between point A and B, including around corners, the system limits speed based on how tightly the truck turns, while also working to reduce truck lean.
- The operator is not left in the dark - visual indicators on the truck display and audible alerts supplement the noticeable feedback from performance reductions to let operators know the system is intervening with real-time input.
This innovative technology is made up of four sub-systems lateral stability, high-lift tilt control, high-lift traction control and corner control.
ADVANCED TECHNOLOGY FOR OPERATOR AWARENESS
In addition to stability systems, solutions for operator awareness can also help support human operators in adhering to best practice and site-specific safety processes. Some OAS support operators by adjusting and controlling truck movements, including travel speed, lift speed, or reverse speed.
An example of an advanced OAS is Hyster Reaction. Hyster Reaction proactively adjusts lift truck performance based on real-time conditions, dynamically adapting speed and fork control to maintain the combined stability of the lift truck and load.
Hyster Reaction also continuously monitors the combined centre of gravity of the lift truck and load it carries to apply carefully measured performance adjustments to avoid abrupt shifts or jerks that can upset stability, while keeping the operator in control of the lift truck.
With a combination of specialised sensors and location sensing technologies, Hyster Reaction is designed to assist with stability, collision avoidance, and adherence with location-based rules, such as speed, fork height restrictions, and exclusion zones. However, Hyster Reaction leaves the operator in full control of the truck at all times.
While OAS can be extremely valuable in supporting safety objectives, these solutions are designed for added support, and should not take the place of the correct operator training and supervision.
SAFETY IS NONNEGOTIABLE
As businesses continue to demand more from materials handling operations, safety must remain in focus. Training and trucks are both advancing to help better equip operators to perform in line with best practices.
The key is a layered approach and choosing the training protocols and solutions best suited for the particular application, and its operators.
Daniel Heap is manager, product and commercial technology and connected fleet, EMEA, for Hyster Europe
For more information:
Tel: 01276 538500
- Materials handling challenges and how to address them
- Panoramic vision
- Tough forklift for everyday operations
- Lithium powered heavy hitter
- Lift truck attachments in factory fit programme
- Hyster A Series - now with 5 year warranty
- Celebrating 35 years in Craigavon
- Hyster to give first glimpse of monster electric truck
- Li-ion heavyweights
- Hyster debuts economical pedestrian pallet truck