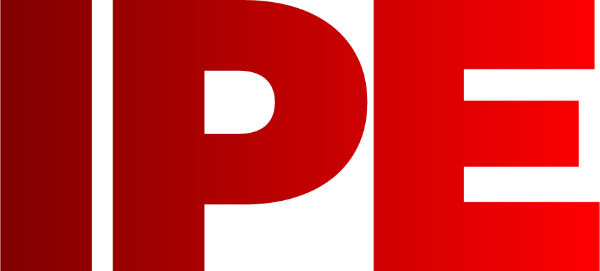
![]() |
Edward Lowton
Editor |
![]() ![]() |
Home> | Energy Management | >Compressors & ancillary equipment | >Maintenance best practice for compressed air |
Maintenance best practice for compressed air
04 November 2024
COMPRESSORS ARE the workhorses of many industrial applications, often running continuously in challenging conditions. Add to this the rising cost of energy and it is vital that compressed air systems operate efficiently. Here are 10 essential steps to maintain and extend the lifespan of your compressed air system - with a handy troubleshooting guide for the most common issues.

1. Implement a regular maintenance schedule
Regular maintenance is vital for the efficiency and longevity of your compressed air system. Always follow the manufacturer’s recommended service intervals and procedures. Routine checks help avoid energy losses due to poorly performing equipment and prevent unplanned outages. Establish a maintenance regime that includes regular checks of all components of the system, from the compressor to the ancillary equipment.
2. Consider compressor location
The location of your compressor significantly impacts its efficiency, with high temperatures likely to increase energy consumption and the potential for equipment failure. Ensure that compressors are situated in a dry, clean and cool area, installing additional ventilation if necessary to help prevent costly repairs.
3. Conduct regular air leak inspections
Air leaks are very costly. Even a small 2mm hole can waste over £1,249 annually in energy costs, but as air leakage presents no danger, it is often left unchecked. High leak rates can cause pressure fluctuations, slowing down production and causing the compressor to work harder (and therefore consuming more energy) to generate the same volumes of air.
Inspect the compressed air pipework for leaks and implement a robust repair regime by tagging the most serious leaks first and remedying before moving on to smaller leaks.
4. Monitor and replace inlet filters
Inlet filters prevent contaminants from entering the compressor and causing unnecessary damage to components parts.
Check and replace these filters routinely before the pressure drop across them becomes significant. Clean filters ensure the compressor operates efficiently, reducing energy consumption and extending the equipment's lifespan.
5. Don’t neglect ancillary equipment
A compressed air system comprises more than just the compressor alone. Regularly maintain ancillary equipment such as dryers, filters, air receivers, and pipework. Neglecting these components can lead to inefficiencies and system failures.
6. Embrace predictive maintenance
Moving from reactive to predictive maintenance can save time and money. Predictive maintenance uses data analytics and Industry 4.0 technologies to anticipate potential failures before they occur - and with so many technologies now available, investment can prove very cost effective.
Indeed, the payback period can be rapid, compared to the costs of unexpected downtime, helping keep your compressed air system operating reliably and with high energy efficiency.
7. Use genuine spare parts
Always opt for genuine spare parts designed specifically for your compressor. While cheaper alternatives may seem cost-effective, they can compromise system performance and lead to failures. Genuine components are designed specifically for the equipment they are intended for, helping avoid unnecessary maintenance or rework, while maintaining excellent system performance.
8. Train personnel properly
Good housekeeping techniques can soon pay dividends, so ensure that all personnel involved in the operation and maintenance of the compressed air system are trained. A competent operator can help in the early identification of issues and thorough maintenance practices, helping avoid a small, easily rectified problem from becoming a major equipment breakdown.
9. Implement energy management practices
Good energy management isn’t only crucial for cost control. It also plays a strategic role in a site’s environmental sustainability commitments.
Installing energy-efficient compressors, variable speed drives and ancillary equipment will clearly help in the drive to reduce electricity consumption, but there are numerous maintenance regimes that will help to lower consumption too.
For example, switch off compressors when they are not in use to avoid idling, identify and fix air leaks and replace inefficient components with energy-efficient alternatives.
10. Perform regular system audits
Regular audits of the compressed air system can identify inefficiencies and areas for improvement. BCAS members can assist with data logging - helping you to understand your system’s performance and pinpointing specific issues that may not be apparent during routine maintenance.
Troubleshooting common issues
Inconsistent pressure
Inconsistent pressure is a common issue in compressed air systems. It can be caused by air leaks, clogged filters, or malfunctioning pressure regulators. Inspect the piping and components regularly for blockages or build-up of debris that could restrict airflow.
If pressure fluctuations persist, consider consulting a BCAS member to perform a thorough system analysis. They can install pressure regulators to ensure consistent pressure throughout the system, which are easy to adjust to maintain the system’s requirements.
Excessive noise
Excessive noise can indicate air leaks, loose components, or worn-out parts. Start by inspecting and tightening all components, ensuring they are secure. Check for worn or damaged parts such as bearings and belts, lubricating or replacing them as necessary. Clean or replace dirty air filters to improve airflow and reduce noise.
If the problem persists and it is not feasible to install the compressor away from the point of use, your compressed air specialist may be able to add soundproofing materials or enclosures.
Contamination
Contaminants like oil or particulate matter can degrade product quality and damage pneumatic equipment. Install and replace air filters regularly to remove contaminants.
Ensure that the compressor is operating within the recommended parameters to minimise oil carryover. And remember to dispose of waste oil in line with the Hazardous Waste Regulations 2005
Moisture in the air system
Excess moisture can cause rust, corrosion, and damage to pneumatic tools and equipment – and in stringent hygienic environments, will not provide the high air quality levels demanded by the application.
First, ensure that condensate drains are functioning correctly and are emptied regularly. Next, audit your downstream air dryers to ensure they are removing the necessary moisture from the compressed air. Finally, check and replace filters and moisture traps periodically to ensure they are working effectively.
Insufficient flow
When a compressed air system is unable to deliver the required volume of air, it can impact significantly on production output. Begin by measuring the flow rate to ensure it meets the demands of the system, using flow meters to monitor and diagnose.
The issue could be at the point of generation and require additional air compressors, or a system redesign using base load compressors to handle the main demand, with speed-regulated units to handle peaks and troughs. Alternatively, it may be that the system has inadequate storage, in which case, check the capacity of air receivers to ensure they can handle peak loads.
Finally, continue to monitor the air pipework network to ensure it is sized appropriately and free from any obstructions that could restrict airflow.
Ashley Quarterman is executive director designate at BCAS
Tel: 0207 935 2464
- Update From Europe
- F-Gas update and membership offer
- BCAS launches industry-first NVQ for skilled compressed air engineers
- Energy efficiency: Work in progress
- Legislation in a post-Brexit landscape
- Trade associations: Promoting and defending members' interests
- Setting the standard for compressed air quality
- Working safely with compressed air
- Maximising eco efficiency
- PSSR - compliant and competent