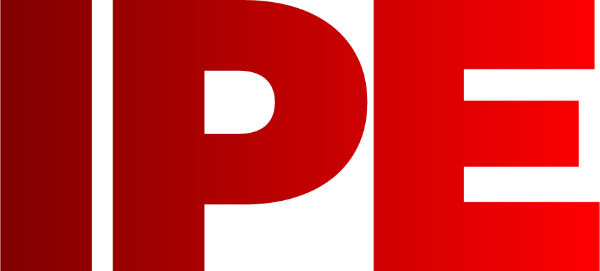
![]() |
Edward Lowton
Editor |
![]() ![]() |
Home> | Handling and Storing | >Conveyors | >Farnell installs new powered conveyor solution at its Leeds DC |
Farnell installs new powered conveyor solution at its Leeds DC
02 September 2024
Leeds-based Farnell needed a new powered conveyor system which would integrate with its existing system without interrupting operations

FARNELL IS a global distributor of electronic components. The business’ ongoing growth highlighted a need to increase the stock holding in its Leeds Distribution Centre (DC).
"Initially, we approached the supplier who had designed and installed the original semi-automated system. Unfortunately, the post COVID demand for automated logistics solutions meant that the lead times they were quoting were simply too long," explained Farnell’s head of UK operations. "Consequently, we made the decision to go out to tender for the next phase of development." The company Farnell selected was BS Handling Systems, based on its competitive proposal and short delivery time-frame.
Designing the integrated conveyor solution
"At the first design meeting, the BSH team walked around the existing system and listened to our thoughts about how the new powered conveyor system could work.
"They took our thoughts and their perceptions of the system away with them and came back with what was clearly a thoroughly well-thought out solution. The proposed design included five merge points with the existing system. One taking totes with in-bound stock to be put away in one of three zones in the new storage/picking area on the mezzanine floor.
"The second merge enabling totes with part orders coming from the automated mini load system to divert to the new picking area to collect additional product orders. A merge direct to packing/despatch on the ground floor, the merge of picked totes back into the original system on the mezzanine floor and the empty tote feed from the original system on the ground floor up to the infeed on the mezzanine.
"With the new system, we’ve integrated the logic and the picking sequences which is important for bringing it all together at the end with the existing system. The design also includes a couple of ‘short-cut’ conveyor routes to take completed orders directly to the despatch area to save time and avoid potential congestion on the main system.
Installing the new conveyors with minimum disruption
"One of our key drivers for the installation of the new powered conveyor system was that it must not interrupt our existing service. The DC had to continue operating at its normal throughput so that our customers where not let down or disappointed in any way.
"Naturally, all the work had to be done safely following Construction, Design and Management Regulations 2015 (CDM). This meant fencing off any part of the live operations with the potential for disruption this could cause.
"The excellent work they did integrating the new conveyors into the original system gave us the confidence to add their name to the tender list for additional high bay pallet racking that we required.
"Yet again, BS Handling Systems’ quote and installation schedule offered the best solution, so we appointed them to carry out that work too. This storage area was also completed on time and in budget."
For more information:
Tel: +44 116 289 4958
- No related articles listed