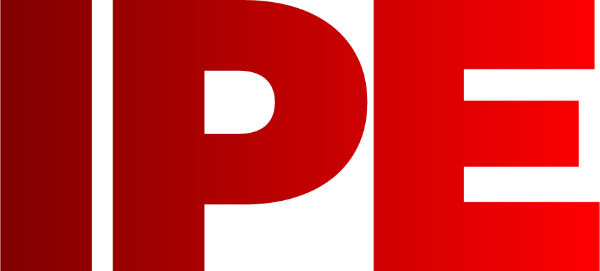
![]() |
Edward Lowton
Editor |
![]() ![]() |
Home> | Efficient Maintenance | >Industry 4.0 | >Technology and Open Standard data enabling smart maintenance |
Technology and Open Standard data enabling smart maintenance
18 May 2018
Taking care of maintenance in an industrial or building setting involves many considerations for maintenance operators – from sourcing the right products to creating cost and energy efficiencies. However, the space has been revolutionised thanks to an array of smart maintenance products, reports Allen Boney, local product manager, Electrical and Test & Measurement, RS Components
From retro-fittable smart sensors to detect wear and tear and plan life-cycles of parts, to test and measurement devices to pre-empt maintenance, being smart in this area saves on both costs and downtime. Another development is manufacturers working collaboratively in the open-standard of IO-Link when it comes to creating a universal data structure for usage information. Extra data can be streamed from intelligent sensors to maintenance teams, enabling pre-emptive, timely and smart maintenance decisions to be made based on solid and accurate data.
Sensor connectivity and communication
Production processes rely heavily on sensors providing basic measurement data for their ongoing, satisfactory operation, especially in terms of process control. However, the arrival of IO-Link – a powerful standard used to communicate with sensors and actuators – means new data about the process can be captured and unlocked, generating further information for better decision making. Being manufacturer agnostic, IO-Link allows sensors to provide operation management and maintenance teams with more information on the performance of the sensor or actuator.
IO-Link allows process variables, identification information, parameters and device status to be sent – helping avoid replacement with the wrong device model. It also allows for sensor parameters to be stored in the controller and automatically transferred when the unit is replaced. It simplifies equipment replacement, reduces the level of training required, reduces maintenance costs through better diagnostics and prevents downtime.
Upgrade with minimal cost
One of the major benefits of IO-Link technology is its use of existing wiring. It transmits the additional information via the 3-wire connection used by the sensor or actuator without affecting its basic operation. This means IO-Link is invisible to the system unless a gateway is used to interface with this data, which allows IO-Link enabled sensors to be implemented into existing machines or designs with minimal re-work – saving on upgrade costs.
Some maintenance operators might choose Ethernet enabled sensors such as thermal imagers and vision sensors, which are mounted in the process and transmit data via open Ethernet standards such as Modbus/TCP. Vision sensors such as the Telemecanique OsiSense XUW easily integrate into machinery and are dedicated to the inspection of manufactured parts. They allow checking of high production rate operations, ensuring high repeat accuracy, and can be used to manage objects' flow.
Connected test and measurement
IO-Link and sensors are effective for predictive maintenance, but it’s worth using a combination approach. Both portable and fixed test and Measurement instruments allow engineers to share and log data via open standards such as Bluetooth and Wireless Ethernet (IEEE 802.11). Permanently installed test and measurement equipment is ideal to help identify issues and for use when a need arises to assess a piece of equipment in a part of a plant that may be unsafe to enter. It is also useful for sending information from one engineer to another, when giving guidance on a particular issue.
RS works with CorDEX, which offers the MN4100 dual vision thermal imaging camera that captures fully radiometric data every second, and provides continuous temperature monitoring and alarming for critical electrical and mechanical equipment. Manufacturers such as FLIR offer a way to streamline hand-held thermal inspections and simplify data collection and reporting: its InSite Inspection Management Application is a professional workflow tool for electrical contractors and thermographers, allowing the streamlining of thermal inspections and simplified data collection and reporting in one location that's easy to access, manage, and share. This gives the maintenance team high-quality data on which to make decisions, schedule repairs and maximise uptime.
Negating product and parts wastage caused in scheduled preventative maintenance, whilst managing risk of downtime arising from product failure by facilitating predictive maintenance is a balance that the latest products help maintenance professionals achieve. Whilst IO-Link has become established and has a high level of manufacturer support, there needs to be similar support available from machine builders and integration partners to ensure operational benefits are fully realised.
- RS Components wins European Distribution Gold Award
- Tackling mounting challenges to keep water and wastewater flowing
- HVAC smart probes sync wirelessly with smartphones
- PPE selection guide
- RS releases 2025 Indirect Procurement Report: Tackling the cost of business
- Affordable 3D solution for design bottlenecks
- Tool cabinets and tool modules
- RS appoints new Regional Managing Director for UK and Ireland
- Gravity: The human propulsion flight suit
- Reinforcing support for maintenance engineers
- Broadband sensors: Pinpointing leaks in compressed air systems
- Mechanised welding, cutting and Industry 4.0
- Tomorrow’s tech is here today
- Investment in infrastructure, innovation and people
- Getting to 4.0 – one hard-won gain at a time
- Digital transformation in the chemical industry: White paper
- Digital industry around the world
- Guidance via AR
- How machine learning is transforming predictive maintenance
- Real-time data helps reduce costs and machine downtime