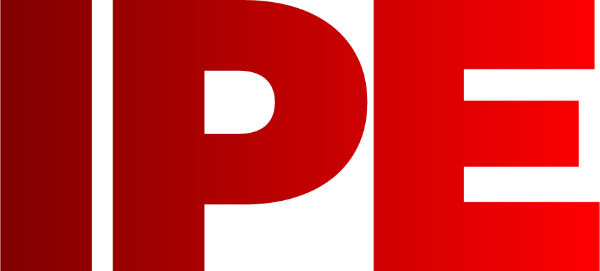
![]() |
Edward Lowton
Editor |
![]() ![]() |
Home> | Production Engineering | >Automation | >Robot swap aids production |
ARTICLE
Robot swap aids production
25 January 2013
As part of a major investment by Norgren at its Lichfield manufacturing site, Kawasaki Robotics has replaced two ageing robots with two Kawasaki RS06L robots. The new additions allow faster cell tool change times and
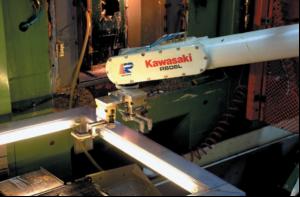
As part of a major
investment by Norgren at its
Lichfield manufacturing site,
Kawasaki Robotics has
replaced two ageing robots
with two Kawasaki RS06L
robots. The new additions
allow faster cell tool change
times and are able to work
more comfortably within
target cycle times.
Installed over 13 years ago the original Kawasaki robots, operate between 5 to 7 days a week and three shifts a day in Norgren's automotive/truck air-brake fittings section.
The new Kawasaki RS robots load and unload brass fittings to two rotary transfer machines which have been moved to new bays in the plant. Cells are programmed to produce up to 100 variants of fitting in batches.
Brass stampings enter the cell, randomly positioned, on a conveyor belt. A vision camera over the conveyor belt pick up point, illuminated by a structured light source, provides the robot with co-ordinates to pick the component correctly. The robot has a double gripper and moves to the transfer machine load point, removes a finished machined fitting and loads the un-machined fitting. The machine cycle takes 6sec.
Mark Clark, manufacturing engineer at Norgren, says: "The new robots are quicker; they work well within the machine cycle time and present the part to the machine before its cycle is finished." The old robots had shorter reach so had to be moved, on a slide fixture, away from the transfer machine to facilitate tool setup, which slowed tool changes. This isn't necessary now as the new Kawasaki RS06L has a longer reach.
Installed over 13 years ago the original Kawasaki robots, operate between 5 to 7 days a week and three shifts a day in Norgren's automotive/truck air-brake fittings section.
The new Kawasaki RS robots load and unload brass fittings to two rotary transfer machines which have been moved to new bays in the plant. Cells are programmed to produce up to 100 variants of fitting in batches.
Brass stampings enter the cell, randomly positioned, on a conveyor belt. A vision camera over the conveyor belt pick up point, illuminated by a structured light source, provides the robot with co-ordinates to pick the component correctly. The robot has a double gripper and moves to the transfer machine load point, removes a finished machined fitting and loads the un-machined fitting. The machine cycle takes 6sec.
Mark Clark, manufacturing engineer at Norgren, says: "The new robots are quicker; they work well within the machine cycle time and present the part to the machine before its cycle is finished." The old robots had shorter reach so had to be moved, on a slide fixture, away from the transfer machine to facilitate tool setup, which slowed tool changes. This isn't necessary now as the new Kawasaki RS06L has a longer reach.
MORE FROM THIS COMPANY
- Heavy duty workhorse joins robot line-up
- Robot at MACH
- Glass expert sees clear advantages with Kawasaki robots
- Multi-million cycle robot replaced after almost 20 years
- Compact robotic welding cell
- Celebrating 20 years in the UK with 700kg addition to palletiser range.
- Supplier award
- £750K investment pulls chair base production back to the UK
- Speedy spot welding robot
- Robots for moulding & post-moulding processes
RELATED ARTICLES
OTHER ARTICLES IN THIS SECTION