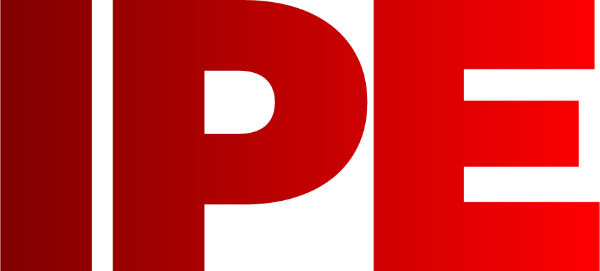
![]() |
Edward Lowton
Editor |
![]() ![]() |
Plasma power supply
28 September 2017
ESAB’s new iSeries power sources for automated plasma cutting are said to offer major productivity improvements and cost savings for stainless steel fabricators.
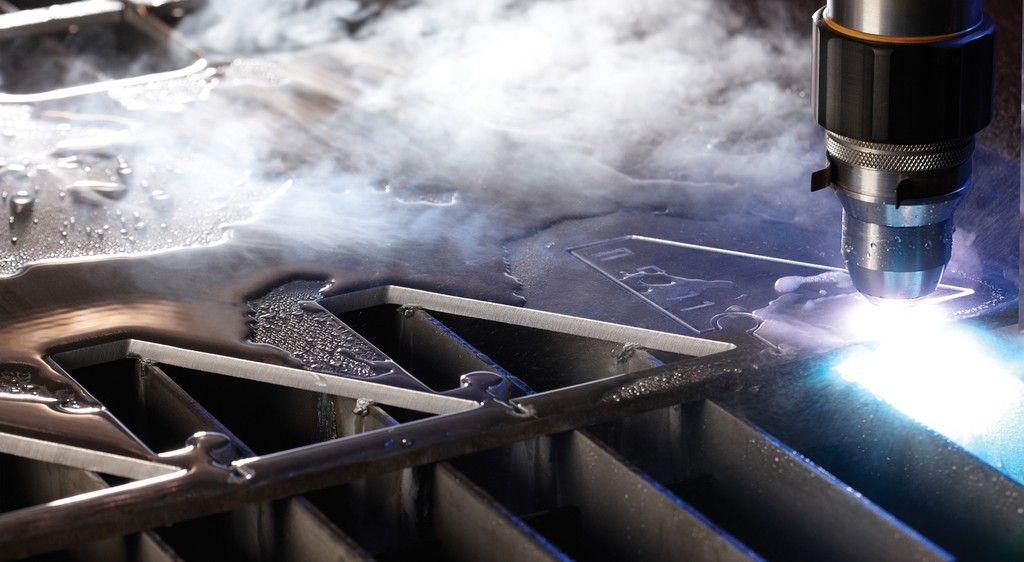
Designed as part of ESAB’s integrated system of components, and equally suitable for new systems and retrofits, according to ESAB the iSeries is the most advanced plasma power supply available today. With a maximum cut capability of 50 mm, the iSeries plasma power sources will benefit many industries utilising stainless steel. In many cases the iSeries will create new opportunities for applications previously dominated by laser and water jet cutting.
Three times faster
Thanks to the Water Mist Secondary (WMS) process, which uses nitrogen as the plasma gas and tap water for shielding, the iSeries power sources are said to cut up to three times faster and reduce the cost-per-cut by 20 per cent or more compared to systems using argon-hydrogen for the plasma gas. The higher productivity and lower cost-per-cut do not compromise cut quality.
HeavyCut technology ensures cut quality and precision performance are excellent, meaning that parts can go directly from the cutting table to welding or fabrication without the need for expensive secondary operations. The iSeries achieves a cut quality of ISO Class 3 or better on stainless steel from gauge to 50 mm thick, noticeably reducing bevel. It is also capable of piercing plate up to 50 mm thick.
Affordable and upgradeable
The iSeries is available in 100 to 400 A configurations and one of the advantages is the upgradeability. If customers purchase a 100, 200 or 300 A model, they can subsequently upgrade it by purchasing StepUp inverter block modules that can be installed by a field engineer in less than 30 minutes. The maximum output is 400 A but, even when a power source is rated at this maximum, the current output can still be turned right down to 5 A for cutting thin sheet. Should an inverter block malfunction, indicated via the LED display, cutting can continue with the remaining blocks.
Less downtime
Another way in which the iSeries saves money for customers is the XTremeLife Wear Parts for cutting at 300 and 400 A. These consumables use a multiple hafnium insert as opposed to a single insert and feature a two-piece tip that runs cooler. Better cooling extends parts life and cut accuracy across the life of the tip, especially when piercing at higher amperages. In addition, the SpeedLok cartridge design results in the fastest torch changes in the industry. These combined features can lower operating cost by as much as 70 per cent on stainless steel.