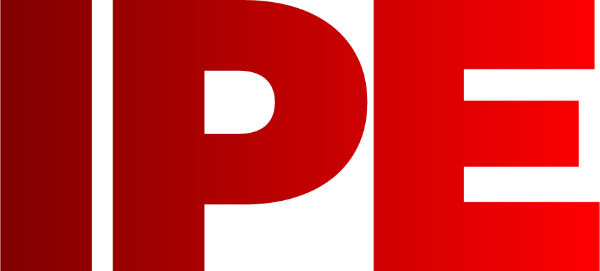
![]() |
Edward Lowton
Editor |
![]() ![]() |
Home> | Energy Management | >Compressors & ancillary equipment | >Mitigating rising supply costs with on-site nitrogen generation |
Mitigating rising supply costs with on-site nitrogen generation
09 December 2024
FROM FOOD preservation, to chemical manufacturing, to electronics’ production - industry uses nitrogen gas extensively for its inert properties, helping to prevent oxidation and combustion.

Yet purchasing supplies of the gas externally can be costly, meaning many manufacturers are turning to their compressed air systems to generate guaranteed-purity nitrogen on site.
Nitrogen generation - how does it work?
Ambient air typically consists of approximately 78% nitrogen, 21% oxygen, and 1% made up of other gases, including water vapor and carbon dioxide.
Once the ambient air is drawn into the system, it is then compressed to a higher pressure before downstream filters and dryers purify the air to remove particulates and moisture. The purified air is then directed to a nitrogen generator, using either membrane separation or pressure swing adsorption technologies - effectively separating the nitrogen gas from the other components in the treated air.
The generated nitrogen is then stored in a buffer tank to ensure a steady supply and consistent pressure. Advanced control systems monitor and regulate the purity and flow rate of the nitrogen, ensuring it meets the specific requirements of the application.
One of the key advantages of on-site nitrogen generation is its seamless integration with existing compressed air systems. These systems can be tailored to specific needs, offering precise control over nitrogen purity and flow rates. Adjustments can be made quickly and easily, providing flexibility for industries with varying nitrogen demands.
The cost-saving benefits of on-site nitrogen production
- Eliminates purchase and delivery costs
By generating nitrogen on-site, manufacturers can eliminate the recurring expense of purchasing nitrogen cylinders or bulk liquid nitrogen – and the associated time and expense of scheduling deliveries. Logistics are also simplified, with less time and labour required for managing nitrogen supplies, allowing factory personnel to focus on core activities.
- Lower storage costs
On-site nitrogen generation systems only produce nitrogen as it is needed, adjusting production rates in real-time to align with operation needs. This reduces the necessity for large and expensive storage tanks or cylinders and the ongoing management of inventory.
- Energy efficiency
As these systems produce nitrogen only when needed, operators can avoid the energy waste associated with overproduction and storage. In addition, on-site systems can be scaled up or down based on demand, ensuring cost-effective nitrogen production without overcapacity or shortages.
- Reduced downtime
On-site generation ensures a continuous supply of nitrogen, minimising production downtime due to delayed or missed deliveries. Routine maintenance can also be planned around peaks and troughs in demand, enhancing operational efficiency.
- Mitigation from market volatility
Self-generating the nitrogen supply required helps operators mitigate for market fluctuations and price increases associated with a bought-in supply, enabling a more predictable and stable cost structure.
- Long-term investment
Long-term operational savings often outweigh the upfront costs of the nitrogen generation equipment, and it is not uncommon to achieve savings in the region of 90%, compared to the cost of bought-in nitrogen cylinders.
Ashley Quarterman is executive director designate at BCAS
Tel: 0207 935 2464
- Energy efficiency and industrial compressors
- Compressed air gun use in machine workshops
- Compressed air pipework: Best practice
- Update From Europe
- Making the most of training opportunities
- Adapting to the circular economy.
- Original way to boost efficiency
- Ensuring workplace safety with compressed air
- Improving compressed air practices to cut energy wastage
- Enhancing safety through efficient maintenance