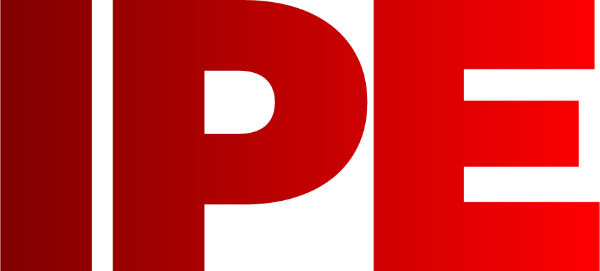
![]() |
Edward Lowton
Editor |
![]() ![]() |
ARTICLE
DSM: The need for best practice
04 March 2013
The way we use electricity is changing and businesses across the country are increasingly focusing on optimising energy use and decreasing their carbon footprint. One way to achieve each of these objectives is by participating in demand side management (DSM), as Marina Hod, market development director at KiWi Power explains
The way we use electricity is changing and businesses
across the country are increasingly focusing on optimising
energy use and decreasing their carbon footprint. One way
to achieve each of these objectives is by participating in
demand side management (DSM), as Marina Hod, market
development director at KiWi Power explains
DSM enables businesses to reduce their consumption from the grid at peak demand times and get paid by National Grid for doing so. In this way, companies can earn a significant recurring revenue stream, gain visibility into their real time energy use, improve emergency preparedness and decrease their carbon footprint. In order to obtain optimum value from working with demand response aggregators there are a number of best practices that should be considered.
Optimise your generator Typically, a standby generator provides electricity for a site in instances when a mains supply has failed. These assets are rarely used due to historically high levels of grid reliability.
Like a car engine, generators require frequent use to keep them working efficiently. To ensure emergency preparedness, it is recommended that generators are run at least once a month.
Generators are often tested 'off-load', which can cause poor combustion, soot formation, clogging of injector rings and unburnt fuel creating oil contamination.
Demand response allows standby generators to be tested 'on-load' and at no cost, making it a useful way to prove engine resilience and optimise performance. Generators are most valuable in demand response programmes where they are able to synchronise with the mains grid supply because they can support significant site electrical loads.
Lister Hospital is an acute NHS-run hospital in Hertfordshire that is currently participating in a demand response programme. To ensure the hospital has a reliable standby power solution in the event of a power failure, it installed new on-site generators and duplicate electricity feed. The generators enable the hospital to take part in a demand response programme, which will help save money on utility bills and create a new revenue stream.
KiWi Power installed four 2MVA, LV diesel generators, which provide full backup for the new 5MVA, duplicate 11kV feed from UK Power Networks. It also implemented a system for controlling these generators remotely from its control centre in London, and integrated this with the hospital's SCADA and PLC systems. KiWi Power can now monitor the status of all four generators at all times and inform the hospital's facilities managers should any problems arise.
Technical audit Working with site staff to understand the normal operating conditions of the facility is key to implementing a successful demand response programme. A technical audit may be conducted free of charge in order to understand the site's operations and create a bespoke demand management strategy (DMS).
Typically, a DMS encompasses non-critical and non-essential systems such as HVAC (heating, ventilation, and air conditioning), lighting, certain manufacturing processes, refrigeration plants and backup generators.
Where possible, DMS should be automated to minimise non-performance risk, using industry standard control and monitoring systems. Automation helps simplify participation and minimises resource requirement from sites. Automation also allows DMS to be initiated remotely and operations to be returned to normal after a demand response event.
An existing 2MW generator was identified for a demand response programme at a large steel facility in Scunthorpe and benefited from a thorough technical site audit and survey report. A testing, commissioning and training programme was implemented, which allowed a technical and commercial proposal to be submitted to the steel company's management team.
Stakeholder management There are often multiple stakeholders within an organisation who must first be consulted when discussing the benefits of a demand response programme. These may include a finance director, facilities/sustainability/ energy managers, engineers and procurement departments. Achieving stakeholder buy-in can be challenging, particularly with businesses spread across multiple sites, where each one may be autonomous and have individual operational requirements.
Sainsbury's is an example of a company overcoming such challenges. While a central coordinator leads the supermarket's participation internally, each site has a bespoke demand reduction strategy and has the final decision on how much demand response to take up. Sainsbury's opted for a pilot scheme in two of its distribution centres. The success of this has led to a full roll out of demand response to the rest of its distribution centres. The next step may be to introduce demand response at store level.
Conclusion Working with a demand response aggregator, such as KiWi Power, can help ensure that businesses realise the full value of demand response participation. Following best practices, such as those highlighted above, and use of the latest technology, aggregators are able to help unlock revenues from various types of demand response programmes currently available. Nonessential services and processes can be identified to allow participation in demand response through comprehensive energy audits and by using existing or new standby power generation assets to provide optimum operational efficiency and performance.
DSM enables businesses to reduce their consumption from the grid at peak demand times and get paid by National Grid for doing so. In this way, companies can earn a significant recurring revenue stream, gain visibility into their real time energy use, improve emergency preparedness and decrease their carbon footprint. In order to obtain optimum value from working with demand response aggregators there are a number of best practices that should be considered.
Optimise your generator Typically, a standby generator provides electricity for a site in instances when a mains supply has failed. These assets are rarely used due to historically high levels of grid reliability.
Like a car engine, generators require frequent use to keep them working efficiently. To ensure emergency preparedness, it is recommended that generators are run at least once a month.
Generators are often tested 'off-load', which can cause poor combustion, soot formation, clogging of injector rings and unburnt fuel creating oil contamination.
Demand response allows standby generators to be tested 'on-load' and at no cost, making it a useful way to prove engine resilience and optimise performance. Generators are most valuable in demand response programmes where they are able to synchronise with the mains grid supply because they can support significant site electrical loads.
Lister Hospital is an acute NHS-run hospital in Hertfordshire that is currently participating in a demand response programme. To ensure the hospital has a reliable standby power solution in the event of a power failure, it installed new on-site generators and duplicate electricity feed. The generators enable the hospital to take part in a demand response programme, which will help save money on utility bills and create a new revenue stream.
KiWi Power installed four 2MVA, LV diesel generators, which provide full backup for the new 5MVA, duplicate 11kV feed from UK Power Networks. It also implemented a system for controlling these generators remotely from its control centre in London, and integrated this with the hospital's SCADA and PLC systems. KiWi Power can now monitor the status of all four generators at all times and inform the hospital's facilities managers should any problems arise.
Technical audit Working with site staff to understand the normal operating conditions of the facility is key to implementing a successful demand response programme. A technical audit may be conducted free of charge in order to understand the site's operations and create a bespoke demand management strategy (DMS).
Typically, a DMS encompasses non-critical and non-essential systems such as HVAC (heating, ventilation, and air conditioning), lighting, certain manufacturing processes, refrigeration plants and backup generators.
Where possible, DMS should be automated to minimise non-performance risk, using industry standard control and monitoring systems. Automation helps simplify participation and minimises resource requirement from sites. Automation also allows DMS to be initiated remotely and operations to be returned to normal after a demand response event.
An existing 2MW generator was identified for a demand response programme at a large steel facility in Scunthorpe and benefited from a thorough technical site audit and survey report. A testing, commissioning and training programme was implemented, which allowed a technical and commercial proposal to be submitted to the steel company's management team.
Stakeholder management There are often multiple stakeholders within an organisation who must first be consulted when discussing the benefits of a demand response programme. These may include a finance director, facilities/sustainability/ energy managers, engineers and procurement departments. Achieving stakeholder buy-in can be challenging, particularly with businesses spread across multiple sites, where each one may be autonomous and have individual operational requirements.
Sainsbury's is an example of a company overcoming such challenges. While a central coordinator leads the supermarket's participation internally, each site has a bespoke demand reduction strategy and has the final decision on how much demand response to take up. Sainsbury's opted for a pilot scheme in two of its distribution centres. The success of this has led to a full roll out of demand response to the rest of its distribution centres. The next step may be to introduce demand response at store level.
Conclusion Working with a demand response aggregator, such as KiWi Power, can help ensure that businesses realise the full value of demand response participation. Following best practices, such as those highlighted above, and use of the latest technology, aggregators are able to help unlock revenues from various types of demand response programmes currently available. Nonessential services and processes can be identified to allow participation in demand response through comprehensive energy audits and by using existing or new standby power generation assets to provide optimum operational efficiency and performance.
MORE FROM THIS COMPANY
- Manufacturing downturn deepens as UK PMI falls to lowest level since February 2013
- PackagingTesters.com: Discover a one-stop solution for packaging testing
- Good Practice Guide for safe use of dumpers
- Free machine loans to support fight against coronavirus
- Movu Robotics powers production and logistics efficiency at Knorr-Bremse’s Lisieux plant
- GSM Online Label Sales - the online label and nameplate specialist
- Advancing continuous improvement with 3D printing
- Clearmark's coding solution helps improve efficiency
- Compressors meet university challenge
- EngineeringUK: "Imperative" to increase number of female students pursuing T Levels
RELATED ARTICLES
- No related articles listed
OTHER ARTICLES IN THIS SECTION