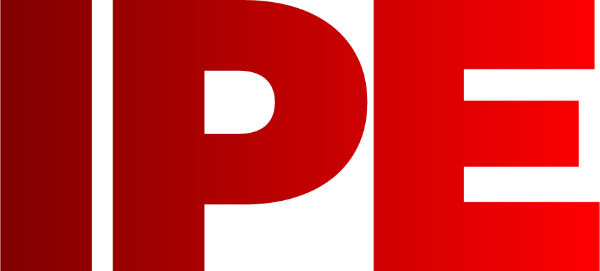
![]() |
Edward Lowton
Editor |
![]() ![]() |
Home> | Production Engineering | >Cutting systems | >Abrasive suspension optimised |
Abrasive suspension optimised
27 July 2020
The Water Abrasive Injection (WAIS) system commonly used in waterjet cutting is increasingly reaching its limits. Addressing this, the Water Abrasive Suspension (WAS) system enables three times higher performance and better quality at significantly lower pressures. To optimise the suspension process, ANT Applied New Technologies AG has developed the abrasive mixing unit ConSus.
Through a globally patented lock method, the mixing unit enables continuous supply of the abrasive and an uninterrupted cutting process. The Fraunhofer Institute of Production Technology (Fraunhofer IPT) has now investigated these unique properties and possibilities.
With the WAIS, water that is under pressure flows through the nozzle in the cutting head of the system. The abrasive is sucked in by negative pressure (“Venturi Principle”) from the abrasive mixing chamber. This results in an air content of about 95 vol. percent as the third phase, which leads to turbulent mixing losses. It reduces the overall efficiency of the cut by about one third. In WAS systems with ConSus, however, part of the pressurized water flows via a bypass valve into the mixing unit, where water and abrasive form a suspension. For acceleration, this is then pressed into the nozzle. The result is a two-phase jet tool consisting of approximately 97.5 vol. percent water and 2.5 vol. percent abrasive. Since the abrasive particles in WAS systems are bound directly in the water, the suspension jet is much more stable, precise and powerful than the injection jet.
Noise level reduction
The Fraunhofer IPT tested both waterjet cutting systems and conducted test series on relevant issues such as health and safety protection at the workplace as well as costs. Measurements based on DIN 9612 have shown that the WAS process with ConSus® has a significantly lower noise level than conventional WAIS cutting jets. Even at a maximum pressure of 1500 bar and 750 g/min of abrasive, the suspension method with ConSus® remains limited to 98 dB, while a WAIS jet with a pressure of 5000 bar and with 500 g/min abrasive produces 108 dB. This corresponds to a noise level factor 3 for WAIS. In real cutting operation and depending on the application, there are even larger differences of 20 to 25 dB.
Minimisation of solid particles
In a further test in accordance with DIN 33896-1, particle emissions during machining of a workpiece were measured. The emissions are mainly a consequence of the grinding of the abrasive. The material used was the particularly tough Inconel® 718. In relative comparison to the WAS process with ConSus®, up to over 200 percent of solid particles were emitted with the injection process (WAS with ConSus®, 1500 bar: 4 mg/cm³; WAIS, 5000 bar: 11 mg/cm³; 400 g garnet sand mesh each 120 per minute).
Protection of abrasive ensures recyclability
According to the Fraunhofer IPT, during the turbulent injection process, the abrasive particles are already significantly reduced in size as they pass through the jet head. Particles that reach a size of less than 100 µm through normal use are generally no longer usable and are disposed of. During the test, this concerned 25 percent of the particles. In the suspension process with ConSus®, in contrast, the size of the abrasive was almost completely retained, ensuring an optimal cutting performance.
Cost-performance ratio
Furthermore, the Fraunhofer IPT compared performance and cost. Alongside the direct consumption costs for the abrasive, energy, employees, wearing parts, maintenance and water, the expenses for initial purchase and depreciation were taken into account. Both systems were supplied with almost the same hydraulic energy (WAIS: 20 kW; WAS: 21kW). Even though WAS systems show higher acquisition and operating costs than WAIS systems, they more than offset those costs through the substantially higher cutting rate of the suspension jet. This results in savings of up to 50 percent in running costs per meter of cut.
In addition to the aspect that the energy consumption with the WAS system is around 70 percent lower, another important factor should be considered: Disposing of the used abrasive is time-consuming and costly. Consumption costs can be significantly reduced with WAS systems by treating the abrasive and the material removal contained in the cutting water. The Abrasive Recycling Unit (ARU) developed by ANT for instance enables inline recycling of up to 80 percent.
Deploying WAS with ConSus offers users decisive advantages over conventional WAIS systems. The two-phase suspension jet ensures reduced noise and particle emissions during waterjet cutting. WAS systems show a considerably higher removal rate, which outweighs the initially higher operation costs (per h) by far. Especially with increased cutting depths and the processing of high-strength materials, there are technological and economic advantages. What is more, the traditional injection process can no longer achieve crucial improvements in performance even at pressures of up to 6000 bar (limit). Thus, at higher pressures the WAIS system increasingly wears out, while the lifespan and reliability of the components are significantly reduced.
ANT AG: Waterjet cutting without air
ANT Applied New Technologies AG is a worldwide technology leader for mobile waterjet cutting and now offers the suspension method stationary for the processing industry. The core competency lies in water abrasive suspension (WAS) cutting technology and in special-purpose machiery. ANT customers across the globe count on reliable service. The systems by ANT AG have a high availability with reliable process accuracy.
The training and experience as well as the personal commitment of ANT AG’s employees guarantee for the high quality and functionality of the systems and for their successful deployment at the customers’ premises. ANT secures the technological know-how through various worldwide patents. ANT AG does not only sell products, but also individual solutions. For more sustainability, the specialist for Water Abrasive Suspension (WAS) and special-purpose mechanical engineering offers solutions to the customers that concern the topics abrasive recycling and water treatment.
- No related articles listed