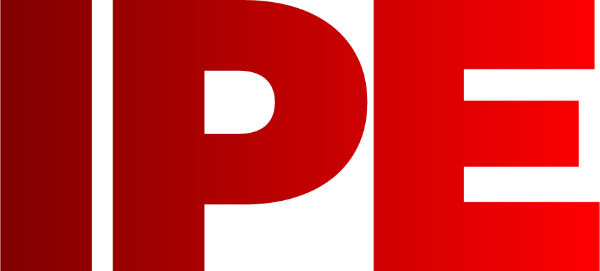
![]() |
Edward Lowton
Editor |
![]() ![]() |
Home> | Handling and Storing | >Labelling, marking and barcoding | >2010 vision |
ARTICLE
2010 vision
25 January 2013
With coding, marking and labelling an essential component of modern production technology, industrial vision-based code readers have an important role to play.Don Braggins of UKIVA explains From processing to packagin
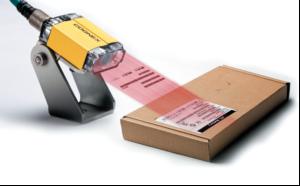
With coding, marking and labelling an essential component
of modern production technology, industrial vision-based
code readers have an important role to play.Don Braggins
of UKIVA explains
From processing to packaging through to warehousing, barcode reading is used in applications as varied as verifying product IDs and automatic picking of products in a warehouse. Correct packaging labelling is critical for consumer safety, especially in the food, beverage, pharmaceutical and medical industries. In addition, 'mark and read' applications are used for product identification and traceability, especially in safety-critical industries such as aerospace and automotive. Coding and labelling usually takes the form of alphanumeric codes, barcodes and the more recently introduced 2D codes.
Vision-based technology Industrial vision code-readers provide an alternative to the more conventional laser scanners. A 1D bar code has a 'check sum' built in so that a laser-scanning type of reader can tell if there is an error in reading it, but can do nothing about it except to say 'unreadable'. A vision system has a better chance of reading a 1D code because if any part of a bar is intact, it can use that information. Vision-based readers tend to be used in circumstances where it is simply not acceptable to receive a 'cannot read - check sum not correct' from a laser scanner. Consider packages coming down a conveyor at constant speed with no facility for offloading those whose code cannot be read.Vision systems are more likely to 'deduce' the meaning of the code, so using a slightly more expensive vision system instead of a laser scanner might avoid the cost of building in a diversion line for packages too difficult to read.
Vision-based code readers fall into two basic categories: Dedicated code readers, both for 1D and 2D code reading, and systems based on industrial cameras. All face the same challenges: Random code or label positioning or orientation, abnormal codes or characters, damage to the code, viewing conditions, interface to the rest of the process, and speed of measurement.
Dedicated vision-based readers Such systems generally feature an integral illumination source and lens and an image of the code is produced using a CCD sensor.
Available in fixed mount and handheld versions, they feature onboard software to process the image and read the code.
For 1D code readers, the challenge is in developing robust reading algorithms that produce reliable results even under non-ideal conditions such as those illustrated. 1D codes are less robust than 2D codes and visionbased readers are more effective than laser scanners in reading low contrast or damaged codes or those distorted by severe perspective.
Reading algorithms have been developed which can handle extreme variations in contrast, blur, damage, voids, specularity, resolution, quiet zone violations (which can occur when codes are printed close to the edge of a label) and perspective distortion.
Since these readers generate an actual image of the code, it is possible to archive images of read failures and download them to a PC to diagnose the root cause of a problem. The performance of individual readers varies from manufacturer to manufacturer, but in addition to their capability to read challenging codes, consideration should be given to the speed at which printed codes can be read. Some readers offer the flexibility to upgrade software for 2D code reading. Readers are available with a variety of interfaces, such as Ethernet/IP and USB, which is important for control, data transfer and integration.
Complete vision systems A high degree of code reading flexibility is offered by using a fully functional industrial vision system equipped with code reading and optical character recognition software.
These differ from the dedicated code readers in that they feature a full camera and lens, often with an external illumination source.
Images of the code are recorded for subsequent processing and measurement.
There are a number of options. The camera may be connected to a PC where the processing is carried out, or smart cameras can be used. These self-contained, standalone vision systems have built-in image processing capabilities. A third option is the compact vision system, where all processing power is contained in a DIN mountable enclosure. This lets multiple cameras be connected to a single processing unit. A key benefit of these powerful vision systems is their flexibility, since they can carry out a host of inspection tasks as well as reading the code.Overview capabilities include checking that the proper label is on the package, that the label is correctly positioned and that the placement angle is within set limits, as well as looking for consistency in colours and logo positioning for brand image purposes. Software can also check for flags, tears and missing parts of the label as well as for defects such as smears, contamination and splatters.With a wide choice of camera types and connectivity standards available, industrial vision systems can be chosen for a huge range of industrial environments.
The author thanks UKIVA members Alrad Imaging, Cognex UK and Stemmer Imaging for their contributions to this article.
From processing to packaging through to warehousing, barcode reading is used in applications as varied as verifying product IDs and automatic picking of products in a warehouse. Correct packaging labelling is critical for consumer safety, especially in the food, beverage, pharmaceutical and medical industries. In addition, 'mark and read' applications are used for product identification and traceability, especially in safety-critical industries such as aerospace and automotive. Coding and labelling usually takes the form of alphanumeric codes, barcodes and the more recently introduced 2D codes.
Vision-based technology Industrial vision code-readers provide an alternative to the more conventional laser scanners. A 1D bar code has a 'check sum' built in so that a laser-scanning type of reader can tell if there is an error in reading it, but can do nothing about it except to say 'unreadable'. A vision system has a better chance of reading a 1D code because if any part of a bar is intact, it can use that information. Vision-based readers tend to be used in circumstances where it is simply not acceptable to receive a 'cannot read - check sum not correct' from a laser scanner. Consider packages coming down a conveyor at constant speed with no facility for offloading those whose code cannot be read.Vision systems are more likely to 'deduce' the meaning of the code, so using a slightly more expensive vision system instead of a laser scanner might avoid the cost of building in a diversion line for packages too difficult to read.
Vision-based code readers fall into two basic categories: Dedicated code readers, both for 1D and 2D code reading, and systems based on industrial cameras. All face the same challenges: Random code or label positioning or orientation, abnormal codes or characters, damage to the code, viewing conditions, interface to the rest of the process, and speed of measurement.
Dedicated vision-based readers Such systems generally feature an integral illumination source and lens and an image of the code is produced using a CCD sensor.
Available in fixed mount and handheld versions, they feature onboard software to process the image and read the code.
For 1D code readers, the challenge is in developing robust reading algorithms that produce reliable results even under non-ideal conditions such as those illustrated. 1D codes are less robust than 2D codes and visionbased readers are more effective than laser scanners in reading low contrast or damaged codes or those distorted by severe perspective.
Reading algorithms have been developed which can handle extreme variations in contrast, blur, damage, voids, specularity, resolution, quiet zone violations (which can occur when codes are printed close to the edge of a label) and perspective distortion.
Since these readers generate an actual image of the code, it is possible to archive images of read failures and download them to a PC to diagnose the root cause of a problem. The performance of individual readers varies from manufacturer to manufacturer, but in addition to their capability to read challenging codes, consideration should be given to the speed at which printed codes can be read. Some readers offer the flexibility to upgrade software for 2D code reading. Readers are available with a variety of interfaces, such as Ethernet/IP and USB, which is important for control, data transfer and integration.
Complete vision systems A high degree of code reading flexibility is offered by using a fully functional industrial vision system equipped with code reading and optical character recognition software.
These differ from the dedicated code readers in that they feature a full camera and lens, often with an external illumination source.
Images of the code are recorded for subsequent processing and measurement.
There are a number of options. The camera may be connected to a PC where the processing is carried out, or smart cameras can be used. These self-contained, standalone vision systems have built-in image processing capabilities. A third option is the compact vision system, where all processing power is contained in a DIN mountable enclosure. This lets multiple cameras be connected to a single processing unit. A key benefit of these powerful vision systems is their flexibility, since they can carry out a host of inspection tasks as well as reading the code.Overview capabilities include checking that the proper label is on the package, that the label is correctly positioned and that the placement angle is within set limits, as well as looking for consistency in colours and logo positioning for brand image purposes. Software can also check for flags, tears and missing parts of the label as well as for defects such as smears, contamination and splatters.With a wide choice of camera types and connectivity standards available, industrial vision systems can be chosen for a huge range of industrial environments.
The author thanks UKIVA members Alrad Imaging, Cognex UK and Stemmer Imaging for their contributions to this article.
MORE FROM THIS COMPANY
OTHER ARTICLES IN THIS SECTION