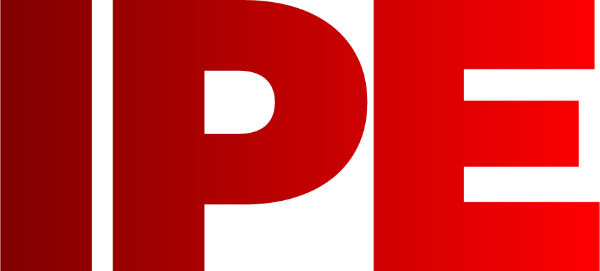
![]() |
Edward Lowton
Editor |
![]() ![]() |
Home> | Production Engineering | >Cutting systems | >‘Clearcut’ Winner For Tackling ACM Delamination Challenges |
‘Clearcut’ Winner For Tackling ACM Delamination Challenges
08 July 2025
AS THE UK's leading manufacturer of precision cutting tools, Industrial Tooling Corporation (ITC) has launched its new Clearcut range of single flute balanced routing tools, specifically engineered to eliminate delamination issues when machining Aluminium Composite Material (ACM) panels.

ACM panels have become increasingly popular in signage, architectural cladding, and display applications. To meet the growing demand for faster turnaround times, more manufacturers are now printing directly onto ACM panels before cutting. This workflow significantly reduces lead times but introduces new machining challenges - ITC has once again listened to the industry and developed a solution with its Clearcut range of cutting tools.
This direct-to-substrate printing approach intensifies delamination and chipping issues during the cutting process, as printed surface layers become more susceptible to heat damage. Cutting stresses can cause both the print and underlying composite structure to fail. "The trend towards printing directly onto ACM substrate before cutting has created a perfect storm for delamination issues," said Sally Hunt at ITC. "Manufacturers gain significant time savings in production, but they've discovered that conventional cutting tools simply cannot handle the increased complexity of machining pre-printed panels without causing costly damage."
The challenge is compounded by the fact that printed ACM panels frequently feature full-bleed graphics extending to the panel edges. Any delamination or chipping during cutting compromises structural integrity and ruins high-quality graphics, resulting in complete part rejection and costly reprints. Traditional cutting tools often leave jagged edges with visible print layer damage, forcing manufacturers to choose between speed and quality. With the slow helix Clearcut Series of routing tools from ITC, manufacturers can maintain both speed and quality.
The signmaking industry has wrestled with this increasing challenge, and the conversations at the Sign UK show have highlighted this challenge. As the industry benchmark, ITC recognised the necessity for a cutting tool solution specifically engineered for the print-then-cut workflow. ITC’s reputation as both a problem-solver and a company that understands the challenges of the industry ensured it developed a breakthrough solution well ahead of its competitors.
"We don't just manufacture cutting tools - we solve manufacturing problems," emphasised Hunt. "When manufacturers came to us with delamination failures on their expensive printed panels, we knew we had to engineer a solution that would prevent the print or laminated surface from lifting whilst maintaining productivity gains and quality standards for customers."
ITC's solid carbide Clearcut range is VITREO coated, and the slow helix geometry ensures maximum productivity with unparalleled edge finishes. The single flute routing tools are available in both coated and uncoated variants, with unbalanced or high-performance balanced tools offered. The balanced tools have been specifically designed for modern digital cutting tables that incorporate high-frequency spindles operating at speeds exceeding 30,000 rpm. The single flute balanced design on a 6mm shank provides construction that eliminates vibration at high speeds, preventing print damage and substrate delamination. The VITREO coating offers superior wear resistance while preventing material and ink adhesion. Simultaneously, the single flute design optimises chip evacuation, reducing heat build-up that damages both graphics and substrate.
"We needed to create a tool that could cut cleanly through multiple material layers at high speed without generating the heat and vibration that destroys expensive printed graphics. The Clearcut's high-speed capability enables clean cuts through printed surfaces without tearing or chipping, whilst the stub length configuration maximises rigidity for precise edge quality on valuable pre-printed panels," Hunt added.
Users consistently report complete elimination of print layer chipping and substrate delamination, with clean, professional edges preserving full-bleed graphics to the edge. "What we're seeing from customers is remarkable," stated Hunt. "They're telling us they can run their machines confidently, knowing that every panel will have perfect edges. At the recent Sign UK show, the number of visitors looking for a solution was evident – once again, we have led the market in developing a solution."
- Ferocious 5-flute milling with new VariMill
- 2023 product catalogue available from ITC
- New line has a ball with steel
- Tightening fixture for collet chucks with an integrated torque indicator
- Cleaning up with a new 'chip fan'
- Howells on track to success with ITC
- ITC debuts latest threadmilling and tapping catalogue
- Game of Thrones goes cutting edge
- ITC introduces a smarter way to rough bore
- Latest back chamfering series