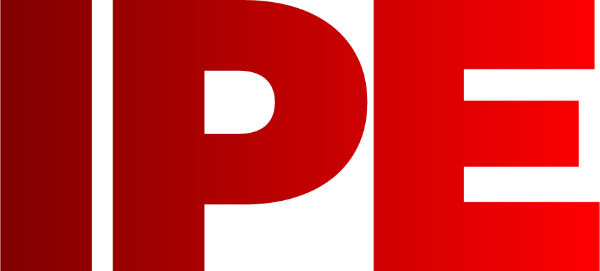
![]() |
Edward Lowton
Editor |
![]() ![]() |
Home> | Health, Safety & Welfare | >Safety Management | >The automation paradox - when robots and humans collide |
The automation paradox - when robots and humans collide
24 January 2025
As warehouses become more automated, with robots and humans working side by side, the risk of human-robot collisions is on the rise. Given this, there is a critical need for comprehensive safety strategies, says James Smith

IN TODAY'S warehouses, team members in high-vis jackets weave between towering racking with robots and heavy machinery operating alongside them, often in close proximity. It is an impressive sight that reflects the technological advances in manufacturing, although I cannot help but wonder: Are we working as safely as we could?
I have spent almost 25 years in manufacturing, and I have never seen change happen so fast. We are racing towards a future where humans and robots will work side by side, but many companies are dangerously underprepared for the safety challenges this brings. With over 4 million robots set to be installed in more than 50,000 warehouses by 2025, a new risk is emerging - human-robot collisions.
Managing the safety of shared human-robot workspaces
Reports have emerged indicating that serious injuries are up to 50% higher in warehouses with robots compared to those without.
The problem comes down to the basic differences between people and machines. Robots operate with programmed precision, following set paths. Humans are adaptable but unpredictable. When these two share space, accidents become more likely. Therefore, we need to put measures in place that influence behaviour, not just rely on safety procedures on paper.
The importance of going beyond basic protection
I have witnessed the pressure to meet ever-increasing productivity targets lead to shortcuts in safety protocols, which makes it more important than ever to design a safety strategy that takes into account the coexistence between people and robots.
This strategy must include comprehensive risk assessments, ongoing training programmes, and the future ability to invest in safety solutions like smart barriers and racking monitors that go far beyond protection. These solutions do much more than just protect people and assets from accidents and bumps - instead, their technology enables preventative maintenance, creates a more efficient warehouse layout through behavioural patterns, and can anticipate future issues thanks to digital twinning, among other benefits. This is a result of having the latest Industrial Internet of Things (IIoT) and data-based technologies integrated into your safety solutions.
Anticipating the needs for a more efficient tomorrow
If you are going to be deploying one of those four million robots, make sure to reassess your safety strategy first. Conduct a comprehensive safety audit of your warehouse as soon as possible, identify every point of human-robot interaction and assess the risks. Then, contact safety experts who understand the unique challenges of automated environments and how to overcome them. Remember, every day you delay this is a day your team is at unnecessary risk.
James Smith is co-CEO at A-SAFE
For more information:
Tel: 01422 331133