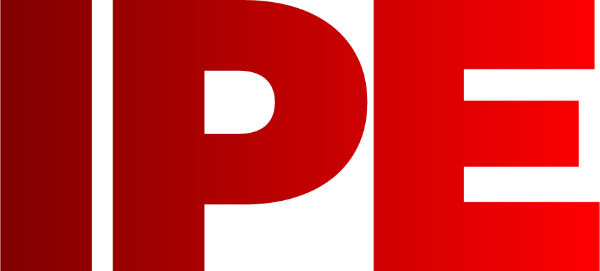
![]() |
Edward Lowton
Editor |
![]() ![]() |
The time is right for food and drink SMEs to invest in automation | 26/07/2017 |
---|---|
Paul Wilkinson, commercial & information systems manager at Pacepacker Services, examines the current challenges of the food and drink industry and details how he believes robots can assist SMEs to boost productivity and compete with larger industry players The adoption of robots in industry has been chequered in the UK. A Centre of Economics and Business Research report* states that the UK had a much smaller rate of adoption than in other developed, industrial countries, at 33 robots per 10,000 employees. In fact, the same report found that the number of new industrial robots installed in 2015 actually dropped 21% from 2014. However, there are signs that UK manufacturers’ attitudes to robots are changing rapidly. Previously robots were seen as the preserve of larger industries, but there is a growing awareness that robots can offer similar productivity benefits to the SMEs that make up the bulk of the UK’s economy. Although prices have remained stable, advances in both software and hardware make today’s robots faster and more powerful, ensuring that they are capable of many more tasks. The food and drink industry in particular can benefit from the adoption of robots. Food and beverage production is becoming more critical to the economy, especially for the export sector. The Food and Drink Federation recently released figures that said the first quarter of 2017 was the largest on record, growing 8.3% year-on-year to £4.9bn, and this follows bumper 2016 figures. The organisation credits the weak pound and better promotion abroad for the increase. In periods of growth like this, companies are more likely to look at capital investment and consider more innovative ways to increase productivity. Robots are likely to be one of the investments that can gain the best yield for the manufacturer. With Brexit on the horizon, there are fears that tariffs may affect this growth, while making it harder to recruit workers for the industry. Oxford University’s Migration Observatory estimates 36% of process workers in the food and drink industry are foreign born, so a recruitment shortage is a real possibility in the near future. Robots can fill this recruitment gap while providing additional benefits to manufacturers. Robots may have an initial capital investment, but provide savings over the longer term by increasing productivity. They also cut out a lot of the paperwork and red tape that can hurt businesses – robots don’t need holidays, pensions or salaries. Technological advances also mean today’s robots can work safely in the same areas as existing staff without the need for additional outlay on protective measures. In the food and beverage industry, robots are mainly found at the back end of the line - bagging, packaging and palletising products. These robots are fast and reliable, making them capable of freeing up manpower to assist elsewhere in the factory. The key to these improvements has been advances in software and hardware, which make robots more flexible and easier to use. For example, there are a wide variety of robotic arm extensions that enable robots to deal with almost any type of container or packaging. Programming can also be done offline, allowing files to be set up beforehand, and quickly downloaded when the process changes and ensuring changeover times are kept to a minimum. One area that has concerned manufacturers in the past, is the disruption caused when initially implementing robots in the production line. This can be minimised by partnering with an integrator with the domain experience, combined with high level engineering, automation, IT and operational skills. There is often tremendous value to be gained from working with companies that have refined their skills by taking on complex and bespoke projects. Having a solid track record of integrating disparate automation platforms is equally valuable, as it enables best practice to be shared between different applications. An integrator with intimate knowledge of the food and drinks industry, such as Pacepacker, can offer advice from the very start of the process on the correct set up, robots, software and even provide tailored training to ensure implementation is painless. For example, Pacepacker and Festo have partnered to deliver training days to customers that can provide answers to any questions and advice on the latest technological advancements. Strong supplier partnerships are equally critical to project success. As testimony, Pacepacker recently sourced equipment from nine different original equipment manufacturers (OEMs) to build its most complex case loading and palletising line to-date. Everything came from British based suppliers, including FANUC, Endoline, Capture Automation, LAC Conveyors and Festo. In total, the line comprised more than 15 individual elements, including a special mechanical end effector designed by Pacepacker that grabs hold of bottles in a single layer. The operation, which previously relied entirely on manual labour, has more than doubled processing and packing output for this client and is also reducing waste and eliminating workforce repetitive strain injuries. Although the UK may have fallen behind the curve in the adoption of robots in industry, this is changing as manufacturers look to increase productivity. SMEs in particular have been reluctant to make the initial outlay on robots, and this is especially true for the food and drink industry. Europe-wide, SMEs with fewer than 249 employees account for more than 50% of the food and drink industry turnover. With Brexit looming, and fears of an upcoming shortage of manpower for the industry, there is no better time to look at automation. Robots are now more powerful and flexible, and assistance is readily at hand to ensure the transition goes without a hitch. |
|
|
|
Robot builder provides career signpost to STEM students | 24/07/2015 |
Fourteen secondary students from two schools in Colchester got the chance to showcase their robotic skills during an open day at Pacepacker Services. During a tour of the Essex-based factory, the students were encouraged to investigate the exciting range of career opportunities that STEM study opens up to them.
With senior people from three of the UK’s top robotic engineering companies in attendance, including Pacepacker’s collaborators – Festo and FANUC – they were able to get a varied perspective on engineering career pathways within the packing industry.
With the global advanced manufacturing market predicted to double in size to £750 billion by 2020, largely driven by developments in robotics and 3D printing, the ability to translate digital design into real-world production are set to be some of the most important skills in the future according to a 2015 report by UKCES. Like many in the sector, Pacepacker is keen to demonstrate the ladders of opportunity and the types of roles that will be in demand.
Pacepacker’s very own award-winning apprentice success story Andrew Lufkin explained to the captive audience why he chose ‘on-the-job’ training with Pacepacker over university fees: "Apprenticeships are an eye opener to the working world. It’s taught me discipline, punctuality, how to prioritise, and accountability.”
Students were also able to quiz graduate and mechanical design engineer, Andrew Westrop, who took the university pathway: He said: "It’s exciting to be part of such an innovative engineering team and I enjoyed sharing my experiences with the students.”
As part of the experience Pacepacker introduced the students to Solidworks software which the company uses to create prototype robot designs. An alternative to CAD software currently used by the students, Solidworks enables designers to be more innovative whilst also applying their STEM skills. Seeing how swiftly the students took to the technology, Pacepacker on the spot agreed to sponsor the first year’s Solidworks license for both school’s robotic groups.
Throughout the day the students were encouraged to get hands on with some of the newest technology, including operating a FANUC robot arm, Festo end effectors (the robot’s hand) and a Pacepacker Blu-Robot (a second-user reconditioned unit).
Commenting on the success of the day, host Dennis Allison, MD of Pacepacker emphasised: "Everything starts with an idea and STEM subjects are used throughout the entire process, from design through to installation. It was a pleasure to see how inquisitive these young students’ minds are and how fast their skills are developing. For a growing company like ours it’s reassuring to see so much fresh engineering talent in the pipeline.”
* https://www.gov.uk/government/uploads/system/uploads/attachment_data/file/439270/150626_AM_SLMI_report.pdf |
|
|
|
Automation equipment with get up and go | 01/05/2014 |
When it comes to handling, moving and lifting bulky products, automation technology today can certainly pack some punch. Once deemed too weighty, fragile and cumbersome to move between production lines, let alone sites, packing machinery is now designed with portability in mind giving manufacturers more versatility than ever before, explains Pacepacker Services
Pacepacker Services has seen a dramatic rise in the demand for bespoke and transportable bagging, pick and place and palletising solutions over the past 18 months. Contrary to popular belief, automation equipment doesn’t need to have a fixed abode. The ability to transport machinery across a factory floor, a field or even a county enables customers, who may have previously ruled out automation due to cost concerns or inflexibility, to boost production in their plants, often with a 12 to 18 month ROI.
Case studies Belmont Farms is a great example. Handling up to 1000t of potatoes each year, Pacepacker created a ‘plug-and-play’ robotic palletising and conveyor system. Measuring 5 x 4m and weighing 2500kg, it was installed within a customised moveable frame that is now easily transportable via a fork lift on a trailer around the 13-mile long family-run farm. This flexibility facilitates expansion opportunities and is beneficial for manufacturers that have numerous packing operations across multiple or single sites.
Full line automation is often perceived as expensive – particularly if you are packing numerous products of varying consistency. Space limitations can also be a barrier that hinders a move to automation. This is something Pacepacker addressed for horse feed manufacturer F H Nash. Rather than doubling the number of systems, they minimised the automation outlay by creating a single bespoke system that toggles between two production lines to handle both dry and wet product.
Taking into account a limited footprint, Pacepacker mounted a C21 Multi-Pile Sack Placer and a Total Bag Control (TBC) bagging system onto sliding rails. Because it was only the TBC moving between lines, Nash was able to use two separate weighing systems to keep the different product consistencies apart, eliminating the risk of contamination. The TBC’s flexibility meant that as the system was moved, product recipes could be called up instantly and downtime eliminated and no matter which position the bagging system was in it fed filled sacks to the same robotic palletiser.
Many of these developments are now possible due to a rise in robotic solutions designed for packing applications. To put this in context, Pacepacker’s portfolio now comprises more than 50 palletising and pick and place robotic options and dozens of different end-effectors, making it much simpler to engineer a bespoke solution to improve product quality, reduce waste and boost throughput.
Working as a FANUC strategic partner, Pacepacker offer ‘new generation’ robots, including the M410-iC/185 palletiser. Reported to be the strongest, fastest and most compact palletiser in its class, it is suitable for restricted areas where headspace is at a premium. The new generation system has been designed with 20% less parts, making it lighter and more portable. Featuring a 185kg payload and average speed of 1700 cycles per hour, it is versatile enough for palletising bags of sugar or shifting slabs of concrete, making it popular with agricultural, food, bulk solids and aggregate manufacturers.
The ability to withstand harsh environments is equally important. Earsham Gravel tasked Pacepacker with creating a portable yet heavy-duty turnkey line, incorporating weighing, bagging and robot palletising technology that could be moved between quarries. The entire line was built into two interconnecting containers measuring 40 x 8 x 8ft. As well as meeting space constraints, the kit was designed to withstand the abrasive and wet quarry environment. Virtually doubling the daily bagging capacity to 140t, it takes just 30 minutes to load the kit onto a lorry and transport to a new location. |
|
|