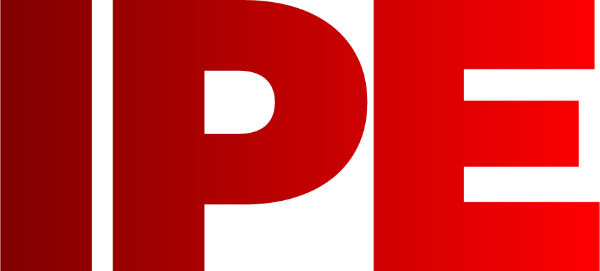
![]() |
Edward Lowton
Editor |
![]() ![]() |
1/15 (1 to 10 of 143)
BCAS expands team with the appointment of second technical officer | 03/07/2025 |
---|---|
BCAS has appointed Steve Downham as its new technical officer. Working alongside Tim Preece, he brings over 26 years of engineering experience in vacuum technology to the team THE BRITISH Compressed Air Society (BCAS) has appointed Steve Downham to further expand its technical team, working alongside Tim Preece as technical officer. Boosting Vacuum Sector Support "It’s a pleasure to join the BCAS team and to use my engineering knowledge to help advise members. I’m planning to meet with lots of members and end users over the coming months, using my skills and experience in the vacuum sector to provide timely and practical advice," said Downham. As a chartered mechanical engineer with a PhD that researched centrifugal pump systems, Downham is no stranger to the world of vacuum technology. For more than 26 years, he has held engineering positions at Edwards Vacuum, latterly as technical lead for new product innovation and research and development. This wealth of engineering knowledge will be a very welcome addition to the Society’s existing technical capabilities, particularly in supporting vacuum technology members and those who are keen to diversify their offer outside of traditional compressed air applications. Navigating Legislation and Compliance Preece will continue to be instrumental in developing standards and legislation and lobbying for the best outcomes for BCAS members. In partnership, Downham will provide guidance on how members can apply and deliver against the requirements set. He will also play an integral role in the Society’s Vacuum committee, as well as working with the training and development team to develop new training courses for members and end users. "We send a very warm welcome to Steve. He has a wealth of knowledge in the vacuum and broader engineering sectors, which will help to strengthen our technical expertise further still," stated Ashley Quartermann, BCAS executive director. "In an ever-changing legislative landscape, it is vital that trade associations remain abreast of new requirements as well as lobbying for the best outcomes for their members and end users. Steve will play an important advisory role in many of these areas of best practice and improved performance." For more information: Tel: +44 (0) 207 935 2464 |
|
|
|
BCAS signs Armed Forces Covenant in industry-wide commitment | 14/05/2025 |
The British Compressed Air Society (BCAS) has signed the Armed Forces Covenant, pledging to support veterans transitioning to civilian careers THE BRITISH Compressed Air Society (BCAS) has signed the Armed Forces Covenant in a ceremony held at Blighmont Reserve Centre in Southampton, marking a new commitment from the industry to those who have served. The Covenant is a commitment from BCAS and its members to the Armed Forces Community. It acknowledges and understands that the armed forces, and their families, should be treated with fairness and respect in the communities, economy and society they serve with their lives. Skills That Translate Through its Armed Forces Working Group, the Society aims to provide meaningful support to ex-military personnel as they transition to a career in civilian life. "The compressed air industry is diverse. It requires specific technical and engineering skills to specify, commission and maintain equipment. It also offers a broad range of other career opportunities in sales and customer service, logistics and administration to name a few," explained BCAS executive director Ashley Quarterman. "We recognise that military experience will equip individuals with many of these skills that are in demand in our sector. Through our working group, we hope to encourage more veterans to consider a career in the compressed air industry. "In return, we want to play our part in helping veterans as they transition into a role in civilian life, by offering fulfilling career opportunities; a transition which can be difficult for many. We are therefore encouraging all our members, and the wider compressed air community to consider the benefits that employing military personnel could bring to their business." Fulfilling Careers Beyond Service BCAS has a number of members with military experience, such as RAF Veteran, James Shaw, MD of JDS Compressors. "My role as a weapons technician was high intensity, and you could never predict what might happen next. We were used to reacting quickly and solving problems. I enjoyed that challenge and, in many ways, we face the same challenges in the compressed air industry," he stated. "Responding quickly to avoid a compressor breakdown, analysing equipment performance and talking with customers to reach the best outcome. It requires a similar mindset." Royal Navy Veteran, Nigel Palmer, who is managing director of SCC Air Compressors UK added: "I am proud to be part of the compressed air industry and its commitment to supporting veterans in their ongoing careers. It is an industry where our skills can be used with great impact - whether it's dealing quickly with equipment breakdown, commissioning a new installation or advising customers on new ways to improve efficiency and performance." Ex Royal Navy Marine engineer and now national sales manager at Atlas Copco, Jason Pollard concluded: "When I left the military, I found that my skills were in demand and could be put to good use in the compressed air industry. Unlike some of my fellow veterans, who have faced numerous barriers when transitioning to a civilian career, I found the compressed air industry to be very receptive to my skillset." For more information: www.armedforcescovenant.gov.uk Tel: +44 (0) 207 935 2464 |
|
|
|
BCAS launches industry-first NVQ for skilled compressed air engineers | 04/04/2025 |
BCAS has launched the NVQ Level 3 Diploma in Installation and Commissioning, the first qualification of its kind for the compressed air industry. THE BRITISH Compressed Air Society (BCAS) has launched its new NVQ Level 3 Diploma in Installation and Commissioning - an industry first that enables experienced compressed air technicians to prove their professional skills and gain a recognised qualification. The NVQ was developed in part to address the competency concerns raised by the Construction Leadership Council regarding personnel working on construction sites. The resulting Compressed Air Pathway is recognised by the Building Engineering and Services Association as a formal industry standard, including Construction Skills Certification Scheme (CSCS) recognition. Validating Expertise Without Additional Training It is designed so that learners can demonstrate their existing knowledge and credentials, without requiring additional training. This gives confidence to end-customers of the engineer's competence, experience and commitment to safe working practices during the installation, commissioning and ongoing maintenance of compressed air systems. The NVQ comprises mandatory units, which include complying with statutory regulations and organisational safety requirements and using and interpreting engineering data and documentation. Emphasis is also given to working efficiently and effectively in engineering and the handing over of maintenance or installation activities to the customer. "The launch of our new NVQ is testament to the significant strides made by the compressed air industry in recent months. We have now developed a recognised qualification which formalises the extensive experience many compressed air engineers already possess," said Terry Collier, BCAS learning and development officer. "Working with our members and other industry bodies, we are proud to introduce this new Compressed Air Pathway to the industry. Together, we are making meaningful progress in enhancing the skills and qualifications of the industry. "Not only does it demonstrate the expertise of our highly skilled sector, but it provides end users with additional reassurance that all health and safety and statutory requirements will be met," he continued. A Collaborative Effort to Elevate Industry Standards "In addition, we have partnered with an external assessment company, TSW Training, who are well respected within the wider engineering sector. TSW Training will be responsible for assessing and quality assuring as technicians work towards assessment. This partnership not only ensures that candidates receive the highest standard of assessment but also aligns with the rigorous requirements mandated by the Construction Leadership Council." Ashley Quarterman, BCAS Executive Director said that the new NVQ further enhances BCAS' wide portfolio of training courses available to engineers and end-users in the compressed air industry. "It forms part of our continued effort to add further value for our members and their customers and would not have been possible without collective effort from the BCAS team and many of our colleagues and partners across the sector," he concluded. The NVQ Level 3 Diploma in installation and Commissioning is now available on the BCAS learning management system website and open for applications. Please visit https://elearning.bcas.org.uk/nvq-level-3-diploma-in-installation-and-commissioning/ For more information: Tel: +44 (0) 207 935 2464 |
|
|
|
BCAS appoints new Learning Support Officer to further enhance training offer | 24/01/2025 |
FAY HUTCHINSON has joined the British Compressed Air Society (BCAS) in the newly created role of Learning Support Officer. Working alongside Terry Collier, BCAS’s learning and development officer, the new role will see BCAS further enhance the breadth and range of compressed air and vacuum training courses and approved accreditations available, with particular focus on increasing participation in its compressed air and vacuum technician (CAVT) apprenticeship. Hutchison has a wealth of training experience, gained in roles both within engineering and the higher education sector. Starting her career in the stainless steel and aluminium sector, she holds a first-class honours degree in business management and a master of business administration (MBA) and has recently completed a level 6 diploma in career guidance and development. "I am really looking forward to using my skills to help further enhance the training support available to our members. I am already speaking to members about our CAVT apprenticeship and some of the ways we can refine it further through progression routes, as well as being able to advise on the range of bursaries and levy funding that could be available," Hutchison stated. Of particular benefit to BCAS and its members is Hutchison’s experience gained during her work with higher education institutes. She has held several employer relationship roles, most recently at the University of Greenwich, where she has secured successful industrial work placements for students during their university studies. She has also been actively involved in encouraging businesses to offer degree apprenticeships, using their apprenticeship levy where appropriate to either bring new talent into the business or to upskill existing members of staff. "The industry is only too aware that recruiting and retaining skilled staff into the compressed air and wider engineering sector is challenging. Offering high-quality training, whether through our apprenticeship scheme or one of our many CPD-approved courses, can help to deliver the next generation of engineers that our sector needs," said Ashley Quarterman, BCAS executive director. "It is great to welcome Fay to the team and to be able to draw on all her experience in both the industrial and education sectors. She understands how effective learning environments can be created, alongside the pressures faced by employers to continually train their teams and this will be of genuine benefit to our members." |
|
|
|
Tackling the skills gap | 26/02/2025 |
BCAS is driving upskilling efforts through flexible courses and resources, supporting employers in addressing the skills gap FIGURES FROM the recent Employer Skills Survey (2022) from the Department for Education show that the amount spent on training in England has dropped to its lowest ever level. In the manufacturing sector, there was also a decrease in employers providing training, a drop of six percentage points in 2017 to 54% in 2022 and the sector was one of the establishments most likely to have skills gaps at 19%. However, there are many employers that are bucking this trend, working with organisations like the British Compressed Air Society (BCAS) to ensure their employees are suitably trained and upskilled. Indeed, Make UK, the Manufacturers’ Organisation states in its 2030 Skills, Closing the Gap report that "The majority of those who will be working in manufacturing in 2030 are already in the workforce. As such, employers are increasingly focused on upskilling and retraining their existing employees, both to ensure that their technical skills keep pace with changing needs, and to retain that talent in the business over the longer term. This is the key priority for manufacturers over the next decade." Why learning and development? We’ll begin by exploring the purpose of learning and development (L&D) activities and how these fit within an organisation's people policies. In simple terms, L&D is about ensuring the right people are on board, with the right skills, at the right time. This is a significant challenge for all HR departments and individuals. However, BCAS is making positive strides, and working in a sector of professional, highly skilled specialists sets us apart, making this a key benefit of investing in one of our many training courses. The role of BCAS BCAS is committed to supporting users of compressed air and its members on this journey. We employ specialists in learning and development as well as technical standards. Some of the current initiatives we are working on with the industry include:
Feedback from individuals and businesses is crucial to the effectiveness of L&D. We are updating training materials and developing new initiatives continually. BCAS remains dedicated to helping member organisations achieve the necessary skill levels in the sector, and users of compressed air to be able to upskill their workforce and have access to unbiased information. Like all businesses, we adapt to the ever-changing external environment and communicate these changes as needed through committee meetings, discussions, and L&D events. A comprehensive range of training courses BCAS offers a diverse range of fully online and blended learning courses tailored to fit the convenience of trainees, whether they're learning from the office or at home. These courses are designed to be flexible, accommodating the pace and place that best suits the learner. Discounts and affordability Courses start at just £35.00, with additional discounts of up to 25% available for customers of BCAS members, along with free associate membership. To access these benefits, customers need only inform BCAS of their compressed air supplier when booking. eLearning Courses
Blended Learning Courses BCAS’s CPD-approved blended learning courses combine online tutorials with guided learning and assessments led by qualified tutors. This format allows for flexible study, with invigilated exams ensuring comprehension and competence.
BCAS’s training courses are a valuable resource for anyone involved in the compressed air industry, offering a range of qualifications from basic safety to advanced technical management. For more information, visit the BCAS eLearning portal at e-learning.bcas.org.uk or email [email protected] For more information: Tel: +44 (0) 207 935 2464 |
|
|
|
CSCS card update: The current state of play | 03/01/2025 |
THE BRITISH Compressed Air Society’s (BCAS) important work to support and influence the proposed changes to the CSCS card continues at pace. The Construction Leadership Council (CLC) is requiring proof of competency in CSCS scheme, covering all industrial sectors. It intends to enforce this from January 2025, using approved apprenticeship schemes to measure competency. The Building Engineering Services Association (BESA) is the industry body that is overseeing the work of the compressed air industry. The skill cards’ situation is exceptionally difficult for everyone in the industry and BCAS understands the pressure that this is placing on organisations. Through numerous meetings and requests for information, the Society continues to lobby for a better outcome. Obtaining a CSCS card via an apprenticeship So far, there is one way to achieve a skills’ card for the compressed air sector. That is through the Compressed Air and Vacuum Technician apprenticeship, which was developed by the BCAS members on the Training and Development Committee. Once an employee is on this scheme, they receive a red trainee card. When they qualify, they can then apply for a gold card. BCAS has formally objected to this requirement for a full apprenticeship qualification on several grounds, as an apprenticeship may not be suitable for many currently serving engineers in this field. The Society is waiting to present to the panel of experts, where it will be highlighting what it considers to be flaws in this argument. Working towards a formal qualification It is the Construction Skills Council’s clear decision that from January 2025 work will not be completed on new construction projects without a skills’ card. To obtain such a card the employee must have an industry-recognised qualification. BESA oversees the compressed air industry. BCAS has had many meetings with the BESA team to find the best outcome for its members and the wider sector. The society argues that allowing an NVQ to be an alternative qualification for our sector is the best way forward. We have worked to:
Next steps BCAS remains committed to apprenticeships where appropriate and working collaboratively with the Construction Skills’ Council to ensure the safety of all employees. The time importance is critical, and the Society continues to push for a swift resolution. Terry Collier is training and development Officer at BCAS Tel: 0207 935 2464 |
|
|
|
Ensuring workplace safety with compressed air | 18/12/2024 |
SAFETY IS a fundamental concern in all workplace settings, including construction sites, factories, and other industrial environments to name a few. Business leaders have a duty to prioritise the safety of their employees and to protect their assets. Compressed air is a versatile energy source, accounting for approximately 10% of all the energy used by industry and must be handled with care. Although the incidence of injuries related to compressed air systems is relatively low in the UK, compressed air systems can pose significant hazards if not properly maintained or the proper precautions taken. Components such as compressors, hoses, pneumatic tools, and electrical connections all have associated risks and the high pressure within these systems can cause serious injuries. Continuous efforts to enhance safety standards and reduce complacency are therefore essential. Barriers to safety Research indicates a strong correlation between complacency and workplace incidents. AA research paper headed Identifying Root Causes of Construction Accidents published in 2000 by the Journal of Construction Engineering and Management identified human factors, particularly complacency, as significant contributors to accidents in the construction industry. This underscores the necessity of constant vigilance and strict adherence to safety protocols. One challenge in promoting a culture of safety is the generational gap in safety perceptions. While younger workers often view new safety measures as standard practice, older employees that have been carrying out their duties for some years may regard them as unnecessary. Bridging this gap is vital for the successful implementation and acceptance of safety protocols. The importance of compressed air safety Training and education Comprehensive training is crucial for all operators working with compressed air systems. Training programs should include detailed instructions on the safe and efficient operation of compressors, awareness of potential hazards, and strategies for risk mitigation. Air compressor safety tips
Conclusion Safety is an ongoing commitment in any workplace. Implementing thorough training and safety measures for compressed air systems is essential to protect workers, prevent accidents, and ensure equipment longevity. To find out more about the Certificate in Working Safely with Compressed Air course from BCAS, please visit: tinyurl.com/5z9e8ppm Terry Collier is training and development officer at BCAS Tel: 0207 935 2464 |
|
|
|
Best practice for sensor calibration | 18/11/2024 |
CALIBRATION IS essential in the compressed air industry to ensure systems operate efficiently, safely, and reliably. In an industry where precision is crucial, routine sensor maintenance and calibration are indispensable for maintaining the high standards required in modern manufacturing. Calibration of sensors in a compressed air system should be conducted regularly to ensure accurate measurements. The frequency of the sensor checking should be proportional to the safety-critical nature of the process or dependant on the sensor’s impact on process variability. For critical measurements, sensors should be checked frequently to ensure accuracy. If a measurement point significantly influences process control - for example, 10% or higher - the sensor should be checked regularly until sufficient data is collected to extend the checking interval. For less critical measurements that have, for instance, only a 0.01% influence on the control of the process, the checking interval can be extended or, in some cases, stopped altogether based on collected data. Methods for checking and calibrating sensors There are two primary methods for checking and calibrating sensors in a compressed air system: routine in-situ checking and laboratory calibration. Both methods require accurate recording and documentation of the check/calibration procedure. Routine in-situ checking: This involves using a portable checking device to verify the accuracy of the installed sensor without removing it from the process. The portable device is brought to the sensor's measuring point, and readings are compared with the live online sensor. To ensure reliability, a minimum of three measuring points should be checked across the sensor's likely working range. This is known as an ‘as found’ check as opposed to a calibration or recalibration. It is quick and non-disruptive to the process, but less accurate than laboratory calibration. Laboratory calibration: This is a more thorough and accurate method, which involves removing the sensor from the compressed air system and calibrating it in a controlled environment, such as an approved laboratory or workshop. The sensor is calibrated using a reference standard with an inaccuracy factor lower than the device being checked. It is a controlled process, using a trained operator to calibrate the sensor, across multiple points, ensuring accuracy throughout its range. This method typically includes both an ‘as found’ check and, if necessary, an ‘as left’ (adjusted) calibration to bring the sensor back into specification. While laboratory calibration is more accurate, it requires more time and a spare calibrated sensor to be installed temporarily to avoid process interruption. Examples of routine checks These two examples of routine checks in a compressed air treatment system illustrate the importance of regular sensor maintenance and calibration:
Tel: 0207 935 2464 |
|
|
|
Mitigating rising supply costs with on-site nitrogen generation | 09/12/2024 |
FROM FOOD preservation, to chemical manufacturing, to electronics’ production - industry uses nitrogen gas extensively for its inert properties, helping to prevent oxidation and combustion. Yet purchasing supplies of the gas externally can be costly, meaning many manufacturers are turning to their compressed air systems to generate guaranteed-purity nitrogen on site. Nitrogen generation - how does it work? Ambient air typically consists of approximately 78% nitrogen, 21% oxygen, and 1% made up of other gases, including water vapor and carbon dioxide. Once the ambient air is drawn into the system, it is then compressed to a higher pressure before downstream filters and dryers purify the air to remove particulates and moisture. The purified air is then directed to a nitrogen generator, using either membrane separation or pressure swing adsorption technologies - effectively separating the nitrogen gas from the other components in the treated air. The generated nitrogen is then stored in a buffer tank to ensure a steady supply and consistent pressure. Advanced control systems monitor and regulate the purity and flow rate of the nitrogen, ensuring it meets the specific requirements of the application. One of the key advantages of on-site nitrogen generation is its seamless integration with existing compressed air systems. These systems can be tailored to specific needs, offering precise control over nitrogen purity and flow rates. Adjustments can be made quickly and easily, providing flexibility for industries with varying nitrogen demands. The cost-saving benefits of on-site nitrogen production
By generating nitrogen on-site, manufacturers can eliminate the recurring expense of purchasing nitrogen cylinders or bulk liquid nitrogen – and the associated time and expense of scheduling deliveries. Logistics are also simplified, with less time and labour required for managing nitrogen supplies, allowing factory personnel to focus on core activities.
On-site nitrogen generation systems only produce nitrogen as it is needed, adjusting production rates in real-time to align with operation needs. This reduces the necessity for large and expensive storage tanks or cylinders and the ongoing management of inventory.
As these systems produce nitrogen only when needed, operators can avoid the energy waste associated with overproduction and storage. In addition, on-site systems can be scaled up or down based on demand, ensuring cost-effective nitrogen production without overcapacity or shortages.
On-site generation ensures a continuous supply of nitrogen, minimising production downtime due to delayed or missed deliveries. Routine maintenance can also be planned around peaks and troughs in demand, enhancing operational efficiency.
Self-generating the nitrogen supply required helps operators mitigate for market fluctuations and price increases associated with a bought-in supply, enabling a more predictable and stable cost structure.
Long-term operational savings often outweigh the upfront costs of the nitrogen generation equipment, and it is not uncommon to achieve savings in the region of 90%, compared to the cost of bought-in nitrogen cylinders. Ashley Quarterman is executive director designate at BCAS Tel: 0207 935 2464 |
|
|
|
Maintenance best practice for compressed air | 04/11/2024 |
COMPRESSORS ARE the workhorses of many industrial applications, often running continuously in challenging conditions. Add to this the rising cost of energy and it is vital that compressed air systems operate efficiently. Here are 10 essential steps to maintain and extend the lifespan of your compressed air system - with a handy troubleshooting guide for the most common issues. 1. Implement a regular maintenance schedule Regular maintenance is vital for the efficiency and longevity of your compressed air system. Always follow the manufacturer’s recommended service intervals and procedures. Routine checks help avoid energy losses due to poorly performing equipment and prevent unplanned outages. Establish a maintenance regime that includes regular checks of all components of the system, from the compressor to the ancillary equipment. 2. Consider compressor location The location of your compressor significantly impacts its efficiency, with high temperatures likely to increase energy consumption and the potential for equipment failure. Ensure that compressors are situated in a dry, clean and cool area, installing additional ventilation if necessary to help prevent costly repairs. 3. Conduct regular air leak inspections Air leaks are very costly. Even a small 2mm hole can waste over £1,249 annually in energy costs, but as air leakage presents no danger, it is often left unchecked. High leak rates can cause pressure fluctuations, slowing down production and causing the compressor to work harder (and therefore consuming more energy) to generate the same volumes of air. Inspect the compressed air pipework for leaks and implement a robust repair regime by tagging the most serious leaks first and remedying before moving on to smaller leaks. 4. Monitor and replace inlet filters Inlet filters prevent contaminants from entering the compressor and causing unnecessary damage to components parts. Check and replace these filters routinely before the pressure drop across them becomes significant. Clean filters ensure the compressor operates efficiently, reducing energy consumption and extending the equipment's lifespan. 5. Don’t neglect ancillary equipment A compressed air system comprises more than just the compressor alone. Regularly maintain ancillary equipment such as dryers, filters, air receivers, and pipework. Neglecting these components can lead to inefficiencies and system failures. 6. Embrace predictive maintenance Moving from reactive to predictive maintenance can save time and money. Predictive maintenance uses data analytics and Industry 4.0 technologies to anticipate potential failures before they occur - and with so many technologies now available, investment can prove very cost effective. Indeed, the payback period can be rapid, compared to the costs of unexpected downtime, helping keep your compressed air system operating reliably and with high energy efficiency. 7. Use genuine spare parts Always opt for genuine spare parts designed specifically for your compressor. While cheaper alternatives may seem cost-effective, they can compromise system performance and lead to failures. Genuine components are designed specifically for the equipment they are intended for, helping avoid unnecessary maintenance or rework, while maintaining excellent system performance. 8. Train personnel properly Good housekeeping techniques can soon pay dividends, so ensure that all personnel involved in the operation and maintenance of the compressed air system are trained. A competent operator can help in the early identification of issues and thorough maintenance practices, helping avoid a small, easily rectified problem from becoming a major equipment breakdown. 9. Implement energy management practices Good energy management isn’t only crucial for cost control. It also plays a strategic role in a site’s environmental sustainability commitments. Installing energy-efficient compressors, variable speed drives and ancillary equipment will clearly help in the drive to reduce electricity consumption, but there are numerous maintenance regimes that will help to lower consumption too. For example, switch off compressors when they are not in use to avoid idling, identify and fix air leaks and replace inefficient components with energy-efficient alternatives. 10. Perform regular system audits Regular audits of the compressed air system can identify inefficiencies and areas for improvement. BCAS members can assist with data logging - helping you to understand your system’s performance and pinpointing specific issues that may not be apparent during routine maintenance. Troubleshooting common issues Inconsistent pressure Inconsistent pressure is a common issue in compressed air systems. It can be caused by air leaks, clogged filters, or malfunctioning pressure regulators. Inspect the piping and components regularly for blockages or build-up of debris that could restrict airflow. If pressure fluctuations persist, consider consulting a BCAS member to perform a thorough system analysis. They can install pressure regulators to ensure consistent pressure throughout the system, which are easy to adjust to maintain the system’s requirements. Excessive noise Excessive noise can indicate air leaks, loose components, or worn-out parts. Start by inspecting and tightening all components, ensuring they are secure. Check for worn or damaged parts such as bearings and belts, lubricating or replacing them as necessary. Clean or replace dirty air filters to improve airflow and reduce noise. If the problem persists and it is not feasible to install the compressor away from the point of use, your compressed air specialist may be able to add soundproofing materials or enclosures. Contamination Contaminants like oil or particulate matter can degrade product quality and damage pneumatic equipment. Install and replace air filters regularly to remove contaminants. Ensure that the compressor is operating within the recommended parameters to minimise oil carryover. And remember to dispose of waste oil in line with the Hazardous Waste Regulations 2005 Moisture in the air system Excess moisture can cause rust, corrosion, and damage to pneumatic tools and equipment – and in stringent hygienic environments, will not provide the high air quality levels demanded by the application. First, ensure that condensate drains are functioning correctly and are emptied regularly. Next, audit your downstream air dryers to ensure they are removing the necessary moisture from the compressed air. Finally, check and replace filters and moisture traps periodically to ensure they are working effectively. Insufficient flow When a compressed air system is unable to deliver the required volume of air, it can impact significantly on production output. Begin by measuring the flow rate to ensure it meets the demands of the system, using flow meters to monitor and diagnose. The issue could be at the point of generation and require additional air compressors, or a system redesign using base load compressors to handle the main demand, with speed-regulated units to handle peaks and troughs. Alternatively, it may be that the system has inadequate storage, in which case, check the capacity of air receivers to ensure they can handle peak loads. Finally, continue to monitor the air pipework network to ensure it is sized appropriately and free from any obstructions that could restrict airflow. Ashley Quarterman is executive director designate at BCAS Tel: 0207 935 2464 |
|
|