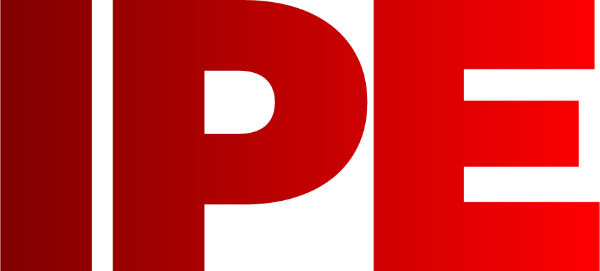
![]() |
Edward Lowton
Editor |
![]() ![]() |
Home> | Health, Safety & Welfare | >Plant and machinery safety | >Managing risks |
Managing risks
03 March 2016
It is common for machinery owners to assume that if their equipment has the CE marking then no further action is required. However, the Work Equipment Directive, which is implemented in the UK by the Provision and Use of Work Equipment Regulations 1998 (PUWER), applies to all work equipment regardless of its age, including equipment that carries the CE marking. Neil Dyson explains more
PUWER describes what an employer needs to do to protect employees in the workplace. It is therefore their responsibility to ensure that all machinery meets the requirements of the Machinery Directive and PUWER, of which risk assessments are an essential ingredient.
To immediately identify any issues, a risk assessment should be completed before any new machinery goes into operation. Problems can then be rectified with the manufacturer, so that they or the machinery owner no longer run the risk of a prosecution under the Machinery Directive or PUWER.
The Health & Safety Executive (HSE) states that if changes to machinery “are very substantial it may amount to being considered a "new" machine (or new assembly), for which you must undertake conformity assessment”.
The HSE goes on to state that even if changes to machinery are not substantial, such as refurbishment, the owner must still ensure that it continues to meet the requirements of PUWER, as well as any other requirements which may also apply to the product.
Assessing risk
The first step is to identify anything that has the potential to cause harm. Secondly, an assessment must be made of the likelihood of a person coming into contact with these hazards and how much damage it would cause.
Examples of hazards that have the potential to do harm include:
• A manipulating robot
• A moving conveyor
• A pallet wrapper
A risk assessment would normally be carried out for each hazard identified. The Preliminary Hazard Analysis (PHA) method uses a Hazard Rating Number system. Referencing a table, the most appropriate phrase that applies to the hazard is chosen, the corresponding score results in a hazard rating number (HRN), which corresponds to the level of risk.
The PHA takes into consideration:
• Likelihood of a person or persons coming into contact with a hazard
• Degree of possible harm that could be caused
• Frequency of exposure
• Number of people at risk at the same time
Control measures can then be applied to mitigate the risk:
• Design the hazard out.
• Remove the need for man-machine interface.
• Design-in safeguards.
• Reduce the possibility of occurrence.
• Reduce the degree of harm.
• Warn and inform machine operators (but only if you can achieve adequate safety).
Once the control measures have been implemented, a re-assessment must then be actioned to ensure that they provide an adequate level of safety. The process is repeated until an adequate level of safety is achieved.
Section 6 of PUWER requires that inspections must be repeated ‘at suitable intervals’ if machines are exposed to conditions that may lead to deterioration. Although, risk assessments must therefore be conducted at appropriate intervals, it is not uncommon for sites to fail to take any action for five years or more.
The answer here is to set up an internal process, overseen by an individual who is responsible for ensuring that risk assessments are carried out according to an agreed schedule. Creating an internal procedure in this way successfully integrates risk assessment into the everyday working practices.
PUWER requires that the persons who determine the nature of the assessments, and carry them out should be competent to do so. However, the failures we see on site are often due to a lack of appropriate internal expertise and physical resource to do an in-depth and correct assessment of all machinery. A decision to ‘make do’ or not invest in the appropriate expertise could result in expensive fines or – worse still – prove fatal to machinery users.
Neil Dyson is business line manager for machinery safety at TÜV SÜD Product Service, a global product testing and certification organisation.
- TÜV SÜD's Machinery Division appoints chief engineer
- Machinery risk assessment system
- Notified Body
- Machinery fire safety: Protecting lives and assets
- Effective machinery compliance project management
- Vibration shaker
- Enabling smart factory interoperability
- Keeping pace with machinery functional safety innovation
- Ensure that change is for the good
- UCPD safety courses