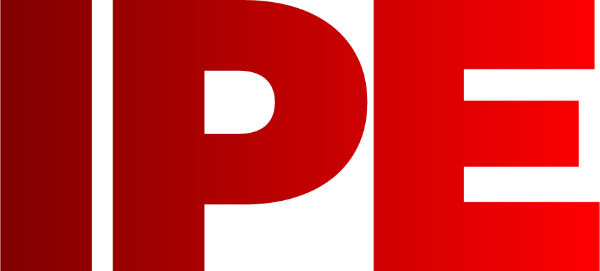
![]() |
Edward Lowton
Editor |
![]() ![]() |
Home> | Energy Management | >Compressors & ancillary equipment | >Ensuring workplace safety with compressed air |
Ensuring workplace safety with compressed air
18 December 2024
SAFETY IS a fundamental concern in all workplace settings, including construction sites, factories, and other industrial environments to name a few. Business leaders have a duty to prioritise the safety of their employees and to protect their assets.

Compressed air is a versatile energy source, accounting for approximately 10% of all the energy used by industry and must be handled with care. Although the incidence of injuries related to compressed air systems is relatively low in the UK, compressed air systems can pose significant hazards if not properly maintained or the proper precautions taken.
Components such as compressors, hoses, pneumatic tools, and electrical connections all have associated risks and the high pressure within these systems can cause serious injuries. Continuous efforts to enhance safety standards and reduce complacency are therefore essential.
Barriers to safety
Research indicates a strong correlation between complacency and workplace incidents. AA research paper headed Identifying Root Causes of Construction Accidents published in 2000 by the Journal of Construction Engineering and Management identified human factors, particularly complacency, as significant contributors to accidents in the construction industry. This underscores the necessity of constant vigilance and strict adherence to safety protocols.
One challenge in promoting a culture of safety is the generational gap in safety perceptions. While younger workers often view new safety measures as standard practice, older employees that have been carrying out their duties for some years may regard them as unnecessary. Bridging this gap is vital for the successful implementation and acceptance of safety protocols.
The importance of compressed air safety
Training and education
Comprehensive training is crucial for all operators working with compressed air systems. Training programs should include detailed instructions on the safe and efficient operation of compressors, awareness of potential hazards, and strategies for risk mitigation.
Air compressor safety tips
- Training: BCAS recommends comprehensive training for all operators, including an understanding of relevant safety standards before operating any equipment.
- Equipment and workspace setup: Operators should follow the manufacturer’s guidelines for the setup of equipment and workspaces, including the installation of safety devices such as pressure relief valves.
- Pre-operation checks: Sites should standardise regular pre-start safety checks for all components of the compressor system to ensure safe and efficient operation.
- Maintenance: Regular maintenance, including checks of filters, dryers, air receivers, and pipework is vital for extending the life of the system and maintaining air quality.
- Good housekeeping and staff involvement: Compressed air is a valuable resource, and leaks should be addressed promptly. Common sources of wastage include leaks, leaving air-consuming equipment running during breaks, and using compressed air unnecessarily for cleaning benches and equipment. Encouraging staff to report and identify instances of wasted air usage is critical.
Conclusion
Safety is an ongoing commitment in any workplace. Implementing thorough training and safety measures for compressed air systems is essential to protect workers, prevent accidents, and ensure equipment longevity.
To find out more about the Certificate in Working Safely with Compressed Air course from BCAS, please visit: tinyurl.com/5z9e8ppm
Terry Collier is training and development officer at BCAS
Tel: 0207 935 2464
- The need to put safety first
- BCAS welcomes new Energy Bill Relief Scheme
- Trade associations: Promoting and defending members' interests
- Efficiency gains in vacuum technology
- BCAS offers 25% discount on ISO 8573 air quality standard training
- New standard targets energy performance
- BCAS supports new UK-based supply chain development platform
- BCAS appoints Terry Collier to further strengthen its training offer
- Setting the standard for compressed air quality
- Cold weather warning