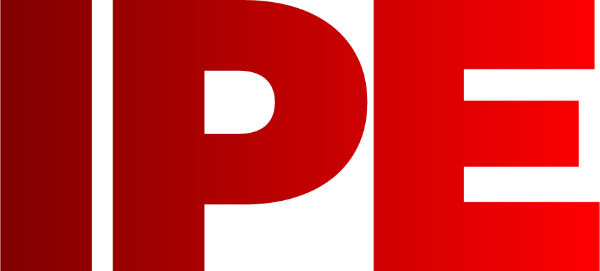
![]() |
Edward Lowton
Editor |
![]() ![]() |
Home> | Handling and Storing | >Conveyors | >Keeping cockpits on the move |
ARTICLE
Keeping cockpits on the move
25 January 2013
Excel Monorail Systems, a division of Excel Automation, has completed an extension to a conveying and handling system, which has enabled a Cockpit fit station to be re-located 20m further along a car production line. C
Excel Monorail Systems, a division of Excel
Automation, has completed an extension to a
conveying and handling system, which has
enabled a Cockpit fit station to be re-located
20m further along a car production line.
Cockpits for the MINI range are delivered to Plant Oxford from the Magna Intier plant at Redditch using special road transport trailers with on-board, chain-driven live roller conveyor systems. On arrival, the trailer is docked with the receiving conveyor. Due to process changes, the Cockpit fit station needed to be relocated further along the production line. The move required the design of a new conveying and handling system to transport the loaded platen out of the drop section to the new fitting position, relocating the manipulator (and standby manipulator), implementing a new light guard array to the new position and a means of returning the platen to the drop section for onward despatch.
Excel Automation was awarded the contract on commercial grounds and was able to show the MINI team a similar system at its Worcester factory. Excel had also installed a handling and conveying system for sequencing the same cockpit platens at the Magna Intier Redditch plant.
The new 20m conveying system now takes the platen on a two-tier conveyor to a new Cockpit fit station where it is removed from the platen and fitted to the vehicle. The empty platen is then returned to the drop section that brought it to the ground floor.
Cockpits for the MINI range are delivered to Plant Oxford from the Magna Intier plant at Redditch using special road transport trailers with on-board, chain-driven live roller conveyor systems. On arrival, the trailer is docked with the receiving conveyor. Due to process changes, the Cockpit fit station needed to be relocated further along the production line. The move required the design of a new conveying and handling system to transport the loaded platen out of the drop section to the new fitting position, relocating the manipulator (and standby manipulator), implementing a new light guard array to the new position and a means of returning the platen to the drop section for onward despatch.
Excel Automation was awarded the contract on commercial grounds and was able to show the MINI team a similar system at its Worcester factory. Excel had also installed a handling and conveying system for sequencing the same cockpit platens at the Magna Intier Redditch plant.
The new 20m conveying system now takes the platen on a two-tier conveyor to a new Cockpit fit station where it is removed from the platen and fitted to the vehicle. The empty platen is then returned to the drop section that brought it to the ground floor.
MORE FROM THIS COMPANY
OTHER ARTICLES IN THIS SECTION