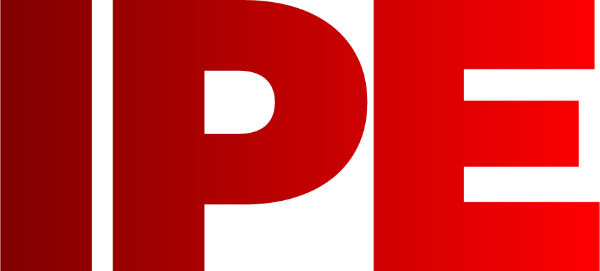
![]() |
Edward Lowton
Editor |
![]() ![]() |
1/2 (1 to 10 of 19)
MasterMover extends Power Steered range | 22/09/2022 |
---|---|
MASTERMOVER HAS debuted the latest addition to its Power Steered range with the introduction of the PS800+. Originally created to fulfil a bespoke customer requirement, the PS800+ has been designed by in-house engineers and added to the Power Steered range to meet the growing demands of the business, where customers regularly ask for bespoke or personalised machines to drive safe and efficient movement of heavy and/or awkward loads. The PS800+ joins the already-popular PS3000+, which has the capacity to manoeuvre up to 30,000kg, and its addition to the range offers customers a smaller solution with a capability to move loads of up to 8,000kg. The Power Steered range features remote-controlled operation, allowing operators to take the optimal viewing point for increased visibility and improved safety. Multi-Link technology The Power Steered range include innovative Multi-Link technology, enabling two or more machines to work together in sync. This makes the movement of particularly long or awkward loads simple to achieve. For example, the manufacturer of aeroplane wings – notoriously tricky and heavy items to move - can use two machines at each end of the load to manoeuvre them carefully and efficiently. A simple remote-control operation means only one operator is required, cutting down on manpower and increasing productivity. "Here at MasterMover, we are continuously working to evolve and improve on existing products and ranges," said James Jones, partner and director at MasterMover. "The new PS800+ will provide a greater choice and flexibility for our customers while still delivering the same great quality and service they’ve come to expect from us. "As with a number of our machines, the PS800+ was originally created to meet the specific need of a customer in the aerospace industry. However, it is now available as an option within our product portfolio, giving customers greater choice and flexibility, especially in terms of remote-controlled movement of loads," hed added Specifications and further details The PS800+ safety features include four emergency stop buttons, an audible horn, a flashing beacon with audible alarm, a wireless transmitter with a safety shut-off if the signal is lost or interrupted, a caster guard preventing entrapment and a hydraulic coupling that provides maximum load security.
|
|
|
|
Ballroom shouldn’t be backbreaking | 27/05/2021 |
The ‘ballroom’ concept is the much trumpeted vision of the pharmaceutical ‘factory of the future’ but does this development create new safety risks for employees? Hugh Freer looks at some of the issues WHEN COMBINED with single use technologies it’s easy to see the attraction of ‘ballroom’ production facilities. Flexibility, fast changeovers, reduced CAPEX costs and increased output are just a few of the reasons the concept has taken hold with many of the industry’s big players. But central to the ballroom idea is the need for process equipment to be mobile. This fundamental change brings with it increased risk as production staff are forced to resort to muscle power alone when moving process equipment around the ‘ballroom’. The modern production facility of today contains a wealth of wheeled equipment with weights often exceeding four figures. A typical 300L reactor will tip the scales at over 800kg and a 1000L mixer will very likely weigh more than 1300kg. With weights like these, neither would be suitable for manual handling, regardless of whether the equipment manufacturer has included handles. So, what’s the solution? Well, contrary to what many might think, it isn’t a pallet jack. While every facility has got them lying around, they’re designed to move pallets. If you use a pallet jack to lift a tank off the floor, you’ve immediately raised its centre of gravity. At the same time, you’ve lost the stability offered by the tanks’ caster wheels. A far safer option is to keep the tank on the ground and use a mechanical aid that’s purpose built for pulling and pushing heavy wheeled loads. That’s where the pedestrian electric tug comes in.
A pedestrian tug delivers a level of control and precision manoeuvring capability that simply can’t be achieved when moving heavy loads by hand
Available in various capacities and configurations, an electric tug is an external drive system that can be hitched to any piece of mobile process equipment. Its function is to eliminate the manual push and pull from moving things like tanks or chromatography columns. At the same time, a pedestrian tug delivers a level of control and precision manoeuvring capability that simply can’t be achieved when moving heavy loads by hand. The ballroom concept: 3 things to consider 1. Process equipment specification If you’re buying new equipment then it’s a great opportunity to ensure compatibility with a tug at the drawing stage. While modifying existing process equipment is simple enough, there can be no doubt that it’s easier and cheaper to ensure that new equipment is tow tug compatible at the specification stage. 2. Not all tugs are equal The last thing you want when buying an electric tug is a machine that doesn’t have the power or the necessary grip to move the load. There’s plenty of ‘optimistic’ tug marketing out there for products that claim to move heavy weights with ease. An easy way to separate the good from the bad is to look for tug manufacturers who readily provide photo and video evidence of their machines moving the kind of things that you want to move in environments that look like yours. You can also ask them to cut the sales pitch and provide an engineering explanation as to exactly how the machine will achieve the required power and grip to move your load. 3. New wheels can help…. a lot! Not everything in the ballroom needs a mechanical aid. Swapping out caster wheels for high grade equivalents that reduce friction can make a huge difference ergonomically. As always, you get what you pay for. Typically, higher grade casters will be more expensive but you’re paying for quality tyre materials that will reduce friction and prolong the life of the product. At the same time, you’ll be getting bearings both in the wheel and top plate that are designed specifically to minimise resistance. These simple tweaks carry cost but bring with them benefits, both in terms of ergonomics and product life. Pedestrian electric tugs that are purpose built for cleanroom use offer the perfect solution to ensure speed and flexibility of production while ensuring safety for staff. Hugh Freer is president, MasterMover |
|
|
|
Boosting productivity: Moving matters | 26/07/2017 |
Many businesses find that moving products through the supply chain creates a lot of non-productive time. Here, Andy Owen, managing director of electric tug specialist MasterMover, suggests how businesses can improve efficiency and productivity. A survey conducted by Salary.com in 2014 found that 89% of employees waste at least some time at work, 20% more than the previous year. In particular, 94% of engineering, manufacturing and construction professionals admitted to wasting time. When you look at these figures against the backdrop of the productivity crisis that many countries are reported to be facing, it paints a worrying picture. As production levels drop and wasted time increases, businesses must do everything they can to improve productivity. However, it's not just intentionally wasted time that's the culprit. A lot of wasted time occurs as part of the warehousing and manufacturing process itself. The first step is to determine where efficiency can be improved. This waste can come from overproduction, transportation, over-processing, waiting, inventory, defects, motion or creativity. This causes employees to spend time and exert effort on tasks that are not essential to production so it is vital that companies eliminate these. Plant managers must assess the main causes of non-value added time (NVAT) in their supply chain. This is a common problem in the aerospace industry. Engineers need a large industrial load-carrier to move large and valuable parts such as wings across the plant as part of a staged production process. Due to the size and value of the part, the carriers often need to be operated by a specially trained member of staff and may take hours to suitably strap the part up before it can be safely moved. Although not all industries work on the same scale as an aerospace factory and an engineer might only spend five minutes waiting for a part each time, this will accumulate and account for significantly more over the course of a working week. Reducing NVAT Any plant manager that sees the benefits of reducing non-value added time would want to implement the policy to increase cost savings and production but may not know how to begin. By going on to the factory floor, or speaking to employees, plant managers will discover ways to reduce non-value added time. Employees may complain of having to bend down to pick up a part or walk a distance to find a component, which will have an impact on their overall productivity. Businesses could act on examples of NVAT in several ways. A cost-effective example of this is for plant managers to invest in powerful electric tugs for large or heavy-duty loads. These pedestrian operated tugs allow a single engineer to safely transport heavy parts across plants with ease, reducing NVAT by eliminating the need for waiting or specialist assistance. Of course, this is only one way businesses can reduce NVAT. In order to truly maximise efficiency, businesses must adopt a lean manufacturing approach and slowly introduce changes. Each incremental improvement, such as saving five minutes wastage per day in assembly, is one step closer to creating a company culture of efficiency. Plant managers can take action to ensure that work time is spent productively; this means more time working and less time waiting, decreasing costs and improving output. |
|
|
|
All-terrain tug released | 28/06/2017 |
MasterMover is powering up its range of all-terrain load moving equipment with the new ATT400+, a powerful electric tug with a high performance hydraulic coupling. The ATT400+ allows plant engineers, maintenance staff and handling operators in industrial environments to move heavy loads of up to 5,000kg on castors or 40,000kg on rails. Due to the nature of industrial environments, plant staff are often required to handle heavy products or components across uneven or cluttered floor spaces. This poses a challenge for traditional load handling equipment, with operators often requiring the use of forklifts or cumbersome alternatives that reduce productivity and create safety risks. The ATT400+ electric tug allows pedestrian operators to effectively and efficiently handle heavy loads on all surfaces, with the tug’s specially designed hydraulic arm transferring the load’s weight onto the wheels. This, in addition to the redesigned body of the tug and puncture-proof tyres, means that staff can handle up to five tonnes in any operating condition. MasterMover has redesigned the body of the tug to generate more traction. The main wheel has been moved forward and is now reinforced by a smaller supporting wheel at the back, which provides better balance. |
|
|
|
The problem with engineering apprenticeships | 24/04/2017 |
One of the most pressing problems for the UK industrial sector in recent years has been the skills shortage, an issue that will once again be at the centre of the public's consciousness in light of the UK Government's recently-introduced apprenticeship levy. Here, Andy Owen, managing director of electric tug specialist, MasterMover, explores why the engineering skills problem is persisting — and what businesses can do about it. The last five years have been a tumultuous period for the UK engineering industry. While stability has gradually been restored in the years following the financial crash, the industrial sector continues to face an uncertain future. This is driven by what has been dubbed the skills gap, in which the volume of skilled engineers entering the industry falls short of the growing demand for engineers. Fortunately, the situation is improving. According to the http://www.engineeringuk.com/report-2017/ 2017 state of engineering report by Engineering UK, support from the education system has led to an increased interest in engineering careers among young people. Now, the UK government has put an apprenticeship levy in place to persuade larger engineering businesses to employ more apprentices. Herein lies the fundamental problem with many of the current apprenticeship schemes in the engineering industry. By introducing a levy to coerce businesses into offering apprenticeships, the UK Government is taking the wrong steps to achieve the right goal. Businesses must make apprentices integral to their strategies rather than a financially-motivated afterthought. For example, MasterMover takes on many apprentices each year across all departments from design engineering to finance. During the apprenticeship, we ensure that learners are equipped with practical skills rather than just experience of shadowing an engineer. This makes it mutually beneficial, particularly for engineering apprentices, as the company gets extra work capacity and the apprentice gets valuable skills development, as well as the opportunity to see their work finalised and shipped worldwide. This is critical in ensuring a sustainable future for both the company and the industry itself. In the http://www.theiet.org/membership/member-news/42a/2016-skills-survey.cfm 2016 skills and demand in industry survey, the Institution of Engineering and Technology (IET) found that 50% of engineering companies believe typical new recruits do not meet their expectations. This can be avoided by actively investing in apprenticeships and shaping new recruits into effective engineers. Naomi Climer, president of the IET, has echoed this sentiment. Following the 2016 survey, Climer stated: “It is more important than ever that we develop the next generation of home grown engineering and technology talent.” This cannot be accomplished unless businesses rethink apprenticeship schemes to provide the most benefit to both parties and cultivate talent. The apprenticeship levy is certainly an important development that underlines the importance of apprentices in the future of engineering, but businesses must change their approach and attitudes towards apprenticeships to realise this future. While the skills shortage has been the key talking point of recent years, it does not have to remain this way. |
|
|
|
Just-in-time: Safe delivery | 02/12/2016 |
Research from Kansas State University suggests that 71% of senior manufacturing executives have used some form of the just-in-time (JIT) manufacturing method in their processes. Here, Andy Owen, managing director of electric tug specialist MasterMover, offers advice on how businesses can successfully manage a system based on JIT and improve their safety record Developed in Japan in the 1960s and 70s, the concept of just-in-time is that a business holds no stock. It relies on deliveries of materials and components to arrive just in time to manufacture and fulfil a customer order, saving space and reducing cost. Having a just-in-time strategy puts pressure on manufacturers to deliver the stock quickly and on plant managers to ensure there are no delays. This can have a negative consequence on safety, with the expectation of moving goods quickly, leading to an increased risk of accidents. To ensure a safe just-in-time system, it is important for businesses to follow key processes. M. Sepheri, a JIT expert, published a methodology for businesses to follow. Sepheri considered housekeeping a top priority. He said that they should consider the physical organisation and discipline of their plant and that it should have a compact layout. Firms need to ensure that the steps in getting the product from the factory to the customer are efficient and do not waste any time or resources. A key step in this process is how businesses physically move goods. Traditionally, companies use forklift trucks or high levels of manual labour to move things. However, these methods can make the process a slow and dangerous one that can hinder the JIT methodology. Traditional equipment such as cranes and forklifts are fine for use at the periphery of a factory, but struggle as you get closer to the production lines, where narrower walkways can pose a safety risk to pedestrians. This means that more manual labour is required and is not great if you're trying to roll out a JIT system. Congested walkways also delay workers' movements if they have to wait for their path to clear or for a trained crane or forklift operator to move the product. MasterMover’s range of electric tugs offers complete control and manoeuvrability. According to the Health & Safety Authority, of the 70,000 self-reported non-fatal workplace injuries in 2014 to 2015 in the manufacturing sector, 25% were related to lifting and handling. By using electric tugs controlled by a pedestrian, plant managers can reduce the risk to employees who handle or lift large objects. By positioning the operator in front of, rather than behind, the goods where their vision would be impaired, the operator can see any hazards in their way. This reduces the risk to the employee transporting the goods, any employees in their vicinity and reduces the risk of damage to the goods themselves. Electric tugs can help companies to move their products,and help them maximise the efficiency, speed and safety of their production line, to create an effective just-in-time process. |
|
|
|
Electric tug proves a smart move | 21/11/2014 |
Specialist automotive yarn manufacturer Autofil Worldwide has increased efficiency and improved health and safety since bringing MasterMover’s SmartMover equipment into its Nottingham-based operation
The polyester yarn manufacturer uses advanced equipment and expert knowledge to create high quality specialist yarns that are woven into fabrics – specifically for use within automotive interiors. The creation of these yarns requires specialist treatment using autoclaves; yarns are wheeled on large trollies into the autoclaves for heat treatments to improve the yarns’ attributes.
Mike Fisher, engineering and safety manager at Autofil explains: "Our specialist yarns are used primarily within car seat manufacture, and we pride ourselves on the superb quality of the materials we produce. To achieve our high quality standard, we use autoclaves to apply heat treatment to stabilise and improve yarn attributes for subsequent processes.
"Loading the Autoclaves is a demanding manual task which requires the manoeuvre of heavy industrial trollies,” he adds. "For some time we’ve been looking to improve our loading methods, not only to advance health and safety but to remove the requirement for operatives to actually position themselves inside the autoclave in order to fully insert these heavy trollies.”
Autofil was restricted to positioning three trollies into the autoclave at a time, and was also reliant on manual handling for the entire manoeuvre. In addressing the problem, the company investigated the advantages of MasterMover technology – in particular the SmartMover – an electric tug that is suitable for manoeuvering all types of wheeled loads, safely and effectively.
The design of the SmartMover makes it not only powerful, but operable for pedestrians, allowing users to move both hi-tech vessels and more simple trollies. Its flexible attachment connects safely to wheeled loads, and the variable speed setting and standard auto-stop feature ensure that material handling is always safe and simple, no matter what the industry, or type of load.
Mike Fisher continues: "It didn’t take much convincing to see that the MasterMover SmartMover would be the ideal solution for loading our autoclaves. I’m pleased to say that I’ve had previous experience of using this exact machine and have complete confidence in bringing its robust, easy-to-use technology to the AutoFil shop floor.
"The SmartMover has completely changed, and significantly improved the way we move our yarn trollies both in and out of the autoclaves. Whereas previously we were loading three trollies at a time, we can now load four – increasing efficiency significantly. The machine’s strength also means that operators need no longer manoeuvre themselves within the autoclave to achieve successful loading. This is a terrific improvement and we’re all extremely satisfied.”
Since incorporating Mastermover’s SmartMover for use with loading the factory’s autoclaves, Autofil has purchased a SmartMover for driving its dye pack transporter up and down the dyehouse which was previously pushed manually – another significant health and safety improvement which the operatives are extremely delighted with.
Andy Owen, managing director of MasterMover, comments: "It’s encouraging to hear that the SmartMover is performing so well for Autofil. We strive to create equipment that increases efficiency, reduces the risk of manual handling injuries and betters the process on the shop floor. We understand that AutoFil’s operation team is extremely pleased with the particular SmartMover that’s currently in use and find the news that a second machine is planning to be purchased very welcoming indeed.” |
|
|
|
Airbus uses electric tugs for wing assembly | 08/01/2014 |
Airbus, one of the world’s leading aircraft manufacturers, is using pedestrian electric tugs from MasterMover as an integral part of its wing assembly plant in Broughton. The factory, near Chester, is responsible for manufacturing the wings on nearly all Airbus aircraft, from the company’s popular A320 to its state-of-the-art A350 XWB.
The complex manufacturing and assembly process involved in building a wing requires the fast, safe and effective transportation of components and tooling around the factory.
Wings for the A320 aircraft are currently made using traditional materials like aluminium, but the arrival of the A350 brings with it a move towards carbon fibre composites. In either material, the wing parts are long, awkward to handle and often heavy.
For the past 10 years, MasterMover has supplied models from its MasterTug range as a solution for moving everything from stringers (the lightweight aluminium struts that secure the wing outer skin to the frame) through to complete wings for the A320. As demands on the Broughton operation have grown, so has the role for the MasterTug. Today, the tugs can be found not only moving wing parts but also moving support equipment, including mobile working platforms, production tooling, kitting trolleys and test equipment.
Designed and manufactured by MasterMover using the principle of weight transfer, electric tugs enable a single pedestrian operator to move heavy components with relatively small equipment by generating tractive force from the load itself. As components can be moved in a safe and controlled manner without the need for forklifts or cranes, Airbus is able to organise its assembly layout to suit its specific working practices.
Varying sizes of MasterTug are used at Broughton, from the MT5 capable of moving four tonne loads to the MT20, which can tow up to 15 tonnes. The MasterTugs are used throughout the production process: moving parts from goods in to the production line; transporting sub-assemblies through the machining process; and handling turnover jigs so that production staff can rotate components freely and safely.
Since 2008, 15 MasterTugs have taken their place on the flow-line production system used for final assembly of the A320 wings. A tug is positioned at each assembly stage and together they move the whole production line in unison. This proved to be a cost effective and highly reliable means of benefitting from flow line production techniques, which is exactly what Airbus needed with the rapidly growing demand for the smaller single aisle A320 aircraft. With a new wing completed every 11 hours, the MasterTugs have confirmed their reliability and longevity in a demanding production environment.
The expansion of MasterMover’s involvement at Airbus Broughton has been a continuous process, as Hugh Freer, Sales Director at MasterMover, explains. "As one department begins to use the MasterTug, their neighbours decide it will also be ideal for their purposes, and so on. The initial proposition proves itself very quickly.”
|
|
|
|
Compact & versatile | 02/12/2013 |
Pedestrian electric tugs from MasterMover are providing safe materials handling in the manufacture of the latest generation of vehicles from Leyland Trucks. The use of two SmartMover SM100 models allows heavy pre-assembled modules to be moved by a single operator, freeing up valuable manpower. The SmartMover is a compact, versatile unit capable of moving up to 1,200 kg on castors. When it is coupled to the load, it utilises tractive force to take the weight of the load away from the operator for a comfortable, controlled journey across the factory. |
|
|
|
Transporting sub-components with MasterMover | 26/04/2013 |
MasterMover, provider of worldwide electric tug solutions, believes that its technology offers a solution to the difficulty of achieving fluid assembly line processes in low to medium volume manufacturing sectors. The company’s MasterTug range has already become an integral part of the assembly line for customers in OEM manufacturing industries around the globe. The reason for MasterMover’s success is that, where it is uneconomic to install expensive automation equipment and unsafe to use existing materials handling machines, electric tugs are providing a real cost-effective method of moving the whole product from stage one of the assembly process through to final inspection as well as delivering the components to the process. "The volumes involved in complex, high value manufacturing preclude the possibility of automation; nonetheless, there must still be a fast, efficient assembly process and a way of transporting sub components,” explains Andy Owen, managing director of MasterMover. Historically, manufacturers have been required to reserve a large section of the factory to provide a road network for forklifts to transfer parts to a fixed location, where the product is assembled until complete. As MasterMover points out, this solution is not satisfactory in terms of efficiency. MasterMover’s solution is to use its MasterTug range, which can move parts from one stage to the next on trolleys. Designed and manufactured by MasterMover using the innovation of weight transfer, electric tugs enable customers to move heavy components with relatively small equipment by generating tractive force from the load itself. As a result, a single pedestrian operator can move trolleys in a safe and controlled manner without the need for forklifts or cranes within the factory. This means that the production line can be laid out to an optimum specification, to suit the specific working practices of the product. The long-term cost implications of this are enormous, according to Andy Owen. "In a traditional, fixed manufacturing environment, it is difficult to increase production volumes without building a factory extension to accommodate additional cranes or roadways. With our system, it can be achieved quickly and flexibly, enabling manufacturers to react to short-term boosts in orders. "Furthermore, it enables ambitious manufacturers to develop new products without being forced to commit to long-term capital investment in a dedicated factory layout,” he points out. Amongst the blue-chip names which have used MasterMover electric tugs to improve assembly line efficiency is JCB, where MasterTugs are involved in moving components in the company’s famous Heavy Products division. "MasterMover tugs are bringing a real benefit to our operation, helping us to assemble a range of quality excavators weighing up to 46 tonnes,” explains Poe Meadon, Materials Department at JCB Heavy Products. "The MT20 units are involved in delivering components from the paint shop to the assembly line, as well as moving part-assembled excavators through to final completion. "In addition, when we are building a bespoke model requiring special changes, we will move the assembly off the production line to a special area. Without MasterMover’s assistance this would be a difficult and time-consuming operation, but the use of MasterTugs ensures a smooth and highly efficient process,” he adds. |
|
|