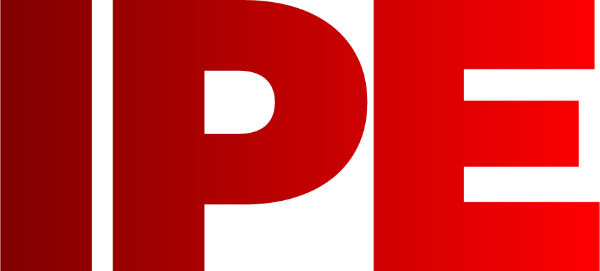
![]() |
Edward Lowton
Editor |
![]() ![]() |
ARTICLE
Cold rolling mill saves cash on bearings
25 January 2013
NSK's asset improvement programme is saving the operator of a Cold Rolling Mill €16,300 annually as a result of solving a problem of bearing failure.
NSK's asset improvement programme is saving the operator of a Cold Rolling Mill €16,300 annually as a result of solving a problem of bearing failure that was occurring three/four times per year, resulting in unplanned shutdowns and serious loss of production at the mill.
The mill operator was being forced to change bearings up to four times a year due to the harsh working environment in which the bearings operated. The bearings were failing prematurely due to contamination; ingress from dirt, debris and liquids that were affecting the bearing lubricant and shortening bearing life.
NSK was called in to find a solution to the failure problem. This involved engineers from the company analysing the mill bearings, and taking samples of the lubricant used (grease) to determine the actual operating conditions. At the conclusion of the analysis, NSK recommended using spherical roller bearings manufactured from the company's Super -TF steel, a material particularly suited for use in environments subject to contamination from debris.
A unique bearing material developed by NSK, Super-TF provides up to ten- times longer life in conditions of contaminated lubricant, in comparison with bearings made of ordinary carburised steel. Where the problem is related to insufficient lubrication, the life of Super TF bearings is still impressive at around 5.5 times that of ordinary carburised steel.
In addition to extending service life under conditions of contaminated or boundary lubrication, Super TF bearings also offer increased resistance to wear and seizure. In comparative tests with bearings made of conventional materials, such as AISI 52100 steel, the Super TF has shown less than one third the rate of wear and a 40% increase in seizure resistance.
Following NSK's recommendation, Super-TF spherical roller bearings were installed in the cold rolling mill. After 4-months in operation the bearings were disassembled & sent back to factory. The laboratory results found that the minimum residual life was between 29-50 months, compared to less than 4-months previously. To date the customer has replaced the bearings once, and that as part of a planned annual shutdown for scheduled maintenance.
The mill operator was being forced to change bearings up to four times a year due to the harsh working environment in which the bearings operated. The bearings were failing prematurely due to contamination; ingress from dirt, debris and liquids that were affecting the bearing lubricant and shortening bearing life.
NSK was called in to find a solution to the failure problem. This involved engineers from the company analysing the mill bearings, and taking samples of the lubricant used (grease) to determine the actual operating conditions. At the conclusion of the analysis, NSK recommended using spherical roller bearings manufactured from the company's Super -TF steel, a material particularly suited for use in environments subject to contamination from debris.
A unique bearing material developed by NSK, Super-TF provides up to ten- times longer life in conditions of contaminated lubricant, in comparison with bearings made of ordinary carburised steel. Where the problem is related to insufficient lubrication, the life of Super TF bearings is still impressive at around 5.5 times that of ordinary carburised steel.
In addition to extending service life under conditions of contaminated or boundary lubrication, Super TF bearings also offer increased resistance to wear and seizure. In comparative tests with bearings made of conventional materials, such as AISI 52100 steel, the Super TF has shown less than one third the rate of wear and a 40% increase in seizure resistance.
Following NSK's recommendation, Super-TF spherical roller bearings were installed in the cold rolling mill. After 4-months in operation the bearings were disassembled & sent back to factory. The laboratory results found that the minimum residual life was between 29-50 months, compared to less than 4-months previously. To date the customer has replaced the bearings once, and that as part of a planned annual shutdown for scheduled maintenance.
MORE FROM THIS COMPANY
- NSK academy adds online training module for food and beverage applications
- Problem solved
- Recycling plant saves over €50k per year
- Self-lubricating deep groove ball bearings
- Self-Lube bearing inserts
- Guide on prolonging bearing life for cement producers
- Bearing up to cement dust
- NSK debuts new bioplastic cage bearings
- Green power for NSK's Europe plants
- NSK bearings and training help woodworking machine builder make savings
RELATED ARTICLES
- No related articles listed
OTHER ARTICLES IN THIS SECTION