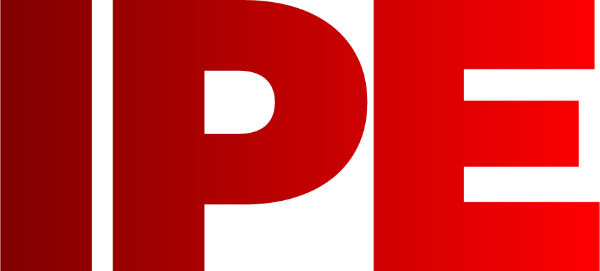
![]() |
Edward Lowton
Editor |
![]() ![]() |
Home> | Plant, Process & Control | >Pumps | >Controlling costs |
ARTICLE
Controlling costs
25 January 2013
Many organisations are striving to reduce operational costs and maintain profitability.Control valves may not at first seem a prime target but, says Mick Phipps of Spirax Sarco, there are real savings to be achieved by spe
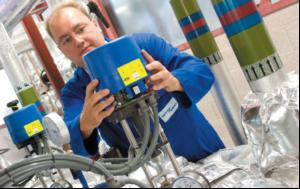
Many organisations are striving to reduce operational costs
and maintain profitability.Control valves may not at first
seem a prime target but, says Mick Phipps of Spirax Sarco,
there are real savings to be achieved by specifying valves
that carry the lowest total cost of ownership (TCO)
Major processing sites often have valve populations running into the thousands. These organisations have well-developed processes for sourcing valves with low running costs to keep their operational expenditure to a minimum.
More modest operations with fewer valves can benefit from a similar approach, making year-on-year maintenance cost savings.
The key lies in the proper sourcing of valves that will give the lowest life cycle cost.
The cost of prematurely shutting down a process to replace a poor quality valve that has failed, will far outweigh any capital costs saved at the time of purchase.
The following criteria serve as a basic guide to purchasing valves with a low total cost of ownership.
Aim to get best value for money. It has been estimated that more than 70% of a control valve's TCO is spent on maintenance. Only 20% is down to the valve's capital cost; the remainder goes on installation. It is vital to buy valves that will give long service life and low maintenance costs as these can far outweigh the lower capital cost of a valve that incurs higher levels of maintenance.
Search out valves that are quick to maintain.
Valves that can be maintained and restored to duty quickly help to limit production delays. Quick replacement of the stem seal, for example, means less downtime and less lost production. Even when maintenance is planned, it is often scheduled during plant shutdowns when maintenance personnel have a heavy workload.Minimising time spent on valves reduces the need for overtime pay or the hiring of third-party contractors.
Points to watch out for when sourcing valves include maintenance that is possible without removing the valve from the line and the ability to replace components without special tools. Look also for selfaligning, clamp-in-place internals. Valves with screw-in components can suffer from the seats seizing in place, requiring the valve to be removed from the pipeline and incurring a lengthy shutdown.
Insist on simple maintenance procedures.
These reduce training costs and help to ensure that any maintenance work done will restore the valve to full operating capability.
Complex maintenance routines carry a higher risk of valves not being re-assembled correctly, potentially reducing performance.
Long maintenance intervals. Buyers of control valves expect several years of reliable life without major maintenance being required, such as replacing the stem seal.
This figure is typically five years, but could be 10 years+, depending on application.
Valves on lines carrying fluids with suspended particles or operating in dusty atmospheres may need maintaining more frequently than valves in less harsh applications. Valves that have design features to minimise the impact of such conditions, for example by including wipers to prevent dust and particles getting into the valve stem, are likely to offer longer service intervals throughout their life. Hard trim materials and a design that diffuses the discharge from the plug and seat and reduces internal flow velocities to minimise internal erosion, further extends valve life.
Ensure it's easy to change the valve's duty.
Occasionally there may be a major change in process parameters that requires new valves, or a process line may shut down completely.
In such situations, control valves that use a modular design carry a cost advantage as they can be reconfigured relatively easily.
This could easily save the cost of purchasing several new valves.Modular valves also help to cut spares stockholding costs.
Consider the less obvious benefits of accurate control, important for the efficient running of any process. Use of positioners to provide precise valve movement contributes to higher productivity and lower energy costs with their environmental benefits, as well as reduced maintenance. Accurate and smooth control tends to reduce the amount of valve movement and wear, as well as decreasing running costs such as compressed air consumption. High quality valves that are well designed using modern design tools such as Computational Fluid Dynamics, can achieve smooth fluid flows under all conditions. Smooth flows lead to reduced internal wear and longer service life.
Good technical support. Take time to look beyond the valve specifications and review the supplier and level of support it provides.
The biggest impact of a poorly chosen valve will be poor process performance, leading to low productivity and poor product quality.
The running costs of a badly specified valve may be excessive too. A valve that is too large for a given duty, for example, will operate more closely to its seat and experience more trim wear. Equally, a valve that is too small may constrict the flow and lead to high velocities, reducing its life. An incorrectly sized and selected valve may also be subject to cavitation and noise in the flow, which can rapidly wear the valve internals. It makes sense to use the vendor's technical expertise to help get it right.
Therefore, pick a vendor that has the inhouse expertise and experience to provide support whenever needed.
Major processing sites often have valve populations running into the thousands. These organisations have well-developed processes for sourcing valves with low running costs to keep their operational expenditure to a minimum.
More modest operations with fewer valves can benefit from a similar approach, making year-on-year maintenance cost savings.
The key lies in the proper sourcing of valves that will give the lowest life cycle cost.
The cost of prematurely shutting down a process to replace a poor quality valve that has failed, will far outweigh any capital costs saved at the time of purchase.
The following criteria serve as a basic guide to purchasing valves with a low total cost of ownership.
Aim to get best value for money. It has been estimated that more than 70% of a control valve's TCO is spent on maintenance. Only 20% is down to the valve's capital cost; the remainder goes on installation. It is vital to buy valves that will give long service life and low maintenance costs as these can far outweigh the lower capital cost of a valve that incurs higher levels of maintenance.
Search out valves that are quick to maintain.
Valves that can be maintained and restored to duty quickly help to limit production delays. Quick replacement of the stem seal, for example, means less downtime and less lost production. Even when maintenance is planned, it is often scheduled during plant shutdowns when maintenance personnel have a heavy workload.Minimising time spent on valves reduces the need for overtime pay or the hiring of third-party contractors.
Points to watch out for when sourcing valves include maintenance that is possible without removing the valve from the line and the ability to replace components without special tools. Look also for selfaligning, clamp-in-place internals. Valves with screw-in components can suffer from the seats seizing in place, requiring the valve to be removed from the pipeline and incurring a lengthy shutdown.
Insist on simple maintenance procedures.
These reduce training costs and help to ensure that any maintenance work done will restore the valve to full operating capability.
Complex maintenance routines carry a higher risk of valves not being re-assembled correctly, potentially reducing performance.
Long maintenance intervals. Buyers of control valves expect several years of reliable life without major maintenance being required, such as replacing the stem seal.
This figure is typically five years, but could be 10 years+, depending on application.
Valves on lines carrying fluids with suspended particles or operating in dusty atmospheres may need maintaining more frequently than valves in less harsh applications. Valves that have design features to minimise the impact of such conditions, for example by including wipers to prevent dust and particles getting into the valve stem, are likely to offer longer service intervals throughout their life. Hard trim materials and a design that diffuses the discharge from the plug and seat and reduces internal flow velocities to minimise internal erosion, further extends valve life.
Ensure it's easy to change the valve's duty.
Occasionally there may be a major change in process parameters that requires new valves, or a process line may shut down completely.
In such situations, control valves that use a modular design carry a cost advantage as they can be reconfigured relatively easily.
This could easily save the cost of purchasing several new valves.Modular valves also help to cut spares stockholding costs.
Consider the less obvious benefits of accurate control, important for the efficient running of any process. Use of positioners to provide precise valve movement contributes to higher productivity and lower energy costs with their environmental benefits, as well as reduced maintenance. Accurate and smooth control tends to reduce the amount of valve movement and wear, as well as decreasing running costs such as compressed air consumption. High quality valves that are well designed using modern design tools such as Computational Fluid Dynamics, can achieve smooth fluid flows under all conditions. Smooth flows lead to reduced internal wear and longer service life.
Good technical support. Take time to look beyond the valve specifications and review the supplier and level of support it provides.
The biggest impact of a poorly chosen valve will be poor process performance, leading to low productivity and poor product quality.
The running costs of a badly specified valve may be excessive too. A valve that is too large for a given duty, for example, will operate more closely to its seat and experience more trim wear. Equally, a valve that is too small may constrict the flow and lead to high velocities, reducing its life. An incorrectly sized and selected valve may also be subject to cavitation and noise in the flow, which can rapidly wear the valve internals. It makes sense to use the vendor's technical expertise to help get it right.
Therefore, pick a vendor that has the inhouse expertise and experience to provide support whenever needed.
MORE FROM THIS COMPANY
- Unsung hero of boiler house efficiency
- Condensate recovery: White paper
- Opportunity to cut costs
- Recovers energy
- Time savings on a plate
- Water heating costs cut
- Boilerhouse guide
- Flash steam emission problems evaporate
- Making sure it's full steam ahead
- Spirax Sarco launches innovative range of insulation jackets
OTHER ARTICLES IN THIS SECTION