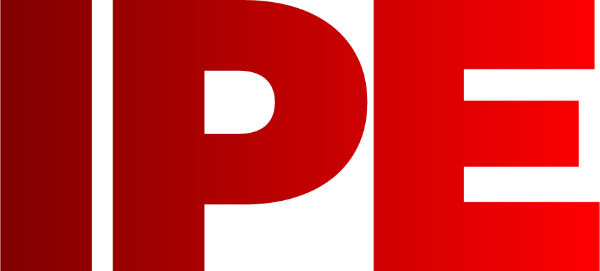
![]() |
Edward Lowton
Editor |
![]() ![]() |
Home> | Production Engineering | >Materials | >Additive manufactured electric motor |
Additive manufactured electric motor
15 October 2021
A TEAM of experts at the Coventry-based Manufacturing Technology Centre is developing an electric motor made from 3D printed components - one of the first organisations in the world to achieve this landmark.

The team, from the MTC's National Centre for Additive Manufacturing along with the centre's electrification experts, has developed a way of producing an electric motor with major components made using additive manufacture.
The result is a motor with increased motor power despite a reduction in the size and mass of key components, a part count reduction making supply chains simpler, increased manufacturing efficiency, lower running costs and reduced assembly and inspection time and costs.
Although a 3D-printed electric motor has been the subject of theoretical studies in the past it has never reached commercial reality. The MTC team has now cleared a path for the development and production of an electric motor using additive manufacture. It has already developed a way of producing an electric motor casing including integrated cooling channels using additive manufacture and the ambition is for the motor to be wholly manufactured using additive manufacture.
MTC chief technologist Steve Nesbitt said the development of electric motors hadn't received this level of focus for more than 100 years, despite costs, quality and performance being high on manufacturers' priority lists.
"Additive manufacturing is a key enabler for developing the complex features and forms essential to improving the performance and functionality of electric motors.
"The process of manufacturing electric motors has a number of challenges including complex or manual assembly, materials that are difficult to process and which can be expensive, thermal management, and the need to make the assembly lighter. By leveraging the capabilities of additive manufacture through product redesign major benefits can be achieved in costs, waste reduction, performance and ease of manufacture."
The MTC's experts are now involved in a detailed examination of further developments required for production, and overcoming potential challenges and constraints.
- Working together
- Advanced Manufacturing Degree to be launched by MTC
- West Midlands leads UK industrial recovery
- Electron beam melting races to the fore
- Self-contained robot cell delivers entry route for first-timers
- Standards partnership on additive manufacturing
- Mike Wilson Joins MTC as Chief Automation Officer
- Manufacturing leaders to help UK industry embrace latest technologies
- Calls to consider West Midlands for Gigfactory site
- New 3D printing system manufacturer joins MTC