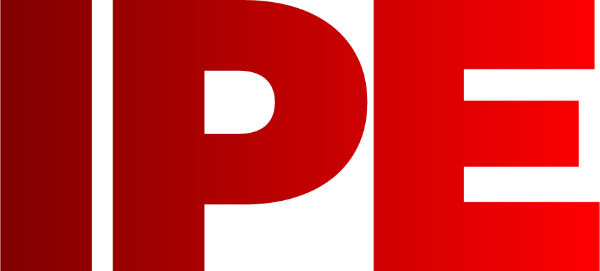
![]() |
Edward Lowton
Editor |
![]() ![]() |
Home> | Energy Management | >Compressors & ancillary equipment | >Latest vacuum pumps: Potential for energy savings |
Home> | Plant, Process & Control | >Pumps | >Latest vacuum pumps: Potential for energy savings |
Latest vacuum pumps: Potential for energy savings
20 July 2015
New from Atlas Copco, the new GHS 350-900 VSD+ range of vacuum pumps for the UK manufacturing industry promises benefits including average energy savings of 50% compared with conventional oil-sealed and dry vane vacuum pumps, as well as best in class noise levels and oil retention.
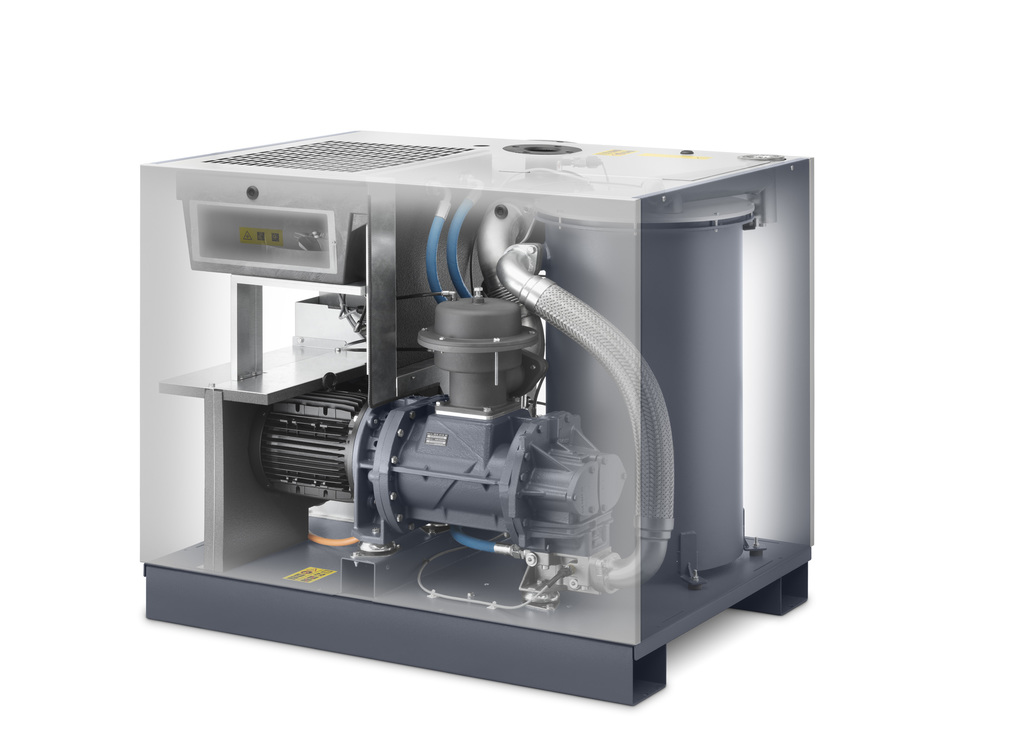
Dirk Ville, general manager of Atlas Copco Compressors UK, said: "With clear synergies between compressed air and vacuum, which represent the ‘Yin’ and ‘Yang’ of air movement, Atlas Copco has been able to use its advanced compressor technology experience to design the GHS VSD+ , leading to a breakthrough in energy efficiency, capable of dramatically reducing UK manufacturers’ lifecycle costs.
"Approximately three-quarters of companies who use rough vacuum require oil-injected pumps, which are traditionally fixed-speed, so the potential for energy savings across UK industry is massive."
The GHS 350-900 VSD+ range, generating nominal displacement of up to 900m3/h, incorporates state-of-the-art VSD technology that enables users to precisely adapt their vacuum generation requirements to match the demands of their process. Coupled with an innovative motor design and inlet control valve, the new range is said to set new standards for energy efficiency in rough vacuum pumps, leading to a reduction in total cost of ownership.
The GHS VSD+ vacuum pump only delivers energy and performance when and where it is needed. If demand drops to half, it only delivers half, and the power consumed is halved. Atlas Copco says this is one of the main reasons why the GHS VSD+ is capable of providing energy savings of 50% on average.
The range is designed to aid efficient production in a wide range of manufacturing industries, such as food and meat processing, bottling, canning, plastics, packaging, printing, paper, electronics, woodworking, house vacuum and central systems. Typical applications include lifting and handling, forming and shaping, vacuum packing, preservation, freeze drying, pick and place and pneumatic conveying.
When benchmarked against oil-sealed and dry vane vacuum pumps currently available on the market, the GHS VSD+ pump is reported to offer a 50% reduction in noise levels, down to a whispering level of 51dB(A), meaning it can be sited on the factory floor without disturbing operators.
From a design viewpoint, the new range is based on Atlas Copco’s compressors, and provides a fully wired, complete system in a single housing, with all access points for service on the same side. Due to its plug-and-play design the GHS VSD+ Series is easy and fast to install. The footprint is one of the smallest on the market, being no larger than a standard pallet.
The new range offers energy recovery features on the larger models, which leads to minimal hot air carry-over in the workplace and air-conditioned production environments.
The complete GHS VSD+ range is equipped with Atlas Copco’s Elektronikon monitoring system and SMARTlink data monitoring. Elektronikon can integrate with the customer’s plant management system and control other vacuum pumps, helping with energy savings. The efficiency credentials of the range are evidenced by conformance with ISO 50001 and 14001 standards, while environmental impact is reduced as a result of impeccable oil retention at all operating pressures – from ultimate pressure to atmospheric pressure.
- Oil-free rotary screw air compressors
- Helping companies to cut their costs
- Distributor appointed
- Air for energy project
- Quiet compressors – the key to reducing factory noise emissions
- Specifying a compressor: To hire or to buy?
- Latest Atlas Copco Class 2 Dryers Deliver Compliance Without the Cost
- Looking to the future
- Energy recovery
- Tips on specifying a stationary air compressor