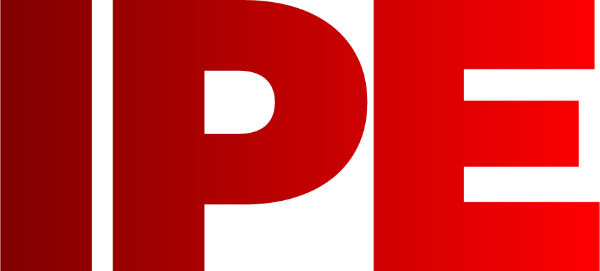
![]() |
Edward Lowton
Editor |
![]() ![]() |
ARTICLE
Plant reliability: key to profitability
25 January 2013
In the fourth and final part of its series Going beyond the repairable asset, ERIKS outlines how plant reliability is key to achieving profitability in manufacturing, processing and distribution businesses.
In the fourth and final part of its series Going beyond the repairable asset, ERIKS outlines how plant reliability is key to achieving profitability in manufacturing, processing and distribution businesses.
This is viewed as so important by leading MRO product and service supply specialist ERIKS that the company has started a campaign to help UK industry improve its performance in this area.
Although most engineers will agree that the reliability of machinery and process systems is crucial, not all appreciate the real impact that component failure or inefficient operation due to machine malfunctions or incorrect setup can have on a company�s productivity and profitability.
This statement is based on ERIKS� experience as a long standing manufacturer of sealing and bearing products, and through knowledge gained in providing maintenance and condition monitoring services to many different customers; these services include vibration and oil analysis, air leak surveys, thermographic surveys, live bearing monitoring, structural inspections, fatigue testing and electrical power testing.
Further evidence is provided via ERIKS� nationwide network of repair and engineering workshops, which specialise in the repair of all aspects of physical plant, from servo-based automation systems and control electronics, through power transmission components to large scale water utility and power generation equipment.
The feedback from workshop engineers is that parts often need replacing long before they reach the end of their predicted operating life. This can be for many different reasons but common throughout is the need to maintain best practice in terms of prevention, training in the latest equipment and the development of techniques to boost reliability and hence profitability.
It can often be the most unexpected issues that create problems. For example, an acidic thumbprint on the inside of a high-speed bearing race can cause it to fail in a fraction of its expected service life; similarly, over-tightening the retaining ring on a mechanical seal by just a few Newton meters can cause a complete process line to grind to a halt.
Every instance of a component failure doesn�t, of course, always lead to an emergency breakdown that stops a plant and costs tens of thousands of pounds per day in lost production; although this does happen more often than you�d think according to ERIKS� engineers.
The real and often hidden cost of reliability is in absorbing the fluctuations in output efficiency and thus production volumes caused by routine maintenance and scheduled repair work. This is where techniques such as predictive maintenance, which enable engineers to make informed decisions, can make a significant difference.
Predictive Maintenance
Moving from reactive to predictive maintenance not only decreases the downtime of production plant but can also increase the quality of output processes or products. In fact, effective predictive maintenance can help increase the productivity of a production line by as much as 10-15%.
This process can be used to determine when an asset is likely to fail - by assessing temperature, vibration, ultrasonics and electrical supply � and can provide engineers with the data that allows them to suggest process improvements that delay or prevent a failure from occurring, and also to cut costs by identifying wastage and inefficiencies.
Using the latest test and monitoring equipment while plant is in operation, maintenance service engineers can conduct assessments of the condition of plant and equipment without having an impact on production.
Experienced specialists can then suggest the most effective methods of maintaining plant productivity � for example, with a comprehensive plant management programme - provide maintenance management systems, and even supply extra resources for larger projects.
Where to start
Once it is recognised that reliability, or lack thereof, can have a profound influence on production operations, maintenance teams need to start looking in a number of areas to make improvements.
Achievement of productivity and profitability goals is a process unique to a site and one which will need to be fine tuned for success, but here�s how to start the process:
- The first step is consultation: reviewing existing high risk, performance critical areas to identify and prioritise savings or improvement opportunities.
- This may include plant surveys and reference to data from production software systems such as SCADA or MES, with downtime or OEE modules that have highlighted problem areas in past.
- Next ask internal and external suppliers to make recommendations, highlighting solutions and providing estimates on savings.
- Prioritise suggestions into short and medium term categories for implementation.
- Use the priority list as a working, agreed action plan, incorporating work schedules, milestones and completion dates.
Consider any ongoing test and analysis or management techniques that might not already be in use; ranging from reliability review meetings to best practice advice and asset management studies.
Cost Justification
When taking proactive measures to improve plant reliability, every production and maintenance manager faces the reality that different approaches to maintenance carry various levels of cost; these cost differences also reflect the level of risk a business carries if maintenance tasks are not completed to satisfactory standards.
Cost has to be balanced against returns; once work is completed it is important that cost savings analyses are carried out and followed through to ensure that improvements are long lasting and that knowledge is retained.
Looking at it from another perspective, good reliability also prevents lost production, product recalls, lower than required output rates, accidents and environmental issues, all of which can arise from poorly managed maintenance and add substantial costs to the bottom line.
Many manufacturing companies spend more maintenance budget on labour, workshop facilities and energy than they do on the components used in completing repairs. So, rather than focusing purchasing efforts on driving down the cost of component parts � in itself a potentially dangerous practice if it affects quality - it makes sense instead to concentrate on implementing improvements in overall plant reliability as this can lead to real savings in the entire operation and maintenance budget.
ERIKS Reliability Services comprises a dedicated team of maintenance service professionals drawn from various core competence centres across the ERIKS Group. The team�s task is to help customers increase the resilience of their production operations by offering products and services that improve reliability, demonstrate savings and boost profitability.
This is viewed as so important by leading MRO product and service supply specialist ERIKS that the company has started a campaign to help UK industry improve its performance in this area.
Although most engineers will agree that the reliability of machinery and process systems is crucial, not all appreciate the real impact that component failure or inefficient operation due to machine malfunctions or incorrect setup can have on a company�s productivity and profitability.
This statement is based on ERIKS� experience as a long standing manufacturer of sealing and bearing products, and through knowledge gained in providing maintenance and condition monitoring services to many different customers; these services include vibration and oil analysis, air leak surveys, thermographic surveys, live bearing monitoring, structural inspections, fatigue testing and electrical power testing.
Further evidence is provided via ERIKS� nationwide network of repair and engineering workshops, which specialise in the repair of all aspects of physical plant, from servo-based automation systems and control electronics, through power transmission components to large scale water utility and power generation equipment.
The feedback from workshop engineers is that parts often need replacing long before they reach the end of their predicted operating life. This can be for many different reasons but common throughout is the need to maintain best practice in terms of prevention, training in the latest equipment and the development of techniques to boost reliability and hence profitability.
It can often be the most unexpected issues that create problems. For example, an acidic thumbprint on the inside of a high-speed bearing race can cause it to fail in a fraction of its expected service life; similarly, over-tightening the retaining ring on a mechanical seal by just a few Newton meters can cause a complete process line to grind to a halt.
Every instance of a component failure doesn�t, of course, always lead to an emergency breakdown that stops a plant and costs tens of thousands of pounds per day in lost production; although this does happen more often than you�d think according to ERIKS� engineers.
The real and often hidden cost of reliability is in absorbing the fluctuations in output efficiency and thus production volumes caused by routine maintenance and scheduled repair work. This is where techniques such as predictive maintenance, which enable engineers to make informed decisions, can make a significant difference.
Predictive Maintenance
Moving from reactive to predictive maintenance not only decreases the downtime of production plant but can also increase the quality of output processes or products. In fact, effective predictive maintenance can help increase the productivity of a production line by as much as 10-15%.
This process can be used to determine when an asset is likely to fail - by assessing temperature, vibration, ultrasonics and electrical supply � and can provide engineers with the data that allows them to suggest process improvements that delay or prevent a failure from occurring, and also to cut costs by identifying wastage and inefficiencies.
Using the latest test and monitoring equipment while plant is in operation, maintenance service engineers can conduct assessments of the condition of plant and equipment without having an impact on production.
Experienced specialists can then suggest the most effective methods of maintaining plant productivity � for example, with a comprehensive plant management programme - provide maintenance management systems, and even supply extra resources for larger projects.
Where to start
Once it is recognised that reliability, or lack thereof, can have a profound influence on production operations, maintenance teams need to start looking in a number of areas to make improvements.
Achievement of productivity and profitability goals is a process unique to a site and one which will need to be fine tuned for success, but here�s how to start the process:
- The first step is consultation: reviewing existing high risk, performance critical areas to identify and prioritise savings or improvement opportunities.
- This may include plant surveys and reference to data from production software systems such as SCADA or MES, with downtime or OEE modules that have highlighted problem areas in past.
- Next ask internal and external suppliers to make recommendations, highlighting solutions and providing estimates on savings.
- Prioritise suggestions into short and medium term categories for implementation.
- Use the priority list as a working, agreed action plan, incorporating work schedules, milestones and completion dates.
Consider any ongoing test and analysis or management techniques that might not already be in use; ranging from reliability review meetings to best practice advice and asset management studies.
Cost Justification
When taking proactive measures to improve plant reliability, every production and maintenance manager faces the reality that different approaches to maintenance carry various levels of cost; these cost differences also reflect the level of risk a business carries if maintenance tasks are not completed to satisfactory standards.
Cost has to be balanced against returns; once work is completed it is important that cost savings analyses are carried out and followed through to ensure that improvements are long lasting and that knowledge is retained.
Looking at it from another perspective, good reliability also prevents lost production, product recalls, lower than required output rates, accidents and environmental issues, all of which can arise from poorly managed maintenance and add substantial costs to the bottom line.
Many manufacturing companies spend more maintenance budget on labour, workshop facilities and energy than they do on the components used in completing repairs. So, rather than focusing purchasing efforts on driving down the cost of component parts � in itself a potentially dangerous practice if it affects quality - it makes sense instead to concentrate on implementing improvements in overall plant reliability as this can lead to real savings in the entire operation and maintenance budget.
ERIKS Reliability Services comprises a dedicated team of maintenance service professionals drawn from various core competence centres across the ERIKS Group. The team�s task is to help customers increase the resilience of their production operations by offering products and services that improve reliability, demonstrate savings and boost profitability.
MORE FROM THIS COMPANY
- ERIKS launch new Automation Services Division in the UK
- Strategic partnership announced
- Seals for tough tasks
- ERIKS launches beginners guide to MRO stores outsourcing
- ERIKS expertise secures safe repairs in Thames River Tunnel
- Drives:Repair or replace?
- Prepare pumps for winter
- Revolutionising the MRO Supply Chain
- Going beyond the repairable asset part #2
- Looking at the bigger picture
RELATED ARTICLES
- No related articles listed
OTHER ARTICLES IN THIS SECTION