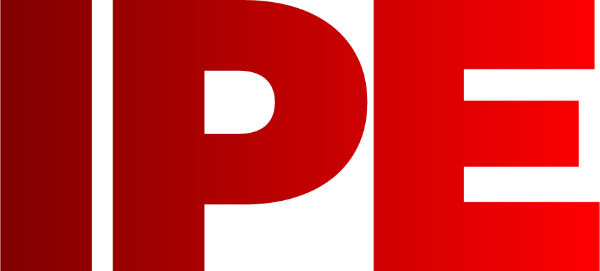
![]() |
Edward Lowton
Editor |
![]() ![]() |
Home> | Efficient Maintenance | >Maintenance products | >Maintenance in better health |
ARTICLE
Maintenance in better health
25 January 2013
It's 10 years since a vast maintenance project was started at the Hospices Civils de Lyon (HCL). More recently, the project involved installation of a CARL Master CMMS (computerised maintenance management system).Val Keale
It's 10 years since a vast maintenance project was started at
the Hospices Civils de Lyon (HCL). More recently, the project
involved installation of a CARL Master CMMS (computerised
maintenance management system).Val Kealey visited the
hospital to find out more
The HCL East Hospitals group includes the hospitals Pierre Wertheimer, Louis Pradel and the Femme Mere Enfant on a site that comprises buildings and technical facilities built between 1963 and 2007. At the end of the 1990s several incidents, including electricity outages, led HCL management and technical services division to give serious consideration to the maintenance of the building and facilities of the Hospices Civils de Lyon.
The conclusion was that the buildings and facilities, which cover 850,000m2 of developed site, consisted of mixed and ageing facilities that had not been subject to effective preventive maintenance. The maintenance function was fragmented; there was no dedicated technical management and those carrying out the work had no clearly defined goals.
The decision was taken to reorganise and modernise maintenace procedures and the 'Maintenance Project' was started. A new Maintenance and Operations department was set up comprising 325 technical staff.
The department has an annual budget of €31.5m.
A technical strategy was developed with the aim of establishing a uniform and satisfactory level of service to ensure continuity of patient care. This included: Creation of four specific disciplines (high current, low current, water & air, and energy) with a lead engineer for each discipline.
An inventory of technical facilities Improving knowledge of the facilities Defining the role and scope of the maintenance department.
A recruitment campaign for maintenance engineers and lead engineers was launched in 2003 and the Maintenance and Operations Department was set up in January 2004. The department then identified critical areas under the four key disciplines, establishing a hierarchy of criticality of facilities within each discipline.
A division into geographical sectors was carried out to optimise management of those areas. The HCL is divided into four hospital zones of about 200,000m2 floor area, each with specialised workshops, staff and one lead engineer per sector.Maintenance staff were reorganised to strengthen technical know-how and knowledge of the equipment inventory, with the aim of improving the image of the technical services department.
CMMS project The size and complexity of the inventory to be managed, prompted the management team to opt for a CMMS. It chose CARL Software's CARL Master. The objective was to prioritise prevention of problems and ensure the security of the facilities. The CMMS project enables the HCL's 17 establishments to: Have a shared, easily accessed database Optimise, unify and rationalise monitoring of maintenance work Monitor the progress of work with work orders Trace and manage requests for work Improve the service provided to other hospital departments by technicians, for example, through information on the status of requests (pending / in progress/ completed.
The project was organised institutionally, with collaboration between DAT (Technical service Division) and the DSI (Information Systems Division). DAT took the lead in terms of the project's functions, the inventory of facilities and premises, software configuration and the adoption of the system by the maintenance teams. The DSI was responsible for integration with the HCL information system and for the supply of the computing infrastructure.
The deployment phase was the most onerous and involved: Installation of the computer equipment; inventory of premises/facilities with updating and labelling of maps; training of workshop staff; training of senior managers (users of Quick DI, the interface for requesting work); data entry; and commissioning.
This phase required major on-site support with the regular presence of a member of the project team, especially when the preventive workload was rising, to help avoid any problems.
The success of the deployment was deemed to depend on maintenance staff using the software in their day-to-day activities. About 120 staff were trained in the required computing skills and the entire maintenance team (350 people) was trained in the software (one to two days training according to their role).
Site workshops provided direct training for 'customers', ie those making work requests - ward managers, senior administrators and so on. This means that in excess of 1000 people underwent training and, although this involved considerable time, the project management team believed it to be necessary in order to establish a connection with 'customers', convincing them of the benefits of making a computerised work request.
The CMMS is centralised on a single database to ensure uniformity of maintenance functions. Apart from the geographical scale of the project, the main problems were the volume and organisation of data.
Database details (August 2011) Geographical points: 46,972 Installation families: 38; sub-families: 309 Installation points: 24,169 with 121,508 defined characteristics Work requests per month: about 6300 .
Work requests dealt with in less that 48h: about 70%.
Work requests dealt with in less than 72h: about 80% Work requests dealt with since commissioning: 247,792 Work tickets per month: about 9500. In 2010, 100,470 work orders were generated, with more than 30,000 orders generated by the technical service (generally preventive) and not by the 'customer' Active preventive triggers: 8764 Active preventive plans: 446 Contracts managed: 1016 CMMS users: in excess of 450.
The technical remit covers all of the hospital's fixed facilities: Electricity: A power station with five generators, transformers, low-voltage distribution panels, electrical cabinets, emergency lighting, and PABXs.
HVAC/plumbing: Boiler room with three combined gas/fuel boilers and 21 heating and hot water production substations (with associated sensors and pumps), refrigeration units, air treatment units, fan convectors, and softeners.
General maintenance: Lifts, automatic doors, pneumatic conveying lines, main vacuum pumps, networks of medical gases, and compressors.
Quick Di Quick Di is implemented on each of the sites. It simplifies work requests and permits tracking of progress by the person making the request. The user connects to Quick Di using his/her usual Windows password for starting the PC and accessing the network.
On connection, the person making the request can see the status of requests made over the past 30 days for his/her functional unit (this corresponds to the department to which the user belongs). This filter avoids having the same request several times as the user is able to see the requests made by his department over the previous 30 days.
The person making the request is also able to check on the progress made in processing the request, a factor that the maintenance team believes to be important in achieving customer satisfaction.
Ongoing The CMMS is an evolving software package and enlargement of the database at HCL is considered essential.Work will also continue on further ramping-up preventive maintenance tasks, integrating maintenance providers and establishing a stock management module.
Results The CMMS project is considered a success at HCL. It has played its part in the overall reorganisation of the maintenance function at the hospitals. Its implementation at all of the HCL sites was carried out progressively and had the support of the staff, who were kept well informed about the project. Staff involvement and the close support of the various teams involved stemmed from a strong desire to have in place a professional and down-to-earth tool.
Cost savings are difficult to identify, although there have been savings on staff costs. The true benefit, however, comes from the security the system provides. Since its installation there have been no major maintenance incidents, an enormous benefit to the hospital and one that it is difficult to put a price on.
The HCL East Hospitals group includes the hospitals Pierre Wertheimer, Louis Pradel and the Femme Mere Enfant on a site that comprises buildings and technical facilities built between 1963 and 2007. At the end of the 1990s several incidents, including electricity outages, led HCL management and technical services division to give serious consideration to the maintenance of the building and facilities of the Hospices Civils de Lyon.
The conclusion was that the buildings and facilities, which cover 850,000m2 of developed site, consisted of mixed and ageing facilities that had not been subject to effective preventive maintenance. The maintenance function was fragmented; there was no dedicated technical management and those carrying out the work had no clearly defined goals.
The decision was taken to reorganise and modernise maintenace procedures and the 'Maintenance Project' was started. A new Maintenance and Operations department was set up comprising 325 technical staff.
The department has an annual budget of €31.5m.
A technical strategy was developed with the aim of establishing a uniform and satisfactory level of service to ensure continuity of patient care. This included: Creation of four specific disciplines (high current, low current, water & air, and energy) with a lead engineer for each discipline.
An inventory of technical facilities Improving knowledge of the facilities Defining the role and scope of the maintenance department.
A recruitment campaign for maintenance engineers and lead engineers was launched in 2003 and the Maintenance and Operations Department was set up in January 2004. The department then identified critical areas under the four key disciplines, establishing a hierarchy of criticality of facilities within each discipline.
A division into geographical sectors was carried out to optimise management of those areas. The HCL is divided into four hospital zones of about 200,000m2 floor area, each with specialised workshops, staff and one lead engineer per sector.Maintenance staff were reorganised to strengthen technical know-how and knowledge of the equipment inventory, with the aim of improving the image of the technical services department.
CMMS project The size and complexity of the inventory to be managed, prompted the management team to opt for a CMMS. It chose CARL Software's CARL Master. The objective was to prioritise prevention of problems and ensure the security of the facilities. The CMMS project enables the HCL's 17 establishments to: Have a shared, easily accessed database Optimise, unify and rationalise monitoring of maintenance work Monitor the progress of work with work orders Trace and manage requests for work Improve the service provided to other hospital departments by technicians, for example, through information on the status of requests (pending / in progress/ completed.
The project was organised institutionally, with collaboration between DAT (Technical service Division) and the DSI (Information Systems Division). DAT took the lead in terms of the project's functions, the inventory of facilities and premises, software configuration and the adoption of the system by the maintenance teams. The DSI was responsible for integration with the HCL information system and for the supply of the computing infrastructure.
The deployment phase was the most onerous and involved: Installation of the computer equipment; inventory of premises/facilities with updating and labelling of maps; training of workshop staff; training of senior managers (users of Quick DI, the interface for requesting work); data entry; and commissioning.
This phase required major on-site support with the regular presence of a member of the project team, especially when the preventive workload was rising, to help avoid any problems.
The success of the deployment was deemed to depend on maintenance staff using the software in their day-to-day activities. About 120 staff were trained in the required computing skills and the entire maintenance team (350 people) was trained in the software (one to two days training according to their role).
Site workshops provided direct training for 'customers', ie those making work requests - ward managers, senior administrators and so on. This means that in excess of 1000 people underwent training and, although this involved considerable time, the project management team believed it to be necessary in order to establish a connection with 'customers', convincing them of the benefits of making a computerised work request.
The CMMS is centralised on a single database to ensure uniformity of maintenance functions. Apart from the geographical scale of the project, the main problems were the volume and organisation of data.
Database details (August 2011) Geographical points: 46,972 Installation families: 38; sub-families: 309 Installation points: 24,169 with 121,508 defined characteristics Work requests per month: about 6300 .
Work requests dealt with in less that 48h: about 70%.
Work requests dealt with in less than 72h: about 80% Work requests dealt with since commissioning: 247,792 Work tickets per month: about 9500. In 2010, 100,470 work orders were generated, with more than 30,000 orders generated by the technical service (generally preventive) and not by the 'customer' Active preventive triggers: 8764 Active preventive plans: 446 Contracts managed: 1016 CMMS users: in excess of 450.
The technical remit covers all of the hospital's fixed facilities: Electricity: A power station with five generators, transformers, low-voltage distribution panels, electrical cabinets, emergency lighting, and PABXs.
HVAC/plumbing: Boiler room with three combined gas/fuel boilers and 21 heating and hot water production substations (with associated sensors and pumps), refrigeration units, air treatment units, fan convectors, and softeners.
General maintenance: Lifts, automatic doors, pneumatic conveying lines, main vacuum pumps, networks of medical gases, and compressors.
Quick Di Quick Di is implemented on each of the sites. It simplifies work requests and permits tracking of progress by the person making the request. The user connects to Quick Di using his/her usual Windows password for starting the PC and accessing the network.
On connection, the person making the request can see the status of requests made over the past 30 days for his/her functional unit (this corresponds to the department to which the user belongs). This filter avoids having the same request several times as the user is able to see the requests made by his department over the previous 30 days.
The person making the request is also able to check on the progress made in processing the request, a factor that the maintenance team believes to be important in achieving customer satisfaction.
Ongoing The CMMS is an evolving software package and enlargement of the database at HCL is considered essential.Work will also continue on further ramping-up preventive maintenance tasks, integrating maintenance providers and establishing a stock management module.
Results The CMMS project is considered a success at HCL. It has played its part in the overall reorganisation of the maintenance function at the hospitals. Its implementation at all of the HCL sites was carried out progressively and had the support of the staff, who were kept well informed about the project. Staff involvement and the close support of the various teams involved stemmed from a strong desire to have in place a professional and down-to-earth tool.
Cost savings are difficult to identify, although there have been savings on staff costs. The true benefit, however, comes from the security the system provides. Since its installation there have been no major maintenance incidents, an enormous benefit to the hospital and one that it is difficult to put a price on.
MORE FROM THIS COMPANY
OTHER ARTICLES IN THIS SECTION