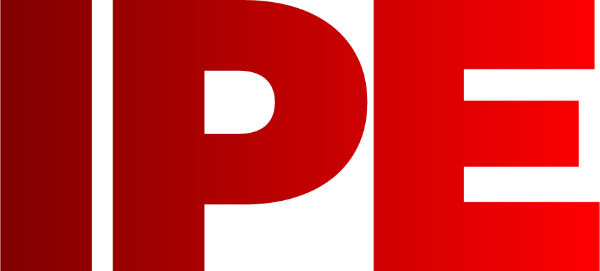
![]() |
Edward Lowton
Editor |
![]() ![]() |
Home> | Plant, Process & Control | >Bearings | >Custom white metal bearings |
Custom white metal bearings
27 October 2020
WHITE METAL or Babbitt bearings are used in a wide variety of rotating machinery and, just like conventional roller or ball bearings, they need to be replaced when they reach the end of their service life. Replacements can be manufactured by specialists such as Sulzer’s Southampton Service Center, which has recently upgraded its facilities.
For some of the largest industrial machines, roller or ball bearings are not suitable and here white metal bearings play an important role. Without them, generators and turbines would cease to turn, stopping the production of power that is vital to industry and everyday life.
White metal bearings are designed to operate with a film of oil in between the bearing surface and the rotating shaft. The most common failure mode is caused by a lack of lubrication and this will normally be highlighted during regular inspections. Once the issue has been identified, it is important to plan for a maintenance intervention at the earliest opportunity.
Sulzer’s Southampton Service Center is equipped to pour and machine white metal bearings to almost any size. Sulzer has invested in its facilities to increase capacity and ensure the continued manufacturing of high quality bearings. This has included the addition of facilities to manufacture white metal spindles for specialist applications.
Simon Dawkins, general manager operations in Southampton for Sulzer explains: “We can adapt our processes and equipment to meet specific customer needs. For example, we created a special piece of equipment that can pour white metal spindles for a customer that needed a unique solution. Our flexibility and precision means that we can deliver comprehensive solutions, including in-situ repairs on marine vessels.”
Once a white metal bearing is delivered for refurbishment, Sulzer can remove the remaining white metal and reuse it to create the new bearings. White metal bearing composition is dictated by the application and Sulzer assesses the exact materials used in the original bearing to ensure that the new component matches it exactly.
Dawkins concludes: “We have the capability to turn around the majority of projects within seven days. To date, the largest bearing we have created had a 1’450 mm (57 inch) diameter and we embrace challenges in more unusual applications to help our customers keep their equipment operational.”
- Challenging offshore motor rewind
- Sulzer installs six HST 20 turbocompressors for Severn Trent
- Turbocompressors boost efficiency at wastewater plant
- Advanced pump analysis proves invaluable
- Sulzer begins Baton Rouge expansion project
- Pump retrofit project paid off in weeks
- Component repair times cut with laser metal deposition
- IoT condition monitoring in the process industry
- Sulzer launches new features for AHLSTAR
- AHLSTAR improves sump pumping in cardboard mill