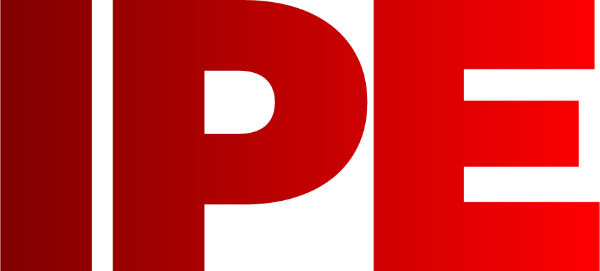
![]() |
Edward Lowton
Editor |
![]() ![]() |
Home> | Health, Safety & Welfare | >Plant and machinery safety | >Looking after your metalworking fluid |
Looking after your metalworking fluid
18 October 2023
DAVID WRIGHT, director general of the United Kingdom Lubricants Association discusses the benefits of adopting a pro-active approach to metalworking fluid management.

The right approach to metalworking fluid management can not only save your company many hours of unnecessary downtime over the long run, but can also add up to big cost savings in having to replace metalworking fluid in your machines over the short-term.
Let’s face it every workshop or factory owner wants to maximise their machine shop efficiency whilst minimising downtime which can be costly and time-consuming. Ensuring the health and safety of machine operators working with metalworking fluids on rolling, cutting or forming metal, is a key part of this.
Managing your metalworking fluids
Regular inspections of factories and workshops undertaken by the Health and Safety Executive in England and Wales has brought the management, and risks, of metalworking fluids to the top of the health and safety agenda.
Enforcement notices relating to individual operator health such as failing to ensure that the exposure of employees to metalworking fluid mist, a substance hazardous to health, is prevented or adequately controlled, or failing to provide health surveillance to employees who are or are liable to be exposed to a substance hazardous to health, namely metalworking fluids, are not uncommon.
Enforcement notices can take a number of different types from providing information and advice face-to-face or in writing, serving notices on duty holders, withdrawing approvals, varying licences, conditions or exemptions, issuing simple cautions or at worst, prosecution.
The Health and Safety Executive have a responsibility to ensure the safety of industrial premises enshrined within the Health & Safety at Work Act of 1974, and is the is the primary piece of legislation covering occupational health and safety in Great Britain. Since its introduction the Act has helped Great Britain become one of the safest workplaces in Europe if not the world in which to work. But more needs to be done.
Protecting employees
According to HSE, the estimated number of working days lost due to work-related ill health and non-fatal workplace injuries in 2021/22 is 36.8 million or on average 16.5 days for every worker. Within this 36.8 million days, 6 million were lost to non-fatal accidents and 30 million due to Injuries, Ill health cases, stress, depression or anxiety, and musculoskeletal disorders. These statistics which were broadly flat before the coronavirus pandemic, have remained stubbornly higher ever since.
The law requires under the Control of Substances Hazardous to Health employers to carry out a suitable and sufficient risk assessment for those exposed to Metalworking Fluid (MWF). The risk assessment should identify the measures required to ensure that exposure is either prevented or adequately controlled, such as kept to a minimum.
Adequate control of exposure can be achieved by reducing skin contact with MWF, reducing inhalation of MWF mist to levels "as low as reasonably practicable", ALARP, and applying control principles by designing operating procedures and activities to minimise emissions and contact with MWF.
In 2016, HSE launched its strategy Helping Britain to Work Well which changed its focus solely from safety at work to take account of the well-being of factory and workshop workers in industrial premises. In metalworking fluid handling the two biggest risks to operator health are lung and skin disease.
Reducing exposure to metalworking fluid mist
On lung health, the inhalation of metalworking fluid mist is a significant risk that must be minimised at work. Operator health is paramount and days lost from work due to ill-health can quickly impact on machine shop efficiency, production downtime and missed customer order fulfilment which can cost companies a great deal of money and lost reputation that are both hard to recover.
Taking a few simple steps to ensure all machine guards are used, enclosures are shut in operation, Local Exhaust Ventilation to extract fluid mist is used where available, and the avoidance of using compressed airlines to clean machines at the end of shift, where possible. This includes allowing the machine enclosure to clear of mist after machining which can be achieved through a time delay switch on the enclosure door.
Recognising that compressed airlines might be in common use, it is essential that machine operators wear protective personal equipment such as face coverings, gloves, safety shoes and overalls to minimise skin contact. Dermatitis is an unpleasant resulting effect of skin coming into contact with metalworking fluid. The use of disposable nitrile gloves and knowing the right way to put these on, and take these off at the end of shift can significantly reduce skin contact.
The fundamental principle of health and safety law is that those who create risks are best placed to manage them. Every workshop could be different from the type of environmental conditions experienced such as the level of humidity in the air, the type of machining carried out, the number of machines used, and the type of metal worked in the machine shop all add up. There is no one size fits all but the basic principles of safe effective practice, remain.
Guidance for machine operators
Following the publication of Good Practice Guidance in the Safe Handling and Disposal of Metalworking Fluid produced by the United Kingdom Lubricants Association in collaboration with the Health and Safety Executive in 2018 and updated in 2021 which can be found at www.ukla.org.uk, a series of training videos have been produced aimed at machine operators such as managing and maintaining fluid quality, dealing with Tramp Oil, how to take samples and checks, maintaining the pH of metalworking fluid and managing and monitoring bacteria.
The training videos form part of a series titled Looking after your Metalworking Fluid, and are all available for streaming in easily digestible three to five minute segments that take the viewer through the different steps in managing metalworking fluid quality. All videos are available through links on the metalworking fluid pages of the UKLA website listed above, as well as being made available directly through UKLA’s Metalworking Fluid Product Stewardship Group’s You Tube channel.
Undertaking a risk assessment, taking a series of reasonable and practicable steps along with regular checks of fluid quality through dip slides or the use of a refractometer can all help to minimise risk. The control of bacteria is key to managing fluid quality. Reducing or minimising where possible colony forming units (CFUs) to 10,000 CFU/ml (104 CFU/ml) involves weekly checks.
But daily checks are also recommended on the visual appearance of the fluid, weekly checks for tramp oil and operating temperature and pH all help provide a proactive approach to fluid management that can reduce downtime, minimise operator ill-health and maintain an efficient, healthy and safe workshop.
United Kingdom Lubricants Association
Tel: 01442 875922
Email: [email protected]
Web: www.ukla.org.uk