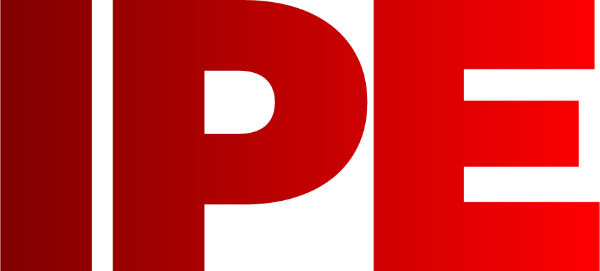
![]() |
Edward Lowton
Editor |
![]() ![]() |
Home> | Premises management/maintenance | >Loading bay equipment | >Planning is key to loading success |
ARTICLE
Planning is key to loading success
25 January 2013
There are many factors to consider when planning a loading bay. Here,Glyn Ansen, national accounts manager for Hörmann UK, details recent projects that demonstrate the benefits of a 'solutions-driven' approach The pri
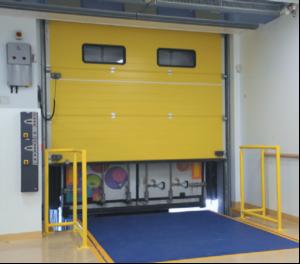
There are many factors to consider when planning a
loading bay. Here,Glyn Ansen, national accounts manager
for Hörmann UK, details recent projects that demonstrate
the benefits of a 'solutions-driven' approach
The primary consideration is the type and sizes of vehicles that are likely to be operated, not just the current fleet.
The site geography has then to be considered in relation to vehicle movements and any slope towards the loading area.
Once the basic layout is considered, the finer detail can be established. The type of mechanical handling equipment employed and the operating environment are critical factors in the overall design.We must then consider the type and size of seal, dock leveller and door required before looking at the control system and ancillary equipment.
Hörmann is one of the companies that offers a one-stop-shop service. It is involved in all aspects from initial design to onsite installation, offering advice to ensure the final solution meets the operational and budgetary needs.
For the Royal Mail distribution centre at Swan Valley, Northampton, Hörmann worked closely with the main contractor Winvic to project manage the installation of 23 loading bays with heavy duty dock levellers, dock shelters, sectional insulated loading bay doors, high speed bi-parting doors and high security doors.
The high specification of the build required considerable attention to detail Hörmann, and non-standard heavy duty dock levellers and dock shelters were engineered for the project.
Hörmann FR type heavy duty 8000Kg rated load dock levellers were installed with a custom 600mm telescopic lip while the dock shelters also had to be designed to accommodate the wide range of vehicles operated by the Royal Mail. By incorporating an inflatable head and standard curtain sides Hörmann produced a solution that gives an efficient seal in all circumstances.
This attention to detail can also be seen at Teva Pharmaceuticals in Eastbourne where Hörmann has installed its new DOBO system that allows trucks to dock on the loading bay before opening their doors (pictured below). This improves both security and helps maintain a clean environment.
In conjunction with the DOBO system this was also the first UK installation of the Hörmann docking assistant that helps drivers dock in the optimum position. The docking assistant operates via proximity sensors in the loading bay door linked to traffic lights that guide the driver into position.
Once the truck is on the dock the inflatable dock seals surround the vehicle on three sides. The vehicle is now docked with both the loading bay door and the truck doors still closed. The truck doors can then be unlocked and opened in to the recess designed into the bay area. To accommodate the door opening the 6t capacity dock leveller is angled downwards in a below dock position. Once the truck doors have been opened the 1000mm telescopic lip of the dock leveller can be positioned and the truck can be unloaded or loaded as required.
Another example of early involvement is the development of High Speed Spiral Doors to meet a demanding brief from Asda at its Didcot warehouse. In a conventional loading environment Asda approached Hörmann to provide loading bay and door solutions to meet its goals of minimising energy usage, in line with their commitment towards the environment, while increasing operational efficiency and maintaining high levels of safety.
For the level access doors Hörmann developed a single high speed, insulated spiral door to replace a traditional two door solution comprising high speed curtain door for daytime use and sectional outer door for night-time security.
The Hörmann high speed spiral door gives efficient thermal insulation, reducing heat loss and affording the high levels of security needed. The non-contact guided roll-up technology allows these doors to operate at high speed with minimal wear leading to long service life. These factors, coupled to Hörmann's precision engineering, combine to give the efficient operation needed with on-going cost savings while reducing overall environmental impact.
The above examples are all solutiondriven.
They have involved design and engineering input from Hörmann's project teams at an early stage, resulting in efficient solutions that meet individual needs.
The primary consideration is the type and sizes of vehicles that are likely to be operated, not just the current fleet.
The site geography has then to be considered in relation to vehicle movements and any slope towards the loading area.
Once the basic layout is considered, the finer detail can be established. The type of mechanical handling equipment employed and the operating environment are critical factors in the overall design.We must then consider the type and size of seal, dock leveller and door required before looking at the control system and ancillary equipment.
Hörmann is one of the companies that offers a one-stop-shop service. It is involved in all aspects from initial design to onsite installation, offering advice to ensure the final solution meets the operational and budgetary needs.
For the Royal Mail distribution centre at Swan Valley, Northampton, Hörmann worked closely with the main contractor Winvic to project manage the installation of 23 loading bays with heavy duty dock levellers, dock shelters, sectional insulated loading bay doors, high speed bi-parting doors and high security doors.
The high specification of the build required considerable attention to detail Hörmann, and non-standard heavy duty dock levellers and dock shelters were engineered for the project.
Hörmann FR type heavy duty 8000Kg rated load dock levellers were installed with a custom 600mm telescopic lip while the dock shelters also had to be designed to accommodate the wide range of vehicles operated by the Royal Mail. By incorporating an inflatable head and standard curtain sides Hörmann produced a solution that gives an efficient seal in all circumstances.
This attention to detail can also be seen at Teva Pharmaceuticals in Eastbourne where Hörmann has installed its new DOBO system that allows trucks to dock on the loading bay before opening their doors (pictured below). This improves both security and helps maintain a clean environment.
In conjunction with the DOBO system this was also the first UK installation of the Hörmann docking assistant that helps drivers dock in the optimum position. The docking assistant operates via proximity sensors in the loading bay door linked to traffic lights that guide the driver into position.
Once the truck is on the dock the inflatable dock seals surround the vehicle on three sides. The vehicle is now docked with both the loading bay door and the truck doors still closed. The truck doors can then be unlocked and opened in to the recess designed into the bay area. To accommodate the door opening the 6t capacity dock leveller is angled downwards in a below dock position. Once the truck doors have been opened the 1000mm telescopic lip of the dock leveller can be positioned and the truck can be unloaded or loaded as required.
Another example of early involvement is the development of High Speed Spiral Doors to meet a demanding brief from Asda at its Didcot warehouse. In a conventional loading environment Asda approached Hörmann to provide loading bay and door solutions to meet its goals of minimising energy usage, in line with their commitment towards the environment, while increasing operational efficiency and maintaining high levels of safety.
For the level access doors Hörmann developed a single high speed, insulated spiral door to replace a traditional two door solution comprising high speed curtain door for daytime use and sectional outer door for night-time security.
The Hörmann high speed spiral door gives efficient thermal insulation, reducing heat loss and affording the high levels of security needed. The non-contact guided roll-up technology allows these doors to operate at high speed with minimal wear leading to long service life. These factors, coupled to Hörmann's precision engineering, combine to give the efficient operation needed with on-going cost savings while reducing overall environmental impact.
The above examples are all solutiondriven.
They have involved design and engineering input from Hörmann's project teams at an early stage, resulting in efficient solutions that meet individual needs.
MORE FROM THIS COMPANY
- Hörmann promotes multi-brand servicing at Maintec
- Fast turnaround modification service
- Lock around the dock
- Winter checks
- Proactive loading bay servicing and maintenance
- UK debut for docking system
- Pre-winter check
- Hörmann's roll call
- Hörmann industrial sliding gates improve site security
- Designed to handle double & single deck semi-trailers
RELATED ARTICLES
OTHER ARTICLES IN THIS SECTION