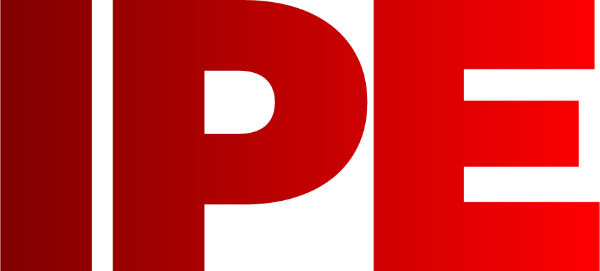
![]() |
Edward Lowton
Editor |
![]() ![]() |
Home> | Handling and Storing | >Warehouse IT | >Do you know what is in your warehouse and where it is now? |
Do you know what is in your warehouse and where it is now?
06 September 2024
When it comes to track and trace, it's important to identify the right solution for your warehouse

EVERYONE WHO runs a warehouse knows that space is expensive, stock is expensive and even more expensive when it gets moved and you lose track of it. The MD’s office might not have a lock but the warehouse door does! Another example that shows how costly, misplaced stock can be, is some distribution warehouses have airport style security to ensure nothing leaves by the wrong exit.
Turck Banner and their sister company, Turck Vilant, have a unique track and trace system that can tell you what is in your warehouse and where it is in real time.
The problem with alphanumeric ordering
The simplest warehouses often use shelf locations in alphanumeric order, with one location for each product. This is very inefficient in terms of the space requirement, as a location is required regardless of whether there is currently any stock or not. Gaps must be left for new products to be accommodated between current locations, or for larger quantities of the current items to fit in the correct location. This system doesn’t require any form of tracking beyond goods in and goods out but is the most prone to errors and misplaced items.
A chaotic warehouse system has numbered locations which get filled based upon quantity and product dimensions, not part numbers. The system keeps track of what product is in which location and directs the warehouse person to either, place items in a location or pick from a location. This solution is a much more efficient use of space, as every location can be used by any product. However it is still reliant on a person using the correct location and not moving anything.
The issue with barcodes
Often these two systems are combined with a barcoding solution, where every product carries a barcode and the warehouse person scans the barcode of each item, when they pick or place the item in a location. This confirms that the correct item is selected, but is still vulnerable to items being moved or removed without the systems instruction. Errors also commonly occur when a warehouse person scans the same item multiple times instead of correctly scanning each similar item. For example, they are instructed to pick 3 of item A, they scan the first barcode three times but have actually picked up two of item A and one of a different item, as many products look similar. Barcodes can only be read at close range, one at a time and in direct line of sight, which limits their use where large quantities are involved.
The benefits of RFID solutions
RFID Tags can be read from a greater distance, do not need line of sight and multiple tags can be read at the same time. This allows a whole pallet of goods to be inventoried without removing any items from their containers. There are standards for the data content of RFID tags defining: products, shipments and assets allowing shipments from multiple suppliers to be received without issue. RFID tags are more robust and reliable than barcodes but generally cost more. Bulk quantities of low value items are often identified with a single RFID tag.
In a busy shipping area, pallets of goods with RFID tags can be passing readers in many directions at the same time. i.e. Goods being loaded or unloaded and goods being transported to and from other storage locations. The inventory system must be able to distinguish between all of these cases and accurately identify the tags that it should be reading and ignore any other tags in the vicinity, including the stray tag that has become stuck to the forklift that is transporting the goods.
As RFID tags need to be within a few meters of the reader to be read and installing enough read heads to cover every location in a warehouse would normally be impractical. RFID warehousing systems are still reliant upon the operator placing the items in the location they were directed to and not moving an item to create space for another item.
What are Real Time Location Systems?
Real Time Location Systems (RTLS) which, in simplistic terms, use beacons in fixed locations within the warehouse or factory that are used to triangulate the position of the receiver, in a similar way to GPS navigation in cars and mobile phones. GPS can be used to track goods in real time and is often the choice for use outside and during transport between factories.
Inside factories and warehouses, RTLS typically uses either UWB (Ultra Wide Band) Radio or BLE (Bluetooth Low Energy) as both are low power, relatively short transmission range 30-200metres, are resistant to interference, and highly accurate, typically 50cm to 90cm.
RTLS would seem like the perfect solution to the warehousing problem. Put a “Tag” on every item and you can find its location, wherever it is, in real time. Unfortunately the RTLS equivalent of a Tag is often more expensive that the item it would be attached to and requires a battery. So typically RTLS is only used to track high value assets, vehicles and people.
Getting expert advice
However if you are an expert in these technologies like Turck Banner's sister company Turck Vilant, you have the skills required to combine these technologies to create an accurate and reliable warehousing solution, that integrates seamlessly with a company’s ERP (Enterprise resource planning) and WMS (Warehouse Management System) to automate the track and trace of goods in real time. The principal is quite simple but the execution requires expertise.
The unique Turck Vilant system tracks the position of the forklift trucks and other transport devices using RTLS, this is combined with the height data from the position of the forks and an RFID reader mounted on the truck to inventory the pallet. This combined data allows the system to know exactly where any pallet has been placed and what is on that pallet. Other systems fail due to unauthorised movement of goods, whereas, any time that a pallet is lifted or moved with the Turck Vilant system, it automatically tracks the new location in real time.
In the medical industry track and trace are a legal requirement, this unique solution provides a complete, real time, stock inventory at the push of a button.
There will always be a balance between single item cost and the cost of methods available to track them. This is why Turck Banner have experts dedicated to track and trace who can not only give advice on the most cost effective solutions but who are constantly pushing the boundaries of technology and innovation to achieve better solutions.
For more information:
Tel: 01268 578888
- Energy efficient and long-lasting
- Daylight visible
- LEDs: Approached from a different angle
- Choosing a precision measurement sensor
- The importance of good connections
- Providing a clear indication
- Sustainability through supply chain management
- Cloud-based remote machine maintenance
- Turck Banner unveils sustainability initiative
- Monitoring, maintenance and IIoT