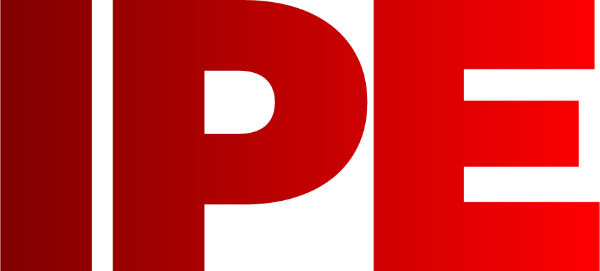
![]() |
Edward Lowton
Editor |
![]() ![]() |
Home> | Plant, Process & Control | >Bearings | >High precision efficiency savings |
ARTICLE
High precision efficiency savings
25 January 2013
Leicester-based AETC was having to replace high numbers of bearings in its CNC machines, so the high precision machining company asked Brammer to find a solution. Brammer provided an analysis of bearing failures with
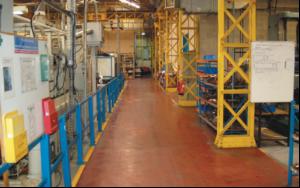
Leicester-based AETC was having to
replace high numbers of bearings in
its CNC machines, so the high
precision machining company asked
Brammer to find a solution.
Brammer provided an analysis of bearing failures with strategic supplier Timken. This enabled specific failure modes to be identified, with technical solutions introduced to increase mean time between failures.
Failures were typically due to poor fitting, a factor which research shows causes 16% of all premature bearing failures, and inadequate lubrication, which is responsible for more than a third of failures. Brammer and Timken were even able to diagnose problems caused by running different bearing brands simultaneously in one machine.
Brammer set up training sessions to help inform managers and engineers of best practice in bearing specification and maintenance. Cost savings are now being realised, and it is estimated that AETC will have to spend £5000 less on replacement products as the lifecycle of the bearings is longer.
Brammer provided an analysis of bearing failures with strategic supplier Timken. This enabled specific failure modes to be identified, with technical solutions introduced to increase mean time between failures.
Failures were typically due to poor fitting, a factor which research shows causes 16% of all premature bearing failures, and inadequate lubrication, which is responsible for more than a third of failures. Brammer and Timken were even able to diagnose problems caused by running different bearing brands simultaneously in one machine.
Brammer set up training sessions to help inform managers and engineers of best practice in bearing specification and maintenance. Cost savings are now being realised, and it is estimated that AETC will have to spend £5000 less on replacement products as the lifecycle of the bearings is longer.
MORE FROM THIS COMPANY
- Maintaining a competitive edge
- Guide launched
- Fan solution for cement plant
- Extended range in new catalogue
- Identifying bearings challenges in the F&D sector
- Bearing failure: Causes and solutions
- New engineering centre opens
- Avid supporter of Team Green
- Lubrication solution for sawmill
- Forum plus Awards lunch
OTHER ARTICLES IN THIS SECTION