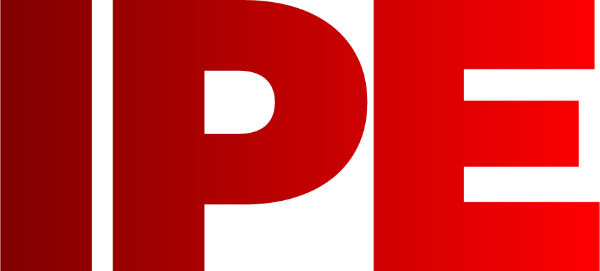
![]() |
Edward Lowton
Editor |
![]() ![]() |
Home> | Efficient Maintenance | >Industry 4.0 | >A closer look at remote machine maintenance |
A closer look at remote machine maintenance
22 September 2023
THE GLOBAL pandemic and Brexit, let alone the other socio-economic pressures that the UK has been facing, have presented numerous challenges for UK manufacturers. As they strive to remain competitive in an increasingly uncertain business landscape, embracing digital transformation solutions, such as remote machine maintenance, has become essential.

Many GAMBICA members thrived from offering this service throughout these times, and the importance of remote machine maintenance for UK manufacturers, was championed through a ‘new way of working’ despite the word “new” not necessarily being true, for a technology which had been around for more than a while. With the aim to enhance their operational efficiency, reduce costs, and ensure business continuity in the face of disruptions, remote solutions became essential for customers.
Adopting new approaches to digitisation
These socio-economic pressures, not only resulted in supply chain disruptions, labour shortages, and reduced access to the European market, but also embedded within these pressures was the discovery of a new mindset and approach to digital technologies, where they became more of a necessity over novelty.
Amidst these difficulties, maintaining the productivity and uptime of machinery became crucial. Traditional on-site maintenance services were no longer viable due to travel restrictions and social distancing requirements. This has gave rise to the adoption of remote machine maintenance solutions.
The benefits of remote machine maintenance
Remote machine maintenance enables UK manufacturers to optimise their operational efficiency. With digital connectivity, technicians can monitor, diagnose, and troubleshoot equipment from a centralised location. Real-time data analytics and predictive maintenance algorithms can identify potential issues before they escalate, minimising downtime and production losses.
Manufacturers can proactively schedule maintenance activities, ensuring minimal disruption to operations. By leveraging remote machine maintenance, manufacturers can streamline their processes, improve equipment reliability, and enhance overall productivity.
Implementing remote machine maintenance solutions also offers significant cost-saving opportunities for UK manufacturers. Traditional on-site maintenance involves travel expenses, accommodation costs, and technician wages. Remote maintenance eliminates these added costs by reducing the need for physical presence. Additionally, swift detection and resolution of machinery issues prevent costly breakdowns and repairs. Manufacturers can avoid the financial burden associated with prolonged downtime and unscheduled maintenance.
Ensuring uninterrupted operations
Furthermore, remote machine maintenance enables businesses to ensure uninterrupted operations during crises or emergency situations. The global pandemic and Brexit-related uncertainties have demonstrated the importance of agile and adaptable approaches to manufacturing. By relying on remote maintenance, manufacturers can swiftly respond to changing circumstances, allocate resources effectively, and mitigate the impact of disruptions. They can also remotely monitor multiple facilities, centralise maintenance processes, and optimise resource allocation across multiple sites.
Digital transformation solutions, such as remote machine maintenance, have become key differentiators in today's competitive manufacturing landscape. Companies that embrace these technologies gain a competitive edge by increasing their responsiveness, flexibility, and adaptability. Remote maintenance enables manufacturers to leverage artificial intelligence, machine learning, and IoT capabilities, enhancing their predictive maintenance capabilities and reducing unplanned downtime.
Strengthening collaboration
Moreover, remote machine maintenance fosters better collaboration between manufacturers and equipment suppliers. This is more evident amongst GAMBICA members who share similar sectors. Real-time communication and shared access to machine performance data allow for faster and more effective troubleshooting and support. Manufacturers can leverage the expertise of suppliers remotely, reducing the need for expensive and time-consuming on-site visits.
In the face of the global pandemic and Brexit challenges, UK manufacturers managed to adapt and remain competitive. In the Industrial Automation sector at GAMBCIA, we were able to see a growth in performance of the sector, showing a resounding resilience throughout these times. It was brilliant to see manufacturers working together to champion British industry and enabling new technology to prevail in a time of need.
GAMBICA
Tel: 020 7642 8080
Email: [email protected]
Web: www.gambica.org.uk
- Technology and Open Standard data enabling smart maintenance
- Broadband sensors: Pinpointing leaks in compressed air systems
- Mechanised welding, cutting and Industry 4.0
- Tomorrow’s tech is here today
- Investment in infrastructure, innovation and people
- Getting to 4.0 – one hard-won gain at a time
- Digital transformation in the chemical industry: White paper
- Digital industry around the world
- Guidance via AR
- How machine learning is transforming predictive maintenance