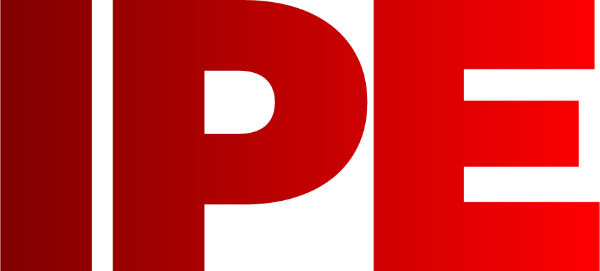
![]() |
Edward Lowton
Editor |
![]() ![]() |
Home> | Plant, Process & Control | >Sensors and instrumentation | >Enabling smart manufacturing |
Enabling smart manufacturing
04 August 2016
As well as having more than 350 different models incorporating IO-Link and two million IO-Link- enabled devices, ifm electronic has the ability to feed all the diagnostic data to the ERP system in parallel to the machine control to enable smart manufacturing.
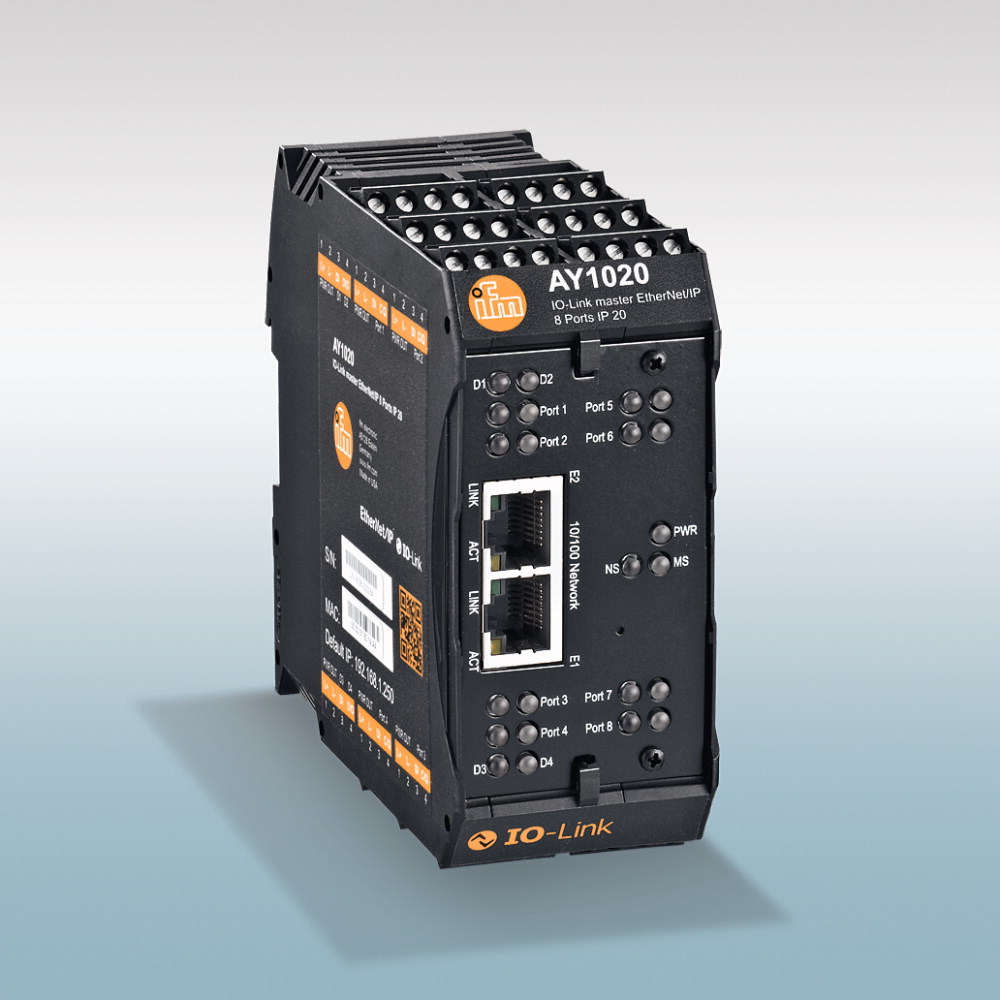
This allows the machine control plc to use sensor data while simultaneously the machine status, events and diagnostics can be logged in real time. Productivity data is live and maintenance scheduled as needed. IO-Link allows each and every sensor to be identified, and the master stores parameters to make swap-out much easier. If a recipe or an operation is changed, the plc can reconfigure any IO-Link device in an instant.
The AY IO-Link master operates as an input/output card with a total of 20 I /O, of which 8 are for IO-Link devices and the rest for binary signals. All signals can be easily transmitted to compatible controllers via the standard fieldbuses EtherNet /IP or
Profinet.